Retrotec USACE User Manual
Page 374
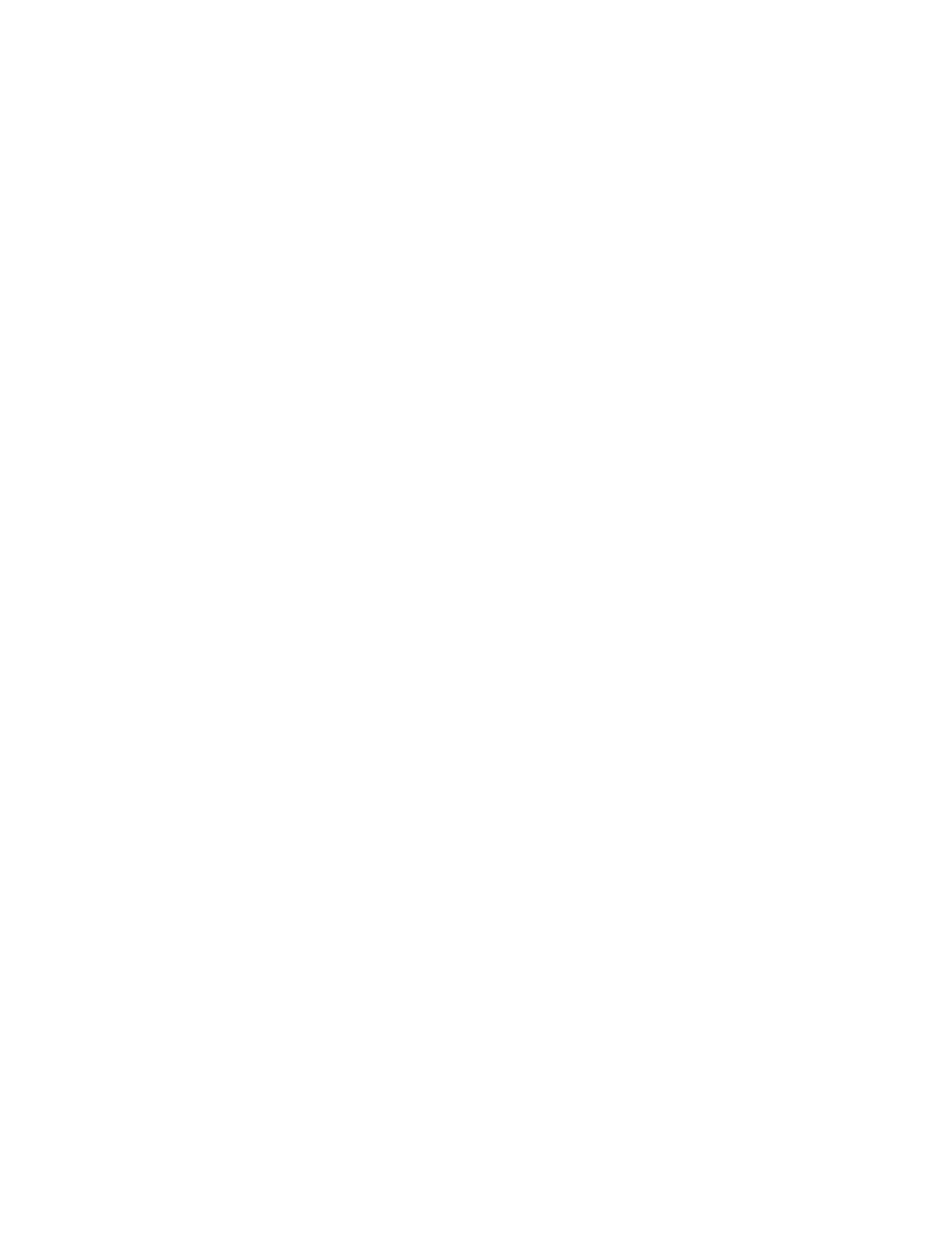
I6 ENERGY & PROCESS ASSESSMENT PROTOCOL
4.19 Lube oil cooler: Properly maintain lubricating oil cooler performance
for effi ciency and reliability.
4.20 Synthetic lube oil: Use synthetic oil on reciprocating and screw
machines that are low oil consumers. Saves 1% energy.
4.21 Motor drives: Specify energy effi ciency motors to save 4–6% of motor
load with 2-year payback.
4.22 Alternate drives: Evaluate back pressure steam turbine drives ($0.015/
kWh) or reciprocating or combustion turbine drives in a cogeneration
topping cycle.
4.23 COG belt drive: Replace standard V-belt with high-effi ciency COG
type V-belt saving 1.5% of drive energy for 3-month payback without
shaft change.
4.24 Air intake location: Air intake should be from coolest location, typi-
cally outside. A 5
°
F temperature difference reduces motor load by
1%. Compressor room air is often 10–40% hotter than outside air,
depending on whether it is summer or winter.
4.25 Inlet guide vanes (IGV): Replace butterfl y inlet valve with inlet guide
vane (IGV) design to reduce compressor motor load by 2–4% with
9–18 months payback.
4.26 Energy
effi ciency dryers: Specify a high-effi ciency dryer such as “Heat
of Compression” and operate unit properly. “Heatless” dryers are not
recommended, as they use and dump CA to regenerate desiccant.
4.27 Dew point control: Optimize dew point by controlling to meet require-
ments on an “as needed” basis rather than timer controls.
4.28 Recover heat of compression: The heat of compression is typically
rejected to the cooling tower. However, 95% of this heat (approxi-
mately 230,000 Btu/hr (673.44 kWh) per 100 hp (379 W ) of com-
pressor drive can be recovered with a plate heat exchanger to preheat
boiler makeup water. Air-cooled units can be directly used as building
heat during winter and exhausted during summer.
4.29 PM program: Establish a predictive and preventive maintenance pro-
gram. A complete program typically saves two to three times its cost.
4.30 Reduce compressor pressure: A 1% motor load savings for each 2 psig
(13.8 kPa) reduction in setpoint can result down to a point that is lim-
ited by the highest-pressure user. This is a no-cost ECO.
4.31 Point-of-use pressure control: Allow the setpoint to automatically fl oat
based on a control signal from the highest-pressure user. This can
generally average an additional 2–4 psig (14–28 kPa) pressure reduc-
tion at the compressor.
4.32 Lower high-pressure user: Reduce the pressure requirements of the
high-pressure user. These could be sticking air cylinders or unneces-
sary equipment or operator demands. An example is high-pressure
paint sprayers versus HVLP units.