Retrotec USACE User Manual
Page 409
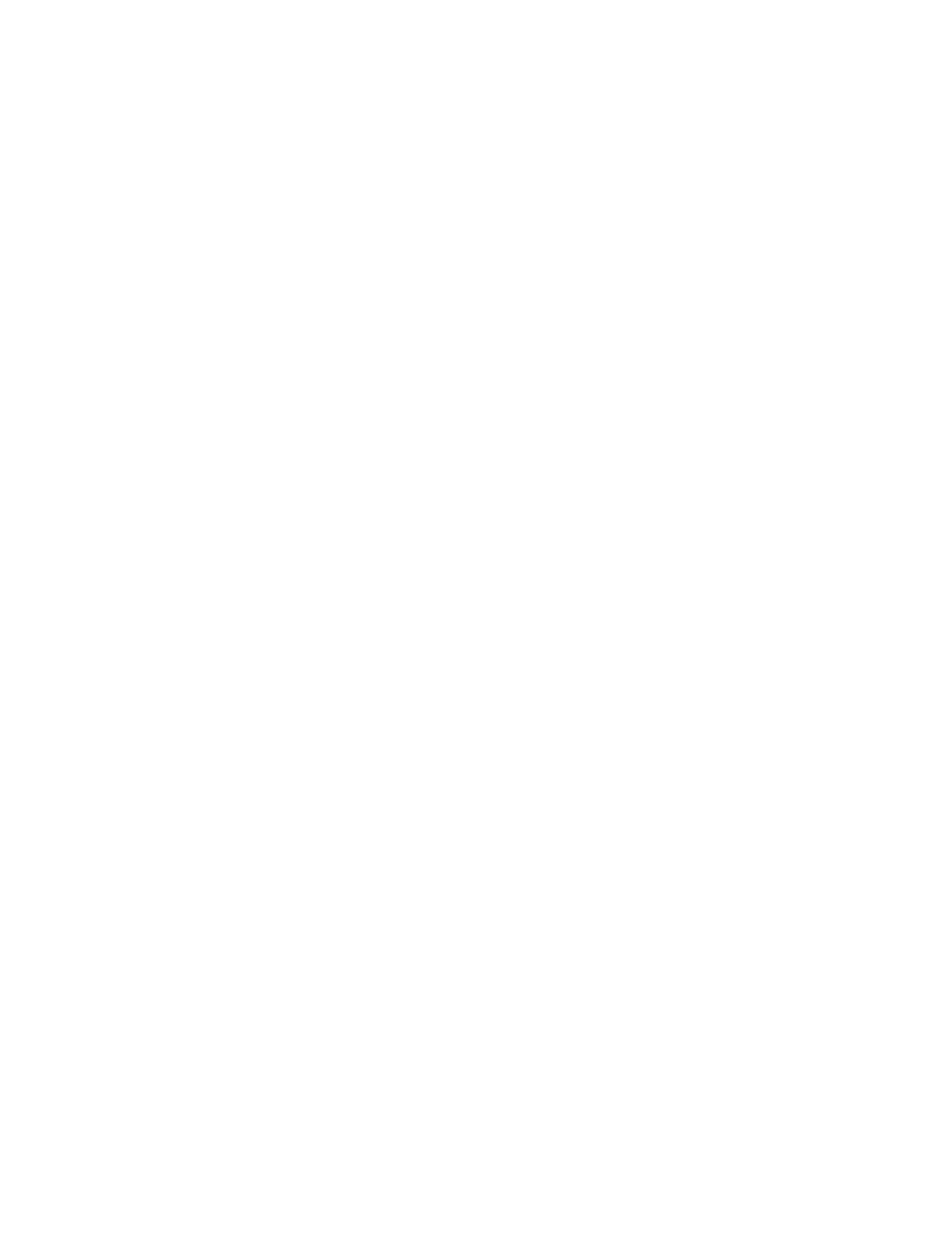
Appendix L L9
4.1.28 Reclaim incinerator heat.
4.1.29 Use hot water from boiler condensate to preheat air.
4.1.30 Boilers: Capture steam condensate for reuse.
4.1.31 Boilers: Install automatic controls to treat boiler makeup water.
4.1.32 Adjust boilers and air conditioner controls so that boilers do not fi re and compressors
do not start at the same time, but satisfy demand.
4.1.33 Check fl ue for improper draft.
4.1.34 Clean boiler surfaces of fouling.
4.1.35 Replace and resize boilers for effi ciency.
4.1.36 Shut down large boilers in summer and use small ones when possible.
4.1.37 Replace noncondensing boilers with condensing boilers (15–20% compared to new
standard).
4.1.38 Prevent dumping steam condensate to drain.
4.1.39 Survey and fi x steam/hot water/condensate leaks.
4.1.40 Convert steam system to low-temperature sliding temperature hot water system. Install
complementing steam boilers where needed.
4.1.41 Survey and replace failed steam traps.
4.1.42 Reduce excess air. Poorly maintained boilers can have up to 140% excess air. Reducing
the excess air to 15% (required for safety) can increase boiler effi ciency by 1% for each
15% reduction of excess air, for a 40 °F (22 °C) reduction in stack gas temperature.
4.1.43 Use smaller boiler when possible to operate below full load—e.g., install smaller boilers
for summer operations and to supplement winter operations.
4.1.44 Improve boiler insulation. It is possible to use new materials that insulate better and
have lower heat capacity. Savings of 6–26% can be achieved if this improved insula-
tion is combined with improved heater circuit control. Several case studies estimate an
average payback period for this measure of about 11 months.
4.1.45 Check steam trap sizes to verify they are adequately sized to provide proper condensate
removal.
4.1.46 Consider opportunities for fl ash steam use in low-temperature processes.
4.1.47 Consider pressuring atmospheric condensate return systems to minimize fl ash losses.
4.1.48 Consider relocation or conversion of remote equipment such as steam-heated storage.
4.1.49 Evaluate insulation of all uninsulated lines and fi ttings previously thought to be uneco-
nomic.
4.1.50 Evaluate potential for cogeneration in multipressure steam systems presently using
large pressure-reducing valves.
4.1.51 Evaluate production scheduling of batch operation and revise to minimize startups and
shutdowns.
4.1.52 Implement regular steam leak survey.
4.1.53 Install condensate return system.
4.1.54 Install cross-connect lines on steam distribution systems.