I.2 steam systems – Retrotec USACE User Manual
Page 370
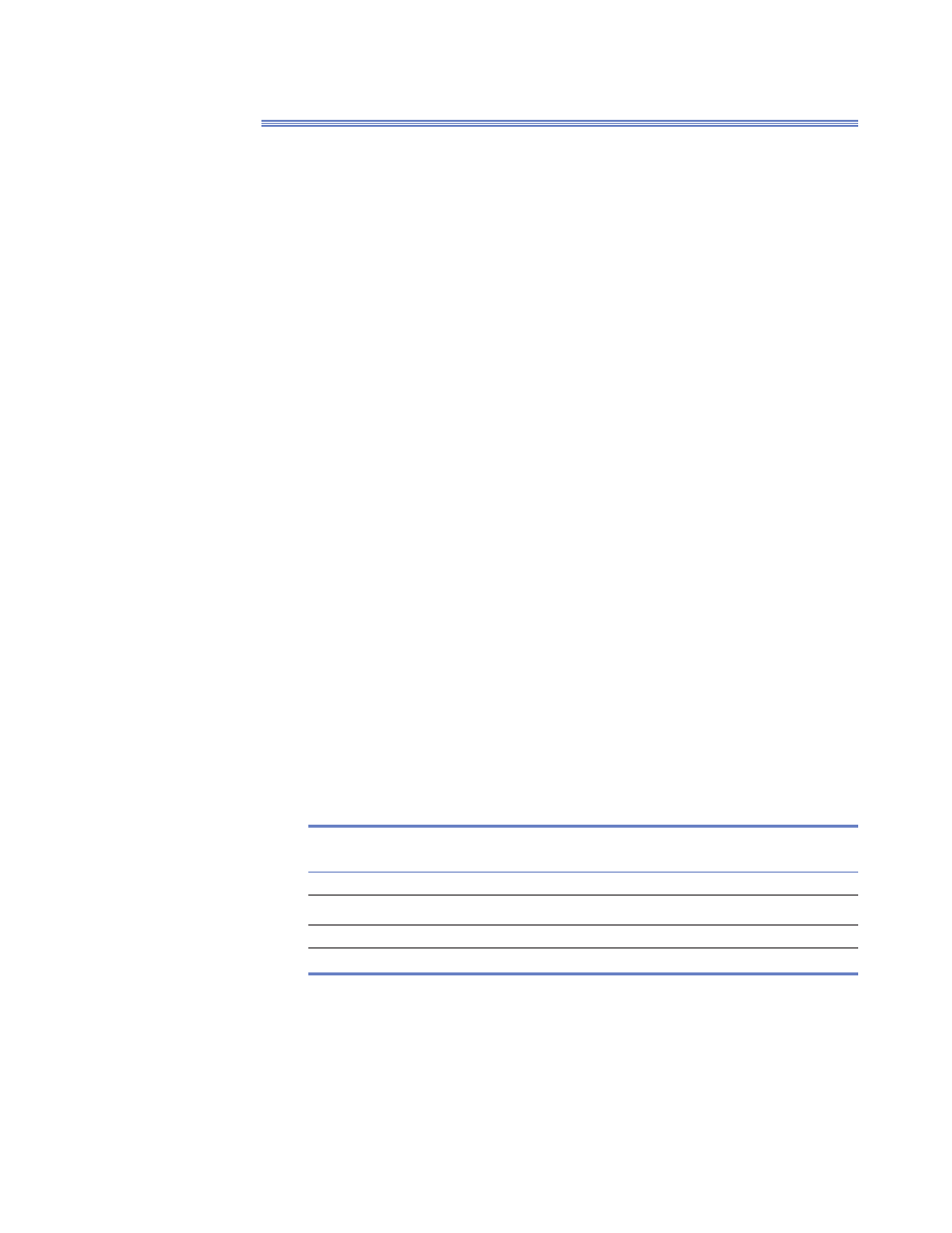
I2 ENERGY & PROCESS ASSESSMENT PROTOCOL
I.2 Steam Systems
2.1 Boiler effi ciency: Optimize fl ue gas conditions to reduce the percent of
0
2
, fl ue gas temperature °C (°F), and CO concentration. Table I1 lists
how the incremental changes in fl ue gas conditions improve a nominal
1,000 kPa (~150 psi) boiler effi ciency.
2.2 Maximize use of high-effi ciency boiler: Maximize the operating hours
and loading of the highest effi ciency boilers to typically reduce fuel con-
sumption by 1–3% at zero cost.
2.3 Run minimum safe number of boilers: Operate minimum number of
required boilers to safely and reliably meet the facility’s steam needs,
resulting in typical savings of 3–6% of the annual fuel expense at no
cost.
2.4 Reduce boiler steam pressure: A 69 kPa (~10 psig) reduction in boiler
pressure setpoint will reduce boiler fuel as shown (in a case in which no
steam turbines are used):
1000–1400 kPa (~150–200 psig) saves 0.2%
690–1030 kPa (~100–150 psig) saves 0.4%
340–690 kPa (~50–100 psig) saves 1.0%
2.5 Heat loss versus insulation thickness: 25 mm (1 in.) of insulation reduces
bare pipe heat loss by approximately 70%; 50 mm (2 in.) reduces the
remaining 30% loss by 70% to 21%, for 91% total; 75 mm (3 in.) reduces
the last 9% by 70% to 6.3%, for a total of 97.3%; 50 mm (2 in.) is the
“economic” thickness for 80% of the applications. Well-insulated distri-
bution systems for a 14.5 MW (50 MBtus/hr) steam distribution system
will typically have 2–4% heat loss. Losses for this system with average
insulation performance will lose 6–10%, while poorly insulated systems
can lose 15% or more. These losses through various quality of insulation
are fi xed losses independent of steam fl ow rate.
TABLE I1. HOW INCREMENTAL CHANGES IN FLUE GAS CONDITIONS
IMPROVE A NOMINAL 150 PSI BOILER EFFICIENCY.
Flue Gas
Effi ciency Condition Change
Change
0
2
(percent)
–1.0%
+0.66%
Temp (°C/°F)
–5.5 °C/–10 °F
+0.25%
CO (ppm)
–100 ppm
+0.10%
2.6 Pipe insulation: Insulate steam systems when pipe surface temperatures
are
≥
71 °C (160 °F) cold-climate or
≥
88 °C (190 °F) warm-climate.
Fuel costs, building inside/outside, and safety must also be considered.
Paybacks usually occur in 18–48 months.