Festo Электромотор MTR-DCI User Manual
Page 106
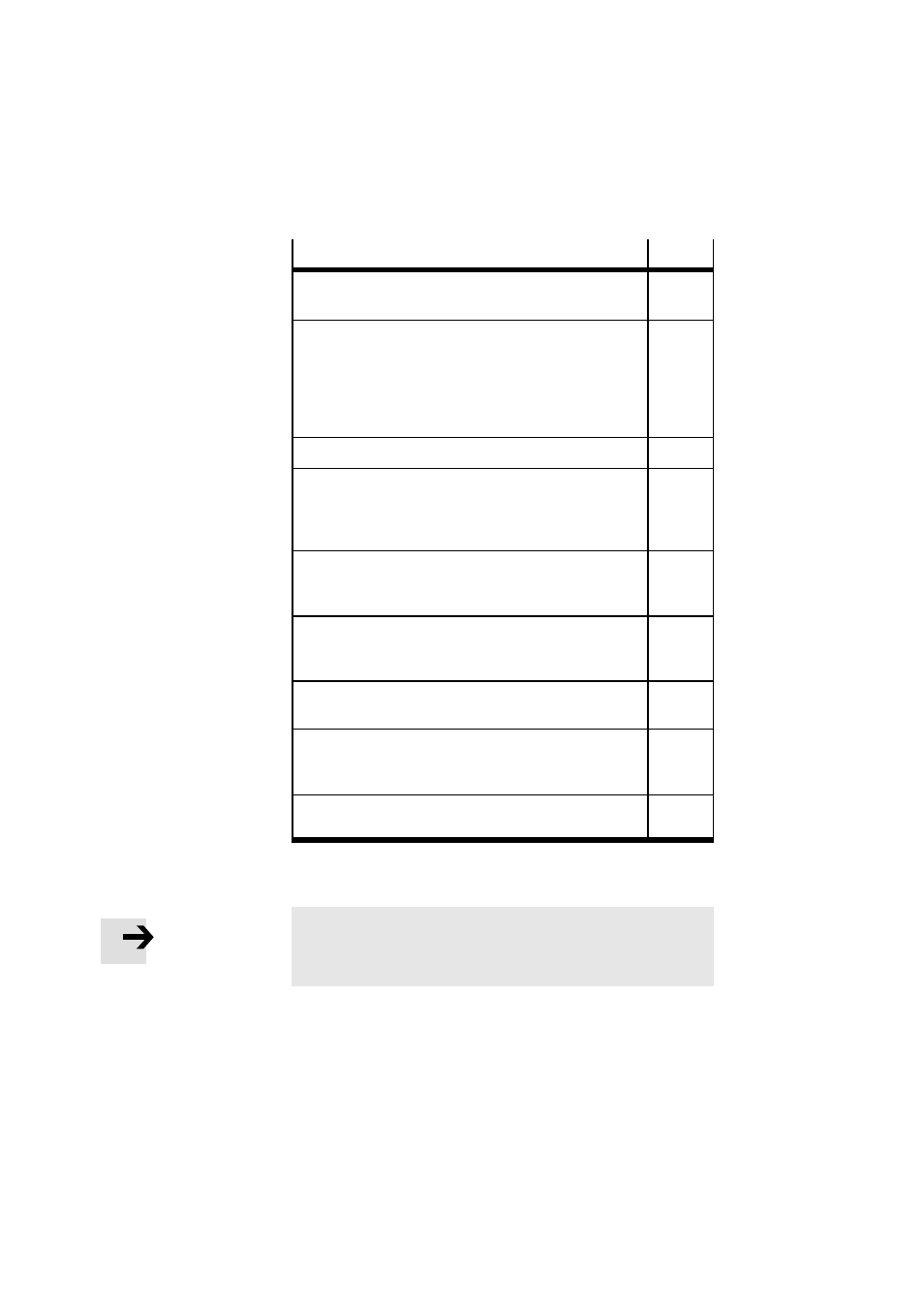
5. Commissioning
5-8
Festo P.BE-MTR-DCI-CO-EN en 1209a
Commissioning (overview)
Chapter
1. Select the drive type and, if necessary, adapt the
parametrizing to suit your axis.
5.2.1
2. Set the following parameters for homing:
– Reference travel method,
– Search speed to reference point,
– Positioning speed to axis zero point,
– With “Fixed stop ...” homing method:
Teach an axis zero point ≠ 0.
5.2.2
3. Carry out a reference run.
5.2.3
4. Teach the following axis parameters for defining
the axis zero point and the working area:
– Offset of the axis zero point to the reference point,
– Positive and negative software end positions.
5.2.4
5. Enter several position sets (target position,
positioning mode, positioning speed and
accelerations).
5.2.5
6. Carry out a test run to check the positioning reaction
of the axis, as well as the basis coordinates and the
working area.
5.2.6
7. If necessary, optimize the settings for position sets as
well as for the basis coordinates and the working area.
5.2.5
8. Commission the CAN interface of the MTR-DCI.
This step can be the first one.
5.2.7
and
5.4.1
9. Before completing commissioning, note the instruc-
tions on operation.
5.7
Tab. 5/1: Commissioning steps
Note
The project zero point PZ can only be set via FCT or
CANopen/CI object 21F4
h
(FHHP PNU 500).