Retrotec USACE User Manual
Page 416
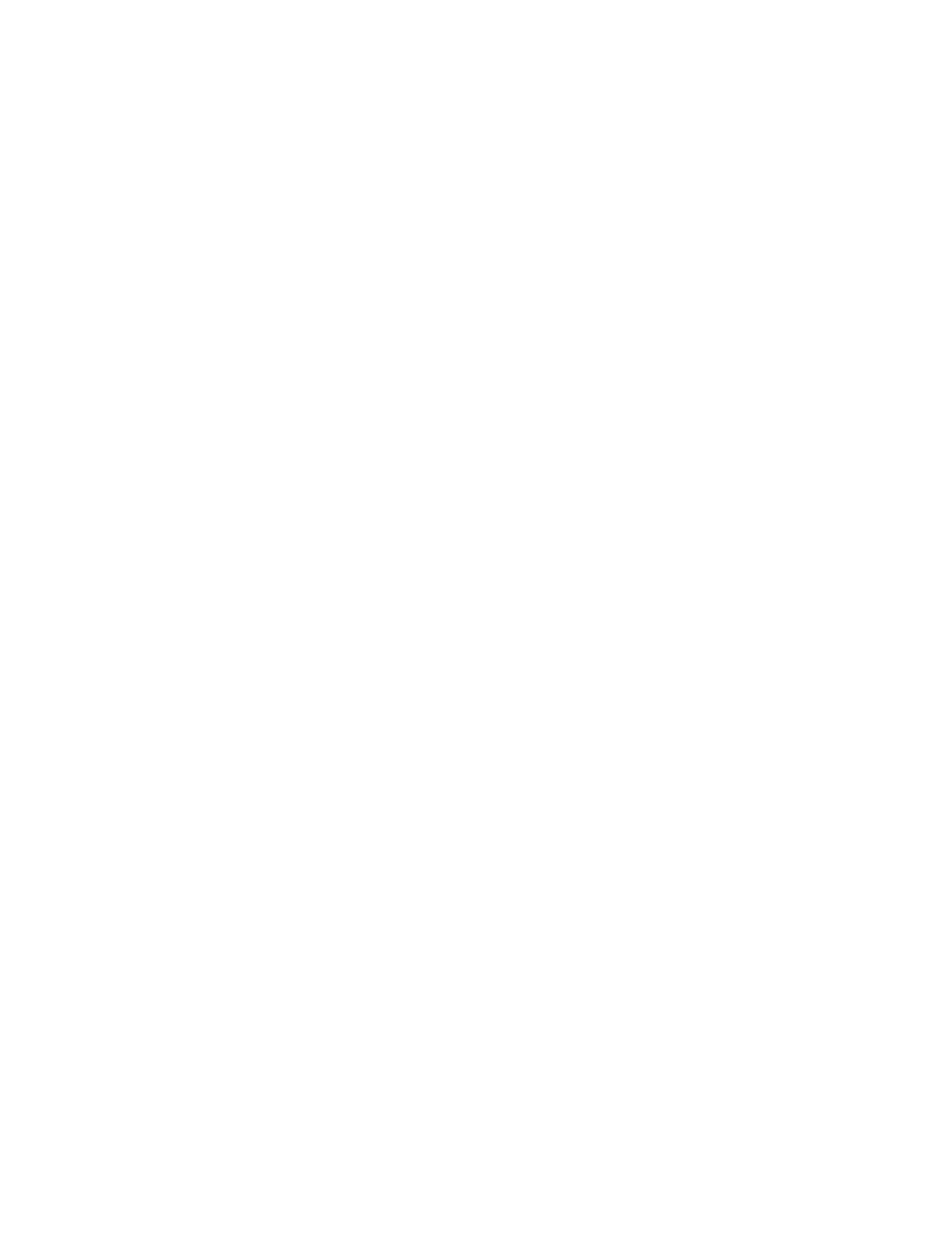
L16 ENERGY & PROCESS ASSESSMENT PROTOCOL
7.1.6 Use ultrafi ltration/reverse osmosis (UF/RO) for wastewater cleaning. When water-
based paint is used, processing equipment must be regularly cleaned with water. A typi-
cal painting operation requires a signifi cant amount of water to clean, and all of it must
be disposed of as hazardous waste. Reducing this hazardous waste therefore reduces
transportation and incineration energy associated with its removal. A combined UF/RO
process cleans waste water to the point where it is again suitable for cleaning purposes.
The UF/RO can recover 95% of the waste water.
7.1.7 Insulate the drying booth or tunnel. Insulation of the drying booth or tunnel can re-
duce heat losses through irradiation, which can be about 5% of the total energy input.
7.1.8 Fix badly functioning entry and exit doors of drying booths, which can cause additional
heat losses.
7.1.9 Enclose painting operation—e.g., in a booth—when possible.
7.2 Plaiting and Metal Finishing
7.2.1 Install emission “elimination” cover on Cr tank and reduce exhaust air fl ow rate when
the tank is covered.
7.2.2 Control exhaust airfl ows and steam heating on plating tanks.
7.2.3 Insulate plating tanks with surface temperature above 49 °C (120 °F).
7.2.4 Treat rinse water to recover valuable metals or chemicals to return to plating bath, with
clean water returned to rinse system.
7.2.5 Rinsing and cleaning: Install timers and tamper-proof conductivity controllers to con-
trol quality of water in rinses.
7.2.6 Rinsing and cleaning: Install ultrasonic cleaning equipment.
7.2.7 Rinsing and cleaning: Install water-saving technologies or modifi cations specifi cally
geared toward each facility. Examples are counter-current rinsing, drag-out tanks or
fi rst-stage static rinses, spray systems, and fl ow reduction devices.
7.2.8 Use no-mask anode tooling technology to reduce labor cost, plating time, and time
needed to grind the surface after plating. Reduction in plating time results in increased
throughput and reduced energy consumption (for tank heating and cooling and exhaust
air transportation and scrubbing).
7.3 Machining
7.3.1 Use process enclosures connected to exhaust systems or having built-in fans and fi lter
for turning (lathe), drilling, milling, and grinding machines. For older machines, use
partial enclosures or local capture hoods.
7.3.2 Use area lighting system in combination with task (supplemental) lighting for
workstations.