Retrotec USACE User Manual
Page 379
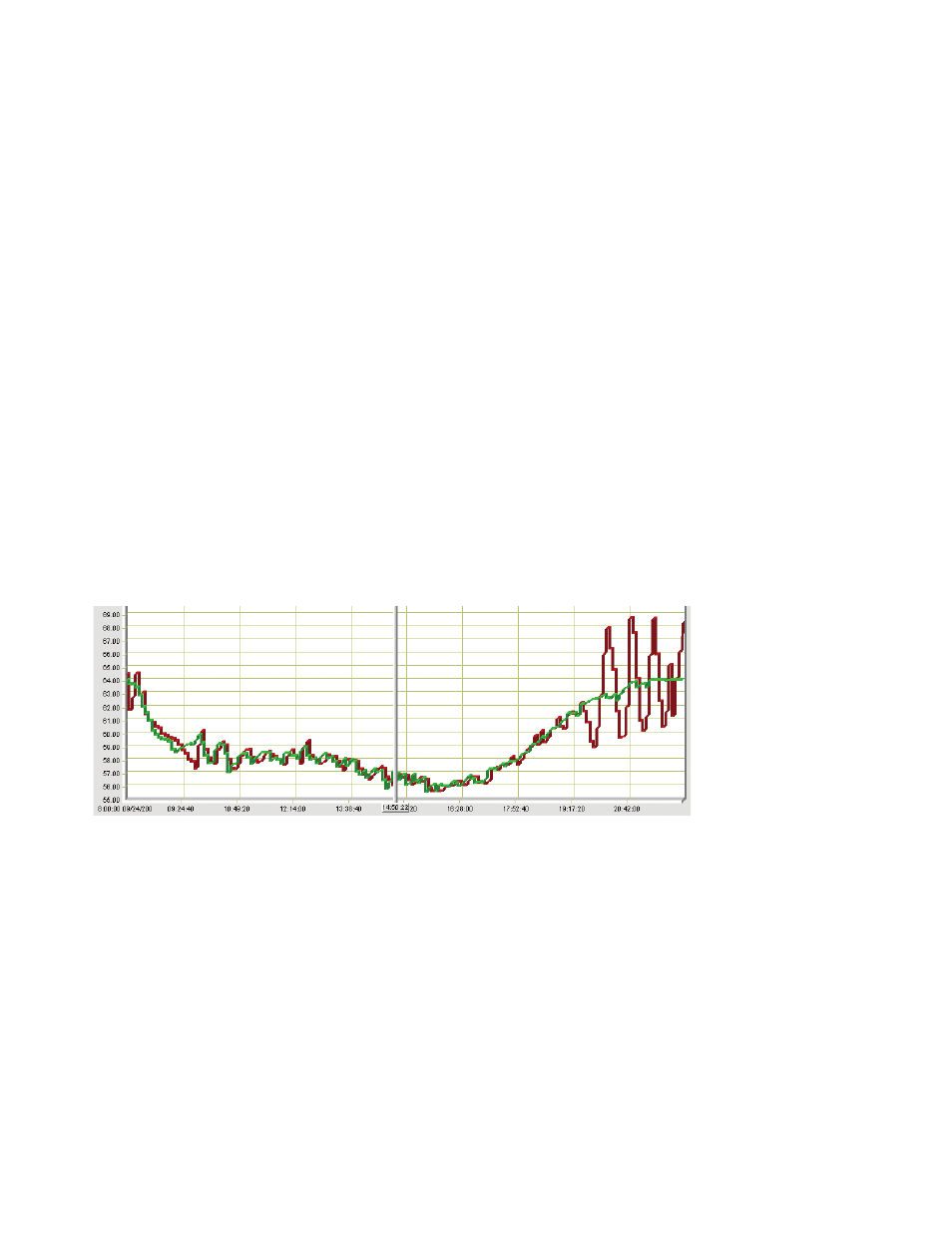
Appendix J J3
A reset strategy based on the needs of the end use loads can reduce pump
energy by 40% or more, depending upon the diversity of the loads.
Effi ciency and load-based reset strategies should be incorporated into the
control routines for the cooling towers. Reducing the condenser water supply
temperature (within reason and equipment limitations) can reduce energy
consumption on constant speed centrifugal chillers by up to 30%, and by up to
60% or more on variable speed centrifugal chillers.
An additional benefi t associated with resetting the chilled water supply
temperature and differential pressure is that cooling coil control valve response
and thus system temperature control are much better when these strategies
are incorporated.
When cooling loads are light but the differential pressure setpoint is at
275.8 kPa (40 PSID) and the CHWS temperature is at 5.6 °C (42 °F), most of
the cooling coil control valves will be operating at or near shutoff. Valves op-
erating near shutoff provide very imprecise temperature control, resulting in
large swings in the leaving air temperature from the air handling units, as well
as in over- and under-dehumidifi cation. If the CHWS temperature is increased
and the differential pressure is decreased, the valves will open up and operate
closer to midstroke or even further open, where their control can be very ac-
curate.
This is shown in the following trend of supply air temperature vs. supply air
temperature setpoint:
Figure J1. Trend of supply air temperature vs. supply air temperature setpoint. Red = supply air
temperature; green = supply air temperature setpoint.
During the day, the CHWS temperature setpoint and differential pressure
setpoint are reset based on the loads. At approximately 19:00, the system is op-
erated in a fi xed temperature and differential pressure (DP) setpoint mode. It
can be seen that the supply air temperature control stays within approximately
–17.5 °C (0.5 °F) until 19:00, when the swings exceed –15 °C (5 °F), due to the
CHW control valve at the AHU being near shutoff.
Optimized chiller equipment staging can reduce the energy consump-
tion penalty imposed by running too much constant speed equipment by
over 50%.