I.3 hvac & r systems – Retrotec USACE User Manual
Page 371
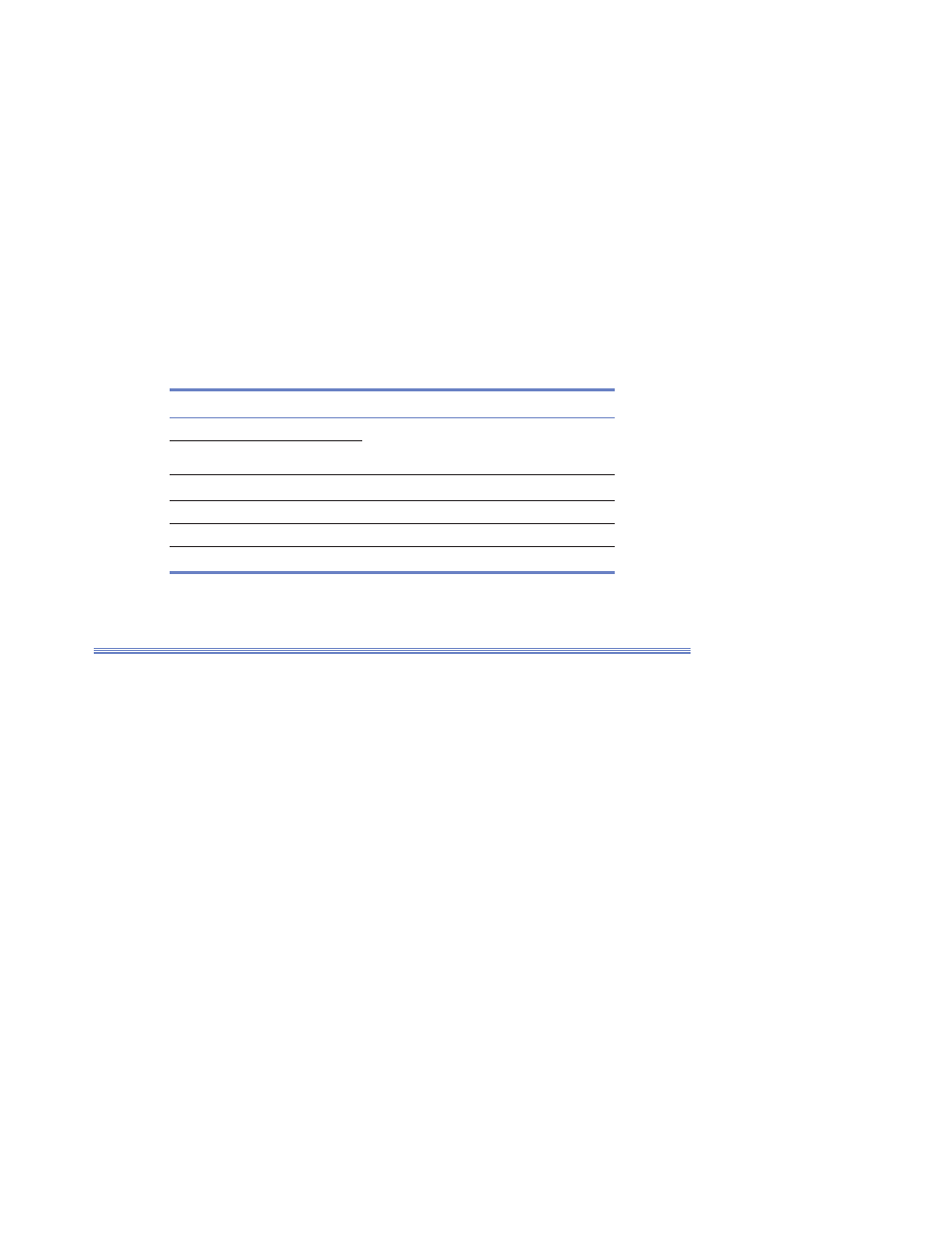
Appendix I I3
2.7 Removable, soft insulation: Install soft-cover, blanket insulation on unin-
sulated steam valve bodies and fi ttings, typically resulting in a 6-month
payback.
Steam trap losses: A typical steam trap loses 0.5–0.9 kg/hr (1–2 lb/hr) of live
steam during normal operation. A failed trap can lose 9–36 kg/hr (20–80 lb/hr)
of live steam. Replacement or repair can result in a payback of 1 month.
Steam leaks: Establish a leak identifi cation and repair program. Leaks for a
well-maintained plant are <1%, typically 2–4%, for a poorly maintained plant
10% or more. Table I2 lists rules of thumb for estimating the annual cost of
steam leaks.
Sizing condensate lines: Condensate return piping should typically be 50%
of the diameter of the steam pipe it serves.
TABLE I2. STEAM LEAK RULES OF THUMB.
Rate Blow
Length (mm/in.)
$/Year
@$11/ton (metric) or
@$5.00/Klb
Type
(kg/hr)/(lb/hr)
Wisp
0.9/2
100/4
90
Small
4.5/10
305/12
450
Medium
13.6/30
914/36
1350
Large
77/170
1829/72
7500
I.3 HVAC & R Systems
HVAC&R unit costs: The incremental cost for HVAC heat is typically
$11 / (metric) ton ($5.00 / klb) $0.87 / MWh ($3.00 / MMBtu) and $176 / kWh
($50 / k ton-hour) for chilled water cooling.
3.1 Chiller Effi ciencies: The typical industrial centrifugal chiller operates
at a COP of approximately 5.0 and 0.70 kW / ton (2.46 kW
el
/ kW
therm
)
(0.85 kW / ton (3 kW
el
/ kW
therm
) with CHW and CT energy). A new high-
effi ciency chiller can operate at 0.55 kW/ton (1.94 kW
el
/ kW
therm
) (0.65
kW / ton (2.3 kW
el
/ kW
therm
) with CHW and CT energy).
3.2 HVAC&R Formulas: The following formulas are useful in calculating
heating and air-conditioning loads:
Sensible heat, W = 37.3 × L /s ×
a.
∆
T (
°
C)
Sensible heat, Btu / hr = 108 × CFM ×
∆
T (
°
F)
Total cooling, W = 1.2 × L /s ×
b.
∆
H (kJ / kg dry air)
Total cooling, Btu / hr = 4.5 × CFM ×
∆
H (Btu / lb dry air)
Water side, W = 4100 × L /s ×
c.
∆
T (
°
C)
Water side, Btu /hr = 500 × GPM ×
∆
T (
°
F)
Latent load, W = 6.4 × L /s ×
d.
∆
M (g)
Latent load, Btu /hr = 0.67 × CFM ×
∆
grains