F.12.3.5. conclusions – Retrotec USACE User Manual
Page 324
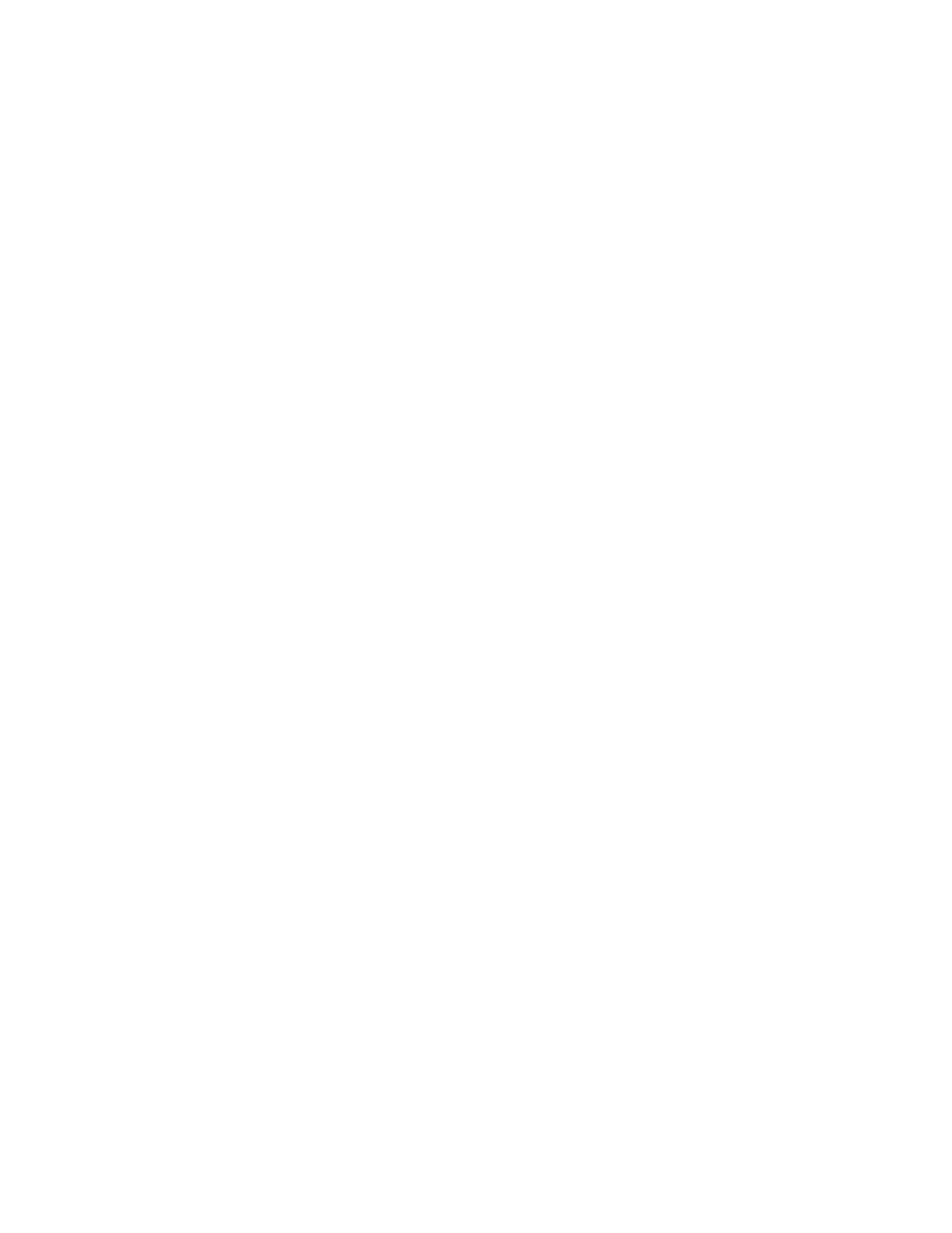
F30 ENERGY & PROCESS ASSESSMENT PROTOCOL
Because bias pressures will have a greater impact on single-direction tests,
the maximum allowable bias pressure under these circumstances has been re-
duced to 5 Pa or 10 percent of the lowest test pressure, which would be 50 Pa
in this case. On the other hand, the test pressure achieved must be 75 Pa. At
these pressures, the bias pressure is somewhat masked by the higher test pres-
sure and extrapolation is no longer an issue. Because buildings often leak more
in one direction versus the other, testing in only one direction must be consid-
ered less accurate than testing in both directions.
The bias pressure in a 12m (40ft) high building where the temperature was
–18
o
C (0 °F) outside and 20
o
C (68 °F) inside and negligible wind for example,
would be 10.5 Pa. This bias would typically be broken up into say +5 at the top
and –5.5 at the bottom of the building. If bias pressure was a problem during
the test the indoor temperature could be brought closer to the outdoor tem-
perature by running door fan for about 5 minutes, which would be suffi cient
time to replace most of the indoor air with outdoor air, and thereby reduce the
bias pressure somewhat.
F.12.3.4. Summary of Deviations from the ASTM Standard
All pressure tests shall comply with the requirements of ASTM E 779-03 with
exceptions indicated in Table 5.
F.12.3.5. Conclusions
Air leakage is caused by pressures that are in the 4 to 10 Pa range. In order
to calculate actual air leakage rates, results should be referenced to those low
pressures but to do so encourages unrepeatable results. To test the quality of
construction, it is not so important to get accurate estimates of loss rates as it is
to simply test the quality of construction and that is best done at higher refer-
ence pressures where results are least affected by ambient pressures and most
repeatable. When air leakages of different buildings are measured at higher
pressures, the actual losses associated with air leakage will generally be pro-
portional to the measurements. It is wise then to express results as a reference
pressure of 75 Pa and to adopt testing methods that will ensure repeatable
results. By testing in both directions from 50 to 25 Pa, the most accurate result
can be obtained with a minimum of test equipment and disruption. Because
of the robustness of the procedure, tests can be performed under almost any
weather condition without affecting results. Only those test parameters that
affect results in a meaningful way are included in a recommended procedure.
It is further suggested to express results in units of airfl ow per unit enclosure
area at 75 Pa so that easy comparisons can be made. Units of cfm per square
foot and liters per second per square meter (both at 75 Pa) have already been
established as the leading candidates for units.
Set-up conditions are crucial for repeatable results, which partially explain
the condition requiring that intermittent exhaust be left open and continuous
ventilation openings be sealed. The other reason is that this set-up condition
best describes what the envelope will experience over its lifetime. Testing in