Parameters, Details of each input signal – IAI America SSEL User Manual
Page 334
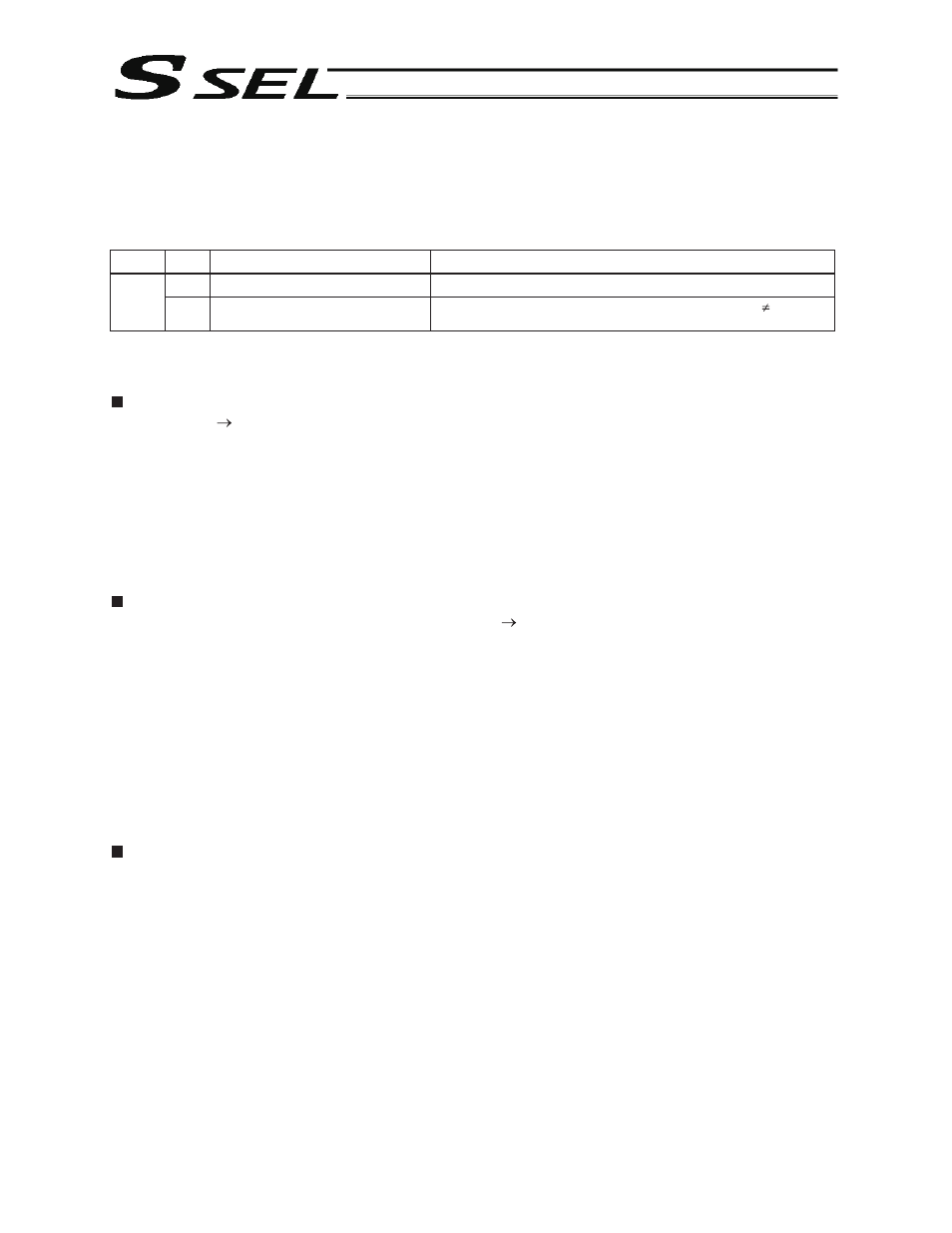
312
Part 3 Positioner Mode
2.
Parameters
To use the controller in the standard mode, set other parameter No. 25 to “1.”
Position numbers are specified as binary codes according to the factory setting. To change the input mode
to BCD, set a value “other than 0” in other parameter No. 25.
No.
Parameter
Function
25
Operation mode type
1: Standard mode
Other
71
Positioner mode parameter 1
Position-number input mode specification (0: Binary,
0: BCD)
* Default value: 0 (Binary)
3.
Details of Each Input Signal
Start (CSTR) : Controller Capable for Memory Capacity Increase
When the OFF
ON leading edge of this signal is detected, the controller will load the target point
number specified by the 16-bit binary code consisting of PC1 through PC16, and perform positioning to
the target position specified by the corresponding position data.
Before movement is started, the target position, speed and other operation data must be set in the
position table using a PC or teaching pendant.
If this signal is input when no single home-return operation has been performed after the power was input
(= when the HEND output signal is OFF), “C6F, Home-return incomplete error” will generate.
Command position number (PC1 through PC16) : Controller Capable for Memory Capacity Increase
When a movement command is executed upon the OFF
ON edge of the start signal, the controller will
load the command position number specified by the 16-bit binary code consisting of signals PC1 through
PC13.
The weight of each bit is as follows: 2
0
for PC1, 2
1
for PC2, 2
2
for PC3, 2
3
for PC4, 2
4
for PC5, ..., and 2
10
for PC11. By combining these bits, any position number between 1 and 20000 (maximum) can be specified.
The input mode can be changed to BCD by changing the setting of other parameter No. 71, as follows:
Other parameter No. 71 = 1 (BCD input)
(Default setting of other parameter No. 71 = 0 (Binary input))
In the BCD input mode, PC1 through 4 indicate the one’ s place, PC5 through 8 indicate ten’ s place, PC9
through 12 indicate the hundred’ s place, and PC13 indicates the thousand’ s place.
Pause (*STP)
If this signal turns OFF while the actuator is moving, the controller will cause the actuator to decelerate to
a stop.
The remaining travel distance will be held, which means that when the signal turns ON again, the actuator
will resume movement of the remaining travel distance.
To cancel the movement command altogether after turning OFF the pause signal, turn ON the
cancellation signal while this signal is OFF to cancel the remaining travel distance.
The pause signal can be used for the following purposes:
[1]
As a sensor to detect entry into a specified area around the system or for other lower-level safety
measures to stop the axis while the servo is on
[2]
To prevent contact with other equipment
[3]
For positioning based on sensor or LS signal detection
has not yet contacted the mechanical end. If the signal is input after the actuator has reversed
upon contacting the mechanical end, home return will be performed again.
(Note) For the controller not capable for the memory capacity increase, it is PC1 to PC13 and 1 to
1500 positions.
(Note) For the controller not capable for the memory capacity increase, read the target point by the binary
code of the 13 bits in PC1 to PC13.
(Note) When this signal is input during home return, the movement command will be held if the actuator