Appendix j – Retrotec USACE User Manual
Page 17
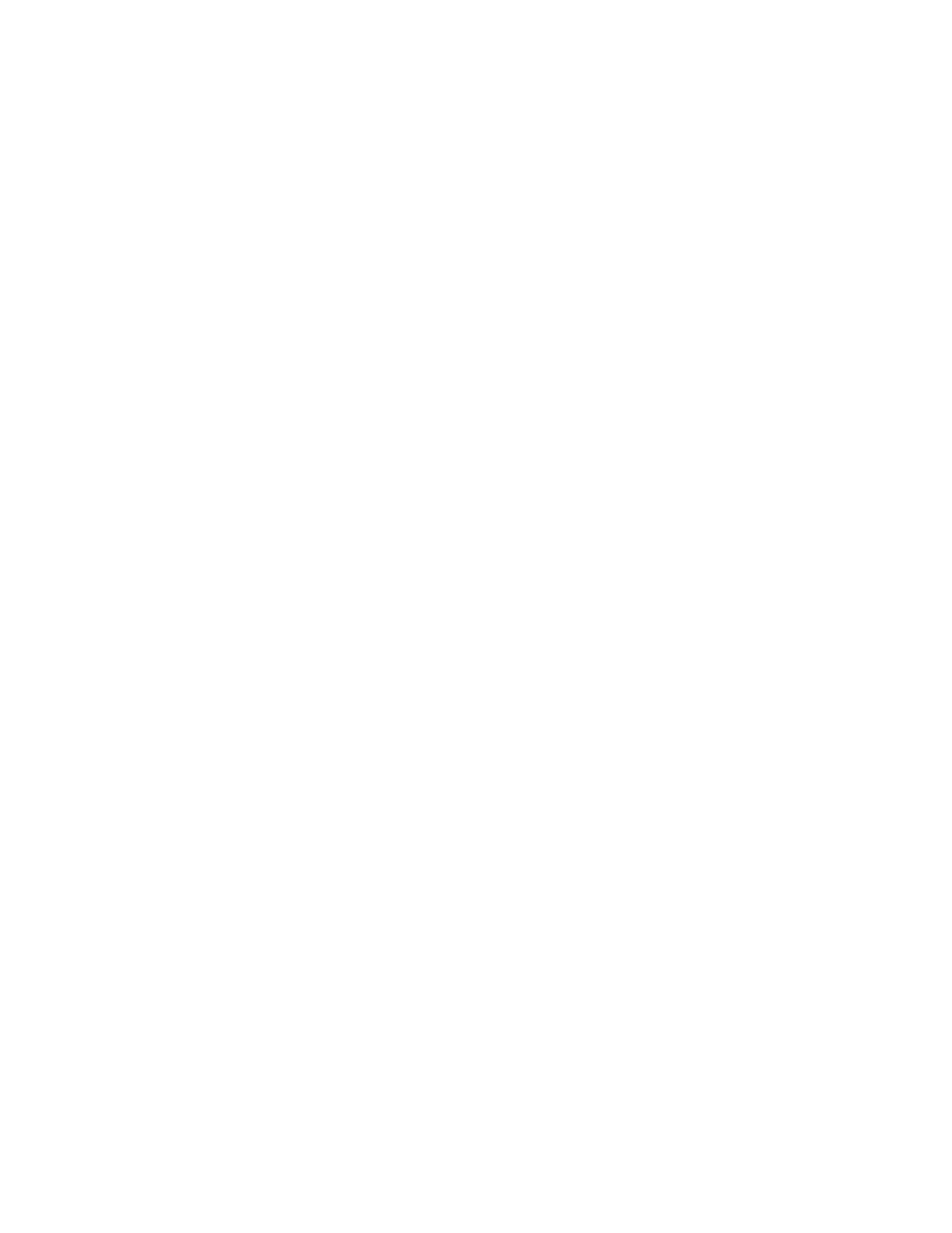
Figures xvii
Figure G16. Heat transfer by convection is observed in this IR thermogram during a pressure
test as cooled air fl ows over a light fi xture, causing a warm pattern or, directly on
the wall surface, a cool pattern. (Images from BCRA.)
Figure G17. IR thermography showing a failed window pane. (Images from BCRA.)
Figure G18. Heat transfer by radiation from incandescent lighting to the ceiling above, the ad-
jacent wall, and the framing below. (Image from Scott Wood Associates, LLC.)
Figure G19. IR thermography of a CMU (concrete mortar unit) showing patterning of the
grout fi lled areas. (Image from BCRA.)
Figure G20. During the day, the moisture trapped in the insulation under the roofi ng cools
slower than the roofi ng, providing a warmer pattern when observed after
sunset. (Image from BCRA.)
Figure G21. During the evening, the moisture trapped in the insulation under the roofi ng
warms slower than the roofi ng, providing a cooler pattern after sunrise. (Image
from BCRA.)
Figure G22. When performing window testing the leaks may appear sharper using IR ther-
mography. (Images from BCRA.)
Figure G23. IR thermography of a vinyl-sided three-story apartment, showing cool pat-
terning of a third-fl oor washing machine leak. (Images from Infrared Training
Center.)
Figure G24. IR thermography showing a leak from HVAC ducting. (Images from Infrared
Training Center.)
Figure G25. Heat fl ux meter installed on a wall and the corresponding IR thermogram.
(Images from original paper presented to BCRA.)
Figure G26. IR thermogram of an electric and hydronic radiant fl oor system. (Images from
BCRA.)
Figure G27. The IR thermogram on the left is a correctly operating steam trap, and the IR
thermogram on the right one that has failed. (Images from Infrared Training
Center.)
Figure G28. The IR thermogram on the left is showing heat gain that may be due to an over-
heated motor bearing. (Images from Infrared Training Center.)
Appendix J
Figure J1.
Trend of supply air temperature vs. supply air temperature setpoint.
Red˛=˛supply air temperature; green = supply air temperature setpoint.
Figure J2.
Example of Load-Based Optimization System (LOBOS) reset strategies in op-
eration.
Figure J3.
Chiller Plant Tuning Graphic: simple, requires only four adjustments. Differ-
ential pressure and chilled water supply temperature are adjusted when loads
are increasing and decreasing.
Figure J4.
AHU Tuning Graphic: simple, requires only six adjustments. Set points for fan
speed, return air temperature, static pressure and supply air temperature are
adjusted when loads are increasing and decreasing.
Figure J5.
AHU Setup Screen.
Figure J6.
High Effi ciency Dehumidifi cation System.
Figure J7.
High Effi ciency Dehumidifi cation System: Energy Savings Vs. Design Air
Flow @ 100% reheat to 65F/68F – Typical for DOAS used for barracks, labs,
manufacturing facilities, etc.
Figure J8.
High Effi ciency Dehumidifi cation System: Energy Savings Vs. Design Air Flow
@ 25% reheat to 65F/68F – Typical for facilities that need minimal reheat.