Trip/warn led troubleshooting procedures – Rockwell Automation 193-EC1_2_3_5, 193-ECPM,592-EC1_2_3_5 E3 and E3 Plus Solid-State Overload Relay User Manual User Manual
Page 218
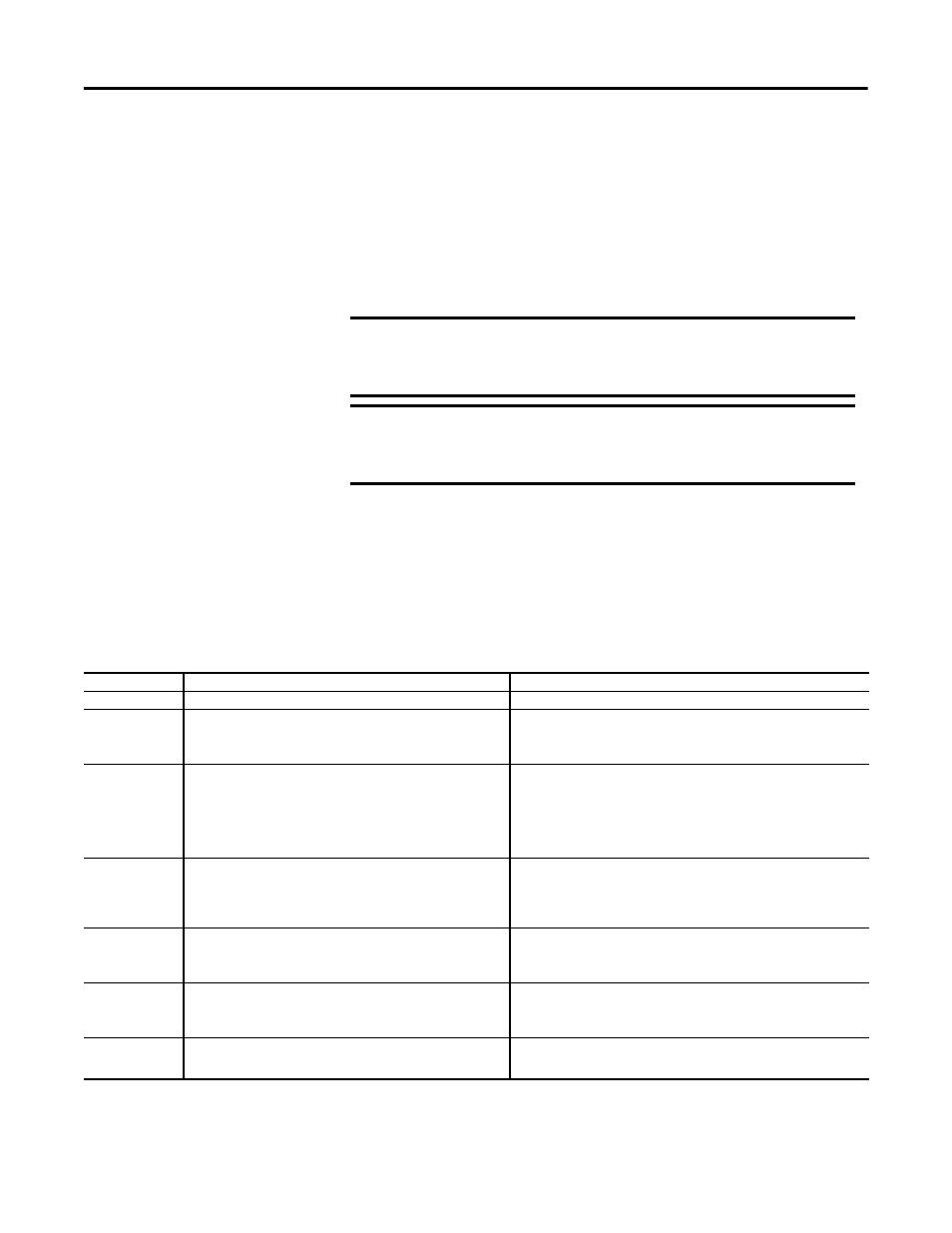
218
Rockwell Automation Publication 193-UM002I-EN-P - December 2011
Chapter 12 Troubleshooting
6.
Setting Parameter 30,
OL/PTC ResetMode, to the “Automatic” selection to
allow the unit to automatically reset after overload and thermistor (PTC)
trips.
7.
Cycling supply power to the E3 Overload Relay to clear Non-Volatile
Faults.
8.
Setting Parameter 26,
Trip Reset, to a value of 1 = trip reset.
Trip/Warn LED
Troubleshooting
Procedures
The following table lists the possible causes for each trip type and the
recommended action to take.
Table 10: Trip/Warn LED Troubleshooting Procedures
IMPORTANT
An overload trip cannot be reset until the value of Parameter
9,% Therm Utilized, is below the value set in Parameter 31, OL
Reset Level.
IMPORTANT
A PTC trip cannot be reset until the motor has cooled
sufficiently for the resistance of the PTC detector to drop
below the E3 Plus Overload Relay’s PTC Reset Resistance level.
Trip Description Possible Cause
Corrective Action
Test Trip
1. Operation of the Test/Reset button
1. Operate the Test/Reset button to clear the trip.
Overload
1. Motor overloaded
2. Improper parameter settings
1. Check and correct source of overload (load, mechanical transmission
components, motor bearings).
2. Set parameter values to match the motor and application
requirements.
Phase Loss
1. Missing supply phase
2. Poor electrical connection
3. Contactor operation
4. Improper parameter setting
1. Check for open line (i.e. blown fuse).
2. Check all power terminations from the branch circuit-protecting
device down to the motor for proper tightness. Ensure that the
overload connection to the contactor is secure.
3. Inspect contactor for proper operation.
4. Single-phase applications require that Parameter 27, Single/Three Ph,
is set to “single phase”.
Ground Fault
1. Power conductor or motor winding is shorting to ground
2. Motor winding insulation is decayed
3. Foreign Object short
4. External ground fault sensor (core balance current
transformer) has improper connection
1. Check power conductors and motor windings for low resistance to
ground.
2. Check motor winding insulation for low resistance to ground.
3. Check for foreign objects.
4. Check cable connections.
Stall
1. Motor has not reached full speed by the end of the Stall Enabld
Time (Parameter 39)
2. Improper parameter settings
1. Check for source of stall (i.e. excessive load, or mechanical
transmission component failure).
2. Parameter 39, Stall Enabld Time, is set too low for the application.
Check to ensure that Parameter 28, FLA Setting, is set correctly.
Jam
1. Motor current has exceeded the programmed jam level
2. Improper parameter settings
1. Check for the source of the jam (i.e., excessive load or mechanical
transmission component failure).
2. Parameter 43, Jam Trip Level, is set too low for the application. Check
to ensure that Parameter 28, FLA Setting, is set correctly.
PTC
1. Motor stator windings overheated
2. Thermistor leads short-circuited or broken
1. Check for source of motor overtemperature (i.e. overload, obstructed
cooling, high ambient temperature, excessive starts/hour).
2. Inspect thermistor leads for short-circuit or open