Retrotec USACE User Manual
Page 68
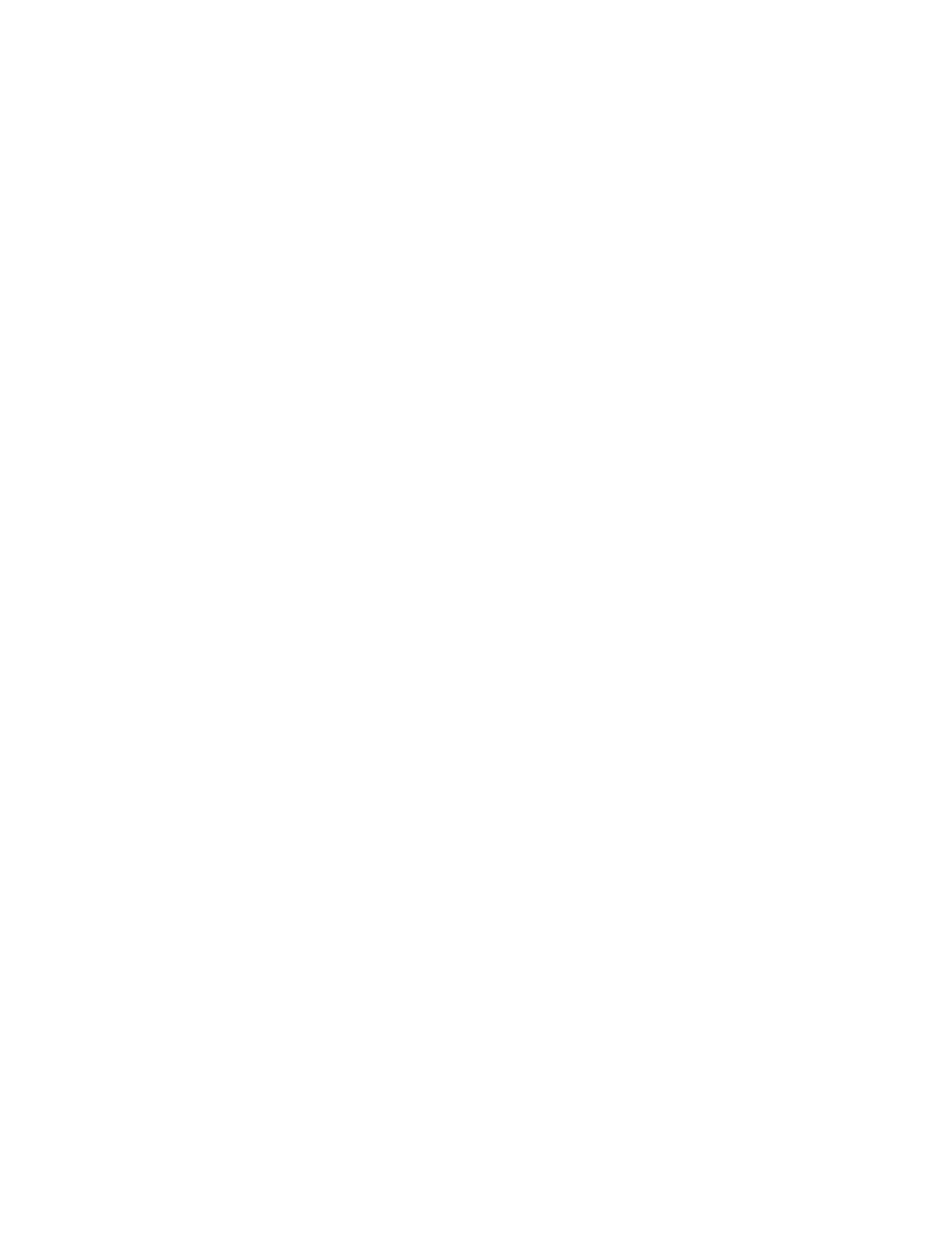
46 ENERGY & PROCESS ASSESSMENT PROTOCOL
The energy assessment team has to keep in mind the original aim of the
assessment, which may not be to identify all saving opportunities, but to
concentrate on low-hanging fruit and no-cost measures. Identifying no-cost
measures is usually fairly easy: they are usually things related to operation
schedules, setpoints, and operation of energy-using systems. Identifying long-
payback measures is usually easy, too: those systems need thorough improve-
ment (change of boiler, installing a new chiller with free cooling, replacement
of windows, etc.).
The challenge that the auditor has is in assessing low- and medium-cost
saving potentials, that is, to estimate costs realistically, is to neither overesti-
mate savings nor underestimate investments.
Ending up with no saving potential is not unusual. If the building is very
simple and there are not many energy-using systems—or if a more complex
building is operated unusually well—there may not be any saving opportuni-
ties without major renovation. The comment from a client with a large building
stock is that zero potential is a good result: it shows that everything is working
as it should, and that the O&M staff knows what it is doing.
There are four key rules for the energy conservation measure analysis that
the auditor should keep in mind:
Do not be too optimistic. (Do not overestimate the savings or underesti-
1.
mate the cost. Keep in mind the occupants’ level of comfort.)
Savings in one energy may increase the consumption of another (e.g.,
2.
lighting and heating are connected).
Check overlapping savings. If there are several saving measures for the
3.
same system (e.g., air-handling unit), defi ne the order for the implemen-
tation of the measures.
Cost savings: when to change the tariff—before or after the saving mea-
4.
sure. (One tariff may be optimal now, but not after the saving measure
has been implemented.)
When analyzing the saving potential, the auditor very often has to also
think about the lifetime of the surrounding technology to come up with
sensible ideas, taking into account the overall improvement needs of the
systems.
It is sometimes important to analyze the remaining life cycle of heating,
ventilation, process, and electrical systems. If the payback time of a suggested
energy conservation measure is long, perhaps 7–10 years or more, will the system
be operational by then, or will it require major renovation or renewal? Ventila-
tion and air-conditioning systems are probably the most critical in this respect.
The lifetime of control equipment and building automation system is 10–15
years; for fans and air handling units, 20–25 years. If the system is 15 years old
already, is it feasible to make improvements to improve energy effi ciency, or
would it be better to make a larger renovation now? This decision shall be made
based on the rough life cycle cost estimate based on the information obtained
during the energy assessment.