Retrotec USACE User Manual
Page 12
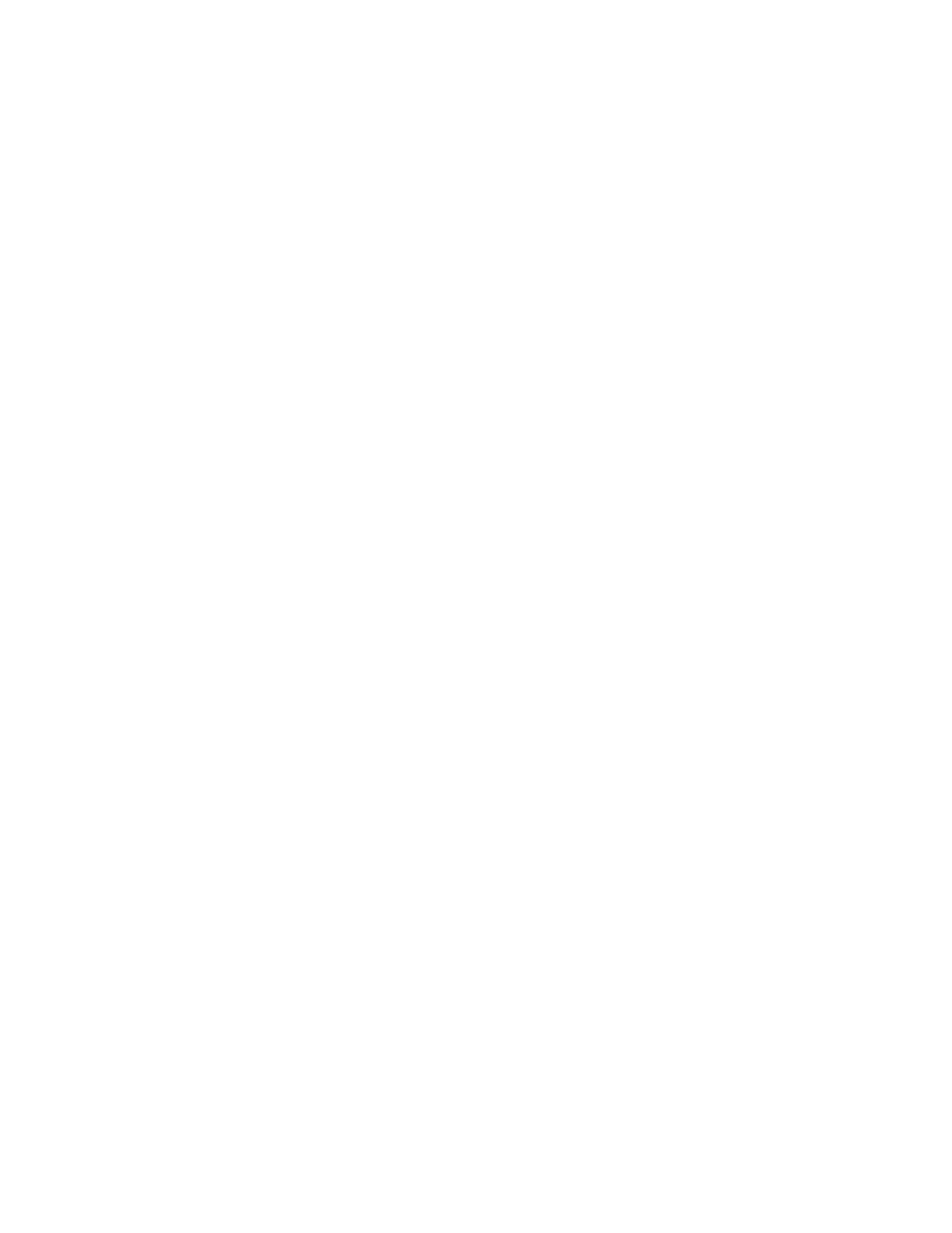
xii ENERGY & PROCESS ASSESSMENT PROTOCOL
Figure D133. Air/oil separator.
Figure D134. Well-maintained control system.
Figure D135. Compressed air for fi lter cleaning by reversed fl ow pulsing requires higher
pressure than most other uses.
Figure D136. Welding work station with compressed air hose on left that is used for part
cleaning.
Figure D137. Use of compressed air to agitate liquid in tank.
Figure D138. Large air compressor that often runs at part load.
Figure D139. Rotary screw compressor using building air.
Figure D140. Refrigerated air dryer.
Figure D141. Large central compressed air equipment requiring load control system.
Figure D142. Offi ce worker reading (left); surgery room (above).
Figure D143. Daylit library space with electric lighting on.
Figure D144. Empty offi ce cubicle area with the lights on full.
Figure D145. Buildings are lit with only a few people working.
Figure D146. Examples of unswitched outdoor lighting: multifamily residential building.
Figure D147. Scene with controlled light not aimed at the sky (left); outdoor lighting aiming at
the sky, washing out the starlight and wasting energy (right).
Figure D148. Incandescent wall sconce (left) and fl uorescent wall sconce (right).
Figure D149. Higher-effi ciency (premium) ballasts.
Figure D150. T12 with 1½-in diameter and T8 with 1-in diameter (left); T12 magnetic bal-
last (right).
Figure D151. Compact incandescent lamps used for general lighting.
Figure D152. Spectrally enhanced lighting uses less energy than commonly used fl uorescent
lamps.
Figure D153. Reduced ambient lighting. One lamp is removed from each fi xture.
Figure D154. Reduced ambient lighting supplemented by task lighting.
Figure D155. Mercury vapor lamps should be replaced with more effi cient light sources.
Figure D156. Non-LED exit sign (left); LED exit sign (right).
Figure D157. High-pressure sodium lighting (left); high output T8 (right).
Figure D158. Heating water distribution pump runs continuously in winter even though no
hot water is needed.
Figure D159. Standard effi cient motor powering a fan.
Figure D160. Properly sized motor for exhaust fan.
Figure D161. Motor identifi cation label (“name tag”) shows effi ciency rating.
Figure D162. Constant-speed motor.
Figure D163. Timer used to turn off process equipment.
Figure D164. Well-maintained condensate receiver with pump to send condensate back to
heating plant.
Figure D165. Constant-speed condenser water pump.
Figure D166. Example of difference in loads on the three-phase electrical power ranging from
a low of 251A on C-phase to a high of 444A on B-phase.
Figure D167. Paint booth with exhaust system continuing to operate when fi nished painting.
Figure D168. Location adjacent to paint booth used to place items from outside to allow
them to reach room temperature before painting.
Figure D169. Paint drying oven with recirculation of oven air. Note the small exhaust duct to
outside.
Figure D170. High-pressure compressed-air paint gun.