Rockwell Automation 193-EC1_2_3_5, 193-ECPM,592-EC1_2_3_5 E3 and E3 Plus Solid-State Overload Relay User Manual User Manual
Page 223
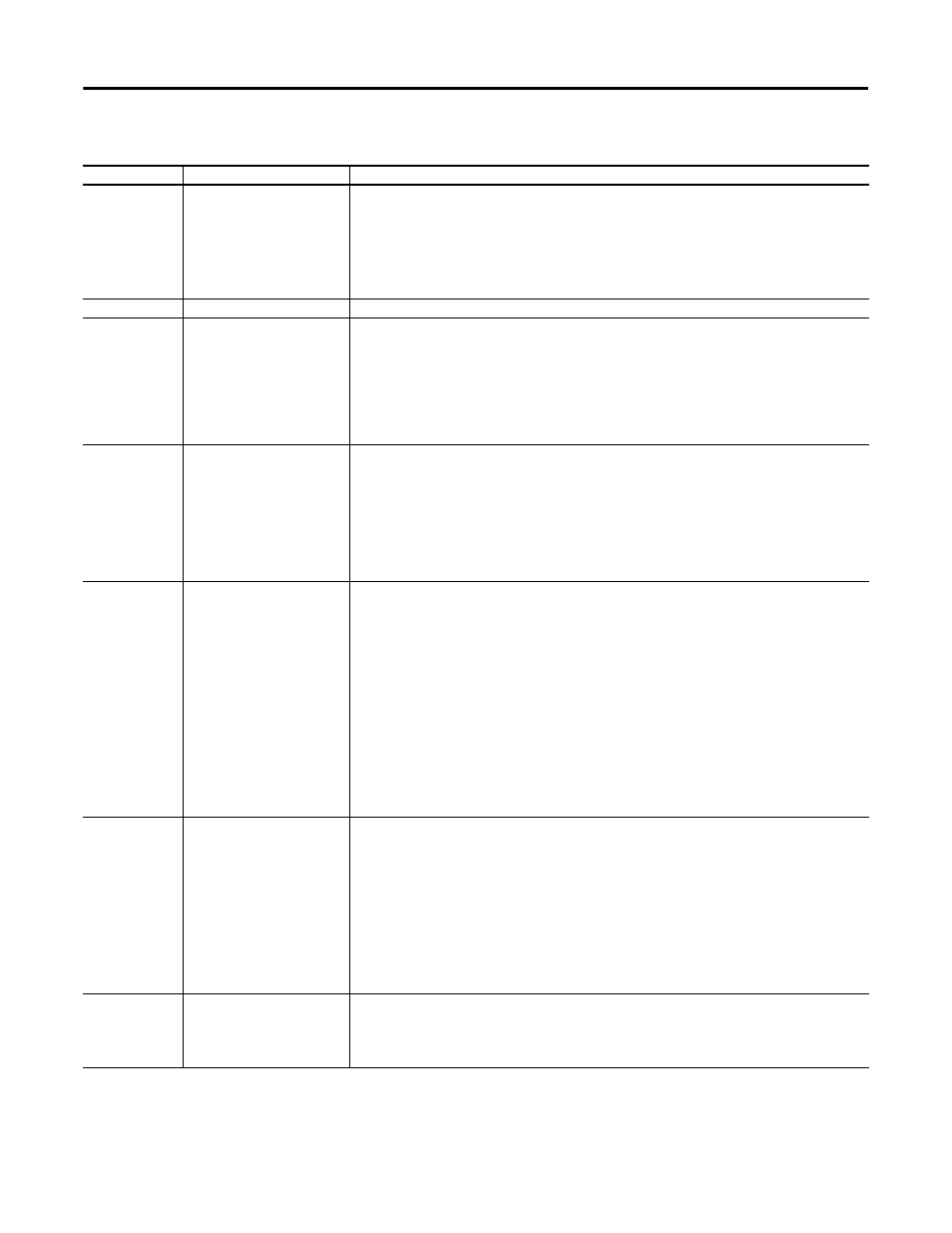
Rockwell Automation Publication 193-UM002I-EN-P - December 2011
223
Troubleshooting Chapter 12
Table 15: Input and Output Troubleshooting Procedures
➊ FRN 2.000 and later.
E3 Plus Model EC5 Only
➌The E3 Trip Relay contacts will not close until 2.35 seconds after power is applied to the E3 Overload Relay
DeviceNet connector. If a “Non-Volatile Fault” previously existed or a fault condition is present during
power-up, the trip relay contacts will not close until the fault condition is removed and the trip is reset.
Failure Type
Failure Description
Corrective Action
Input 1...4
Input 1,2,3 or 4 does not
appear to recognize a contact
closure
1. Check the supply voltage on the DeviceNet connector.
2. If the applicable contact closes but the E3 Overload Relay Input does not recognize the closure, check
the continuity and wiring to the connected contact.
3. Check the IN 1,2,3 and 4 status LEDs. If the appropriate LED does not illuminate, measure the voltage
across and current through the applicable input. Verify they are within the ratings of the E3 Overload
Relay (See Appendix A).
4. If the appropriate Input LED does illuminate, but the input status is not reported properly over the
DeviceNet network, check the programmable controller ladder logic and I/O mapping.
Input 1
Trip reset operation
1. Check the programming of Parameter 77, IN1=Trip Reset ➊
Input 5…6
Input 5 or 6 does not appear
to recognize a contact closure
1. Check the supply voltage on the DeviceNet connector.
2. If the applicable contact closes but the E3 Overload Relay Input does not recognize the closure, check
the continuity and wiring to the connected contact.
3. Check the state of the inputs by monitoring bits 10 and 11 of Parameter 21, Device Status, using
RSNetWorx for DeviceNet or a 193-DNCT (DeviceNet Configuration Terminal). If the appropriate bit is
not set, measure the voltage across and current through the applicable input. Verify that they are
within the ratings of the E3 Overload Relay (See Appendix A).
4. If the appropriate input status is not reported properly over the DeviceNet network, check the
programmable controller ladder logic and I/O mapping.
Trip Relay➌
The trip relay does not appear
to be functioning properly
1. Check the TRIP/WARN and NETWORK STATUS LEDs, or the DEVICE STATUS and TRIP STATUS
parameters. If a Protection Fault exists, refer to the Trip and Warning troubleshooting procedure. If a
DeviceNet-related fault exists, refer to the DeviceNet troubleshooting procedure.
2. Press the Test/Reset button on the E3 Overload Relay. The trip relay should open and the TRIP/WARN
LED should exhibit a single red flash code. Remove the control circuit power and measure the
impedance across terminals 95 and 96 to verify the trip relay contacts are open. Press the Test/ Reset
button again. The unit should reset and the trip relay contacts should close. Measure across terminals
95 and 96 to ensure the trip relay contacts closed.
3. Remove control circuit supply power and check the control wiring to the E3 Overload Relay Trip Relay
(95/96).
OUT A or OUT B
Output A or Output B does
not appear to turn on (close)
when commanded to do so
1. Check the supply voltage on the DeviceNet connector.
2. Check the OUTA and OUTB status LEDs. If the appropriate LED does not illuminate, check the
programmable controller ladder logic and I/O mapping.
3. If the appropriate Output LED is illuminated, remove the control circuit power and check for
continuity across the appropriate output terminals (13/14 for OUTA, 23/24 for OUTB). If the continuity
test indicates the output is open, replace the E3 Overload Relay. Check the supply voltage against the
ratings of the contactor and the relay output before installing a new unit.
4. Remove control circuit power and check the control circuit fuse and the control wiring to the E3
Overload Relay output terminals.
5. Check the control circuit power supply. Verify the voltage is within the contactor and overload relay
ratings.
6. Check the TRIP/WARN and NETWORK STATUS LEDs, or the DEVICE STATUS and TRIP STATUS parameters.
If a Protection Fault exists, refer to the Trip and Warning troubleshooting procedure. If a
DeviceNet-related fault exists, refer to the DeviceNet troubleshooting procedure.
7. Check the OUTA and OUTB Pr FltState, Pr FltValue, Dn FltState, Dn FltValue, Dn IdlState, and Dn
IdlValue programmable parameters. The Pr FltState and Pr Flt Value parameters supersede the Dn Flt
or Dn Idle parameters.
OUT A or OUT B
Output A or Output B does
not appear to turn off (open)
when commanded to do so.
1. Check the OUTA and OUTB status LED’s. If the appropriate LED remains illuminated, check the
programmable controller ladder logic and I/O mapping.
2. If the appropriate Output LED is not illuminated, remove the control circuit power and check for
continuity across the appropriate output terminals (13/14 for OUTA, 23/24 for OUTB). If the continuity
test indicates the output is closed, replace the E3 Overload Relay. Check the supply voltage against
the ratings of the contactor and the relay output before installing a new unit.
3. Remove control circuit power and check the control circuit fuse and the control wiring to the E3
Overload Relay output terminals.
4. Check the OUTA and OUTB Pr FltState, Pr FltValue, Dn FltState, Dn FltValue, Dn IdlState, and Dn
IdlValue programmable parameters. Then check the TRIP/WARN and NETWORK STATUS LEDs, or the
DEVICE STATUS and TRIP STATUS parameters. If a Protection Fault exists, refer to the Trip and Warning
troubleshooting procedure. If a DeviceNet-related fault exists, refer to the DeviceNet troubleshooting
procedure.
OUT A or OUT B
The contactor connected to
Output A or Output B appears
to “chatter”
1. Verify the OUT A or OUT B LED remains in the appropriate On or Off state. If the LED is flickering,
check the programmable controller’s ladder logic program.
2. Check the control circuit supply voltage. Verify it is within the ratings of the contactor coil and the
overload relay’s outputs.
3. Remove the control circuit power. Verify all control wiring is properly secured.