415 appendix axis-specific parameters – IAI America SSEL User Manual
Page 437
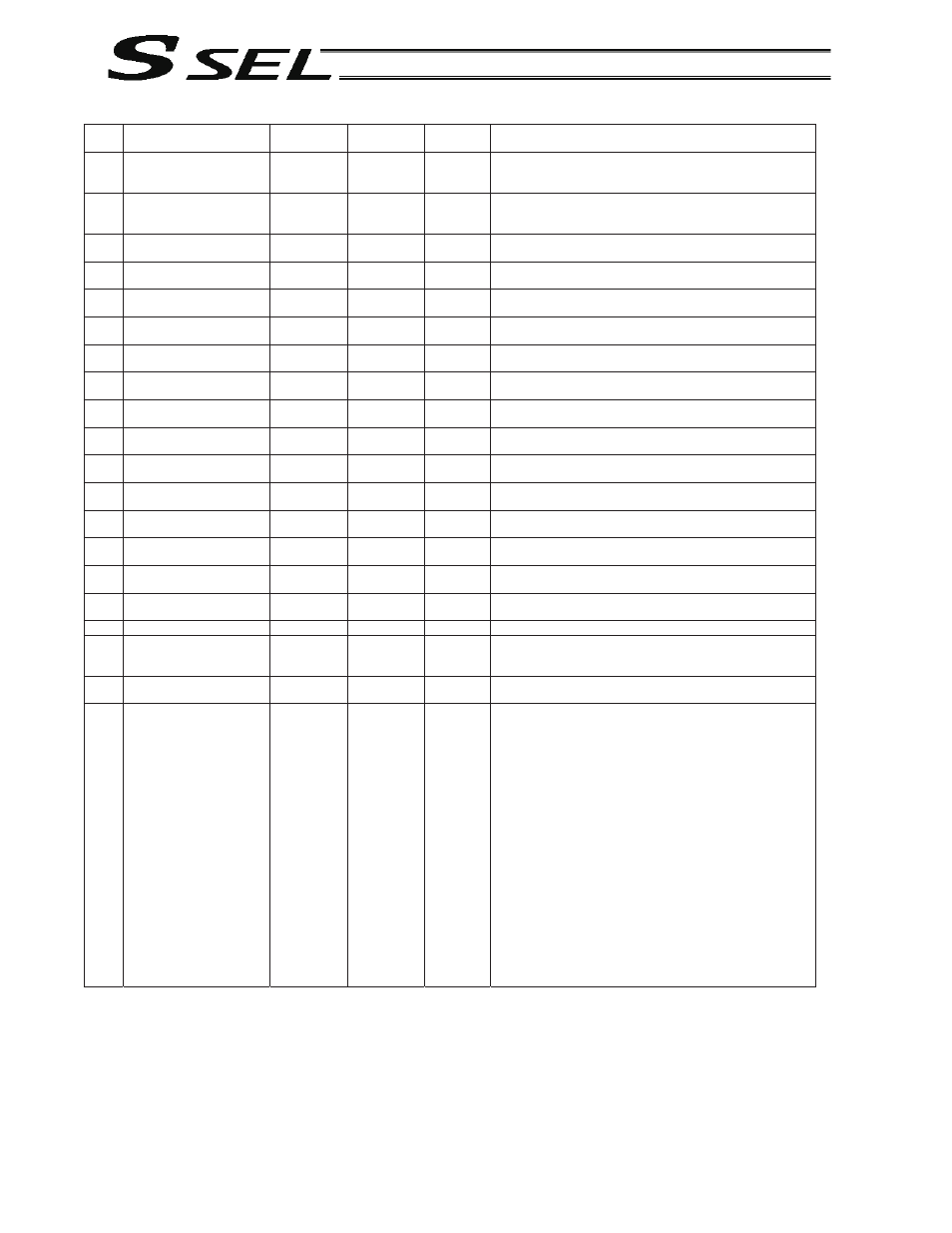
415
Appendix
Axis-Specific Parameters
No Parameter
name
Default value
(Reference)
Input range
Unit
Remarks
83 Absolute
synchro
slave-
axis initialization
cancellation
0
0 ~ 5
Valid only with a synchro slave axis.
84 Maximum
synchronization
correction speed of
synchro slave axis
5
0 ~ 100
mm/sec
Maximum travel speed for synchronization position
correction of slave axis. Valid only with a synchro slave axis.
* Note: Not limited by the safety speed.
85 Home-return
acceleration/deceleration
15
1 ~ 300
0.01 G
86
Zone 1 MAX
0
-99999999 ~
99999999
0.001 mm
Valid only when MAX > MIN. * Must be inside the range for
at least 3 msec.
87
Zone 1 MIN
0
-99999999 ~
99999999
0.001 mm
Valid only when MAX > MIN. * Must be inside the range for
at least 3 msec.
88
Zone 1 output number
0
0 ~ 899
Physical output port or global flag (Output is invalid if “0” is
input; multiple specification is invalid)
89
Zone 2 MAX
0
-99999999 ~
99999999
0.001 mm
Valid only when MAX > MIN. * Must be inside the range for
at least 3 msec.
90
Zone 2 MIN
0
-99999999 ~
99999999
0.001 mm
Valid only when MAX > MIN. * Must be inside the range for
at least 3 msec.
91
Zone 2 output number
0
0 ~ 899
Physical output port or global flag (Output is invalid if “0” is
input; multiple specification is invalid)
92
Zone 3 MAX
0
-99999999 ~
99999999
0.001 mm
Valid only when MAX > MIN. * Must be inside the range for
at least 3 msec.
93
Zone 3 MIN
0
-99999999 ~
99999999
0.001 mm
Valid only when MAX > MIN. * Must be inside the range for
at least 3 msec.
94
Zone 3 output number
0
0 ~ 899
Physical output port or global flag (Output is invalid if “0” is
input; multiple specification is invalid)
95
Zone 4 MAX
0
-99999999 ~
99999999
0.001 mm
Valid only when MAX > MIN. * Must be inside the range for
at least 3 msec.
96
Zone 4 MIN
0
-99999999 ~
99999999
0.001 mm
Valid only when MAX > MIN. * Must be inside the range for
at least 3 msec.
97
Zone 4 output number
0
0 ~ 899
Physical output port or global flag (Output is invalid if “0” is
input; multiple specification is invalid)
98 ~
99
For future expansion
0
100 (For
expansion)
0
101
Allowable time to exceed
continuous-operation
enable torque
0
0 ~ 300
0 sec: Do not monitor the time during which the continuous-
operation enable torque is exceeded
(Main application version 0.17 or later)
102 ~
103
(For expansion)
0
104 Multi-slider
near-miss
detection target axis
specification
OH OH
~
FFFFFFFFH
Bits 0 to 3: Axis number of the paired axis to perform near-
miss detection against (on the positive side of
the coordinate system of the applicable axis)
Bits 4 to 7: Axis number of the paired axis to perform near-
miss detection against (on the negative side of
the coordinate system of the applicable axis)
* This parameter must be input for the paired
axis, as well. (For the purpose of
convenience, the axis with the younger axis
number is deemed the main multi-slider axis
in the pair.)
* This parameter can be specified only for an
axis whose resolution characteristics are the
same as those of the applicable axis.
* With the SSEL controller, the multi-slider
near-miss detection function cannot be used if
the synchro specification is selected.
* If no adjacent slider is present on the
corresponding moving side of the coordinate
system of the applicable axis, set “0.”
(Main application version 0.12 or later)