Retrotec USACE User Manual
Page 216
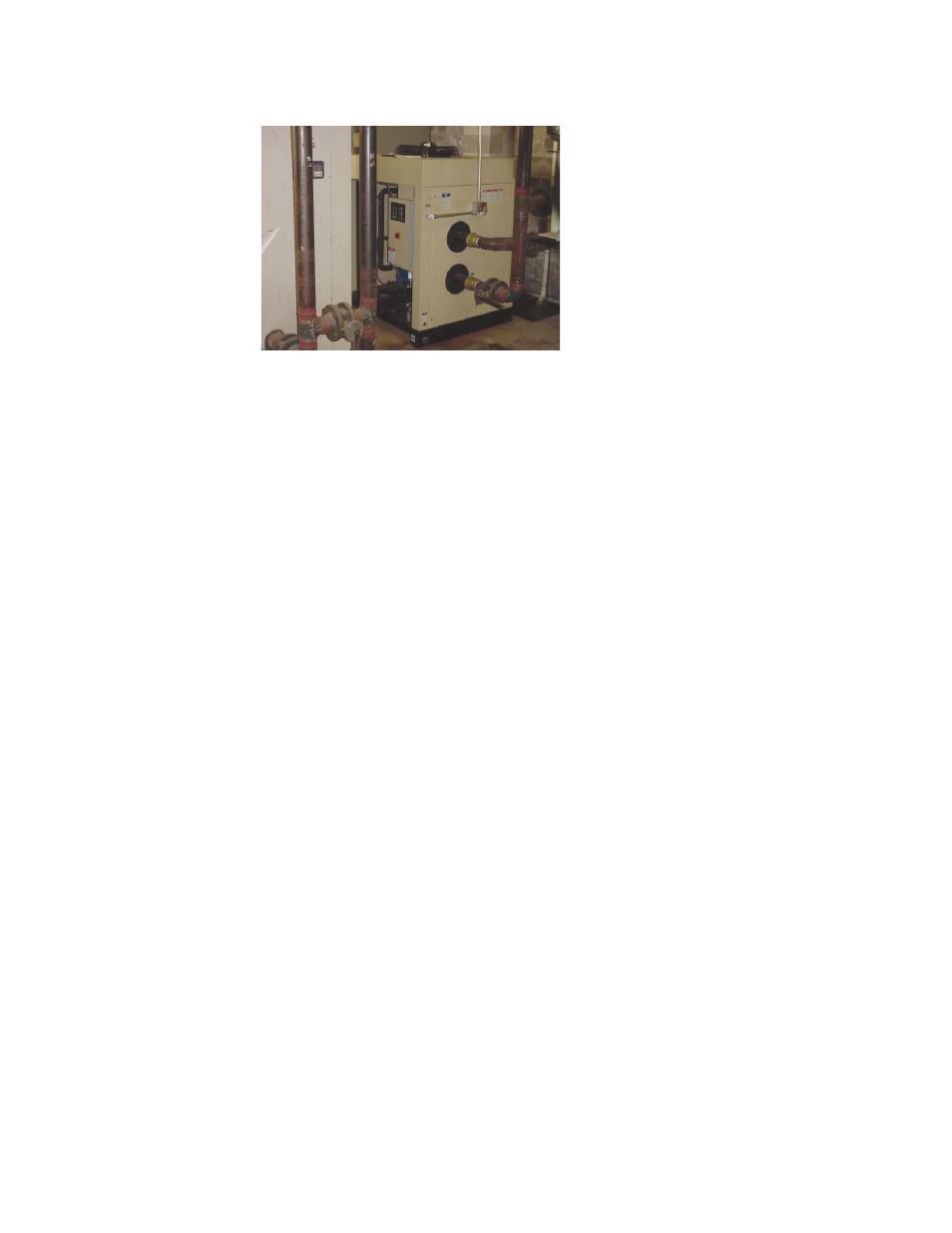
D86 ENERGY & PROCESS ASSESSMENT PROTOCOL
D.4.3.14 Use of Refrigerated Air Dryers (Ineffi ciency)
Figure D140. Refrigerated air dryer.
There are two types of air driers. In one, the compressed air passes through a
cold chamber where the temperature of the air is dropped to a dew point in the
range of 2 –°4 °C (35–39 °F) (Figure D140). Moisture in the compressed air is
condensed in the dryer and drained from the system. The power requirement
of a refrigerated dryer is approximately 0.2 kW/2.8 m
3
(0.2 kW/100 CFM).
The other type of dryer uses a desiccant to remove the water vapor from
the compressed air stream. These dryers use different methods to regenerate
the desiccant, all of which affect their performance and energy use. The sim-
plest one uses a throw-away desiccant and the power they use is caused only
by the pressure drop of the compressed air going through the dryer, which is
approximately 0.2 kW/2.8 m
3
(0.2 kW/100 CFM). Other dryers use different
approaches to regenerate the desiccant they use. One type uses a twin tower
where heated purge compressed air is wasted to regenerate the desiccant. This
dryer can provide very dry air with a dew point of –40 °C (–40 °F), but the
energy use is high, in the range of 2–3 kW/2.8 m
3
(2–3 kW/100 CFM). Heat-
of-compression desiccant dryers do not have a waste of purge air but require
a very hot discharged compressed air stream available only from centrifugal or
lubricant-free rotary screw compressors. The power requirement of this dryer
is approximately 0.8 kW/2.8 m
3
(0.8 kW/100 CFM).
The use of a dryer should be consistent with the degree of dryness required
by the compressed air users. If it is for cleaning and pneumatic tools, the dry-
ness provided by the aftercooler may be suffi cient and no dryer needed. If
precision controls use the compressed air, then very dry air, provided only by a
desiccant cooler, should be considered. If a refrigerated dryer is used, the use
of a desiccant type that provides the same moisture removal should be evalu-
ated as an alternative.
D.4.3.15 Use of Modulation-Controlled Air Compressors at Part
Load (Ineffi ciency)
Modulation-controlled air compressors throttle the incoming air to the com-
pressor by closing the inlet air valve. This limits the amount of air to be com-
pressed, thus the output is varied. This control scheme is applied to centrifugal
and lubricated-injected rotary screw compressors. It is a reasonably effi cient