Retrotec USACE User Manual
Page 11
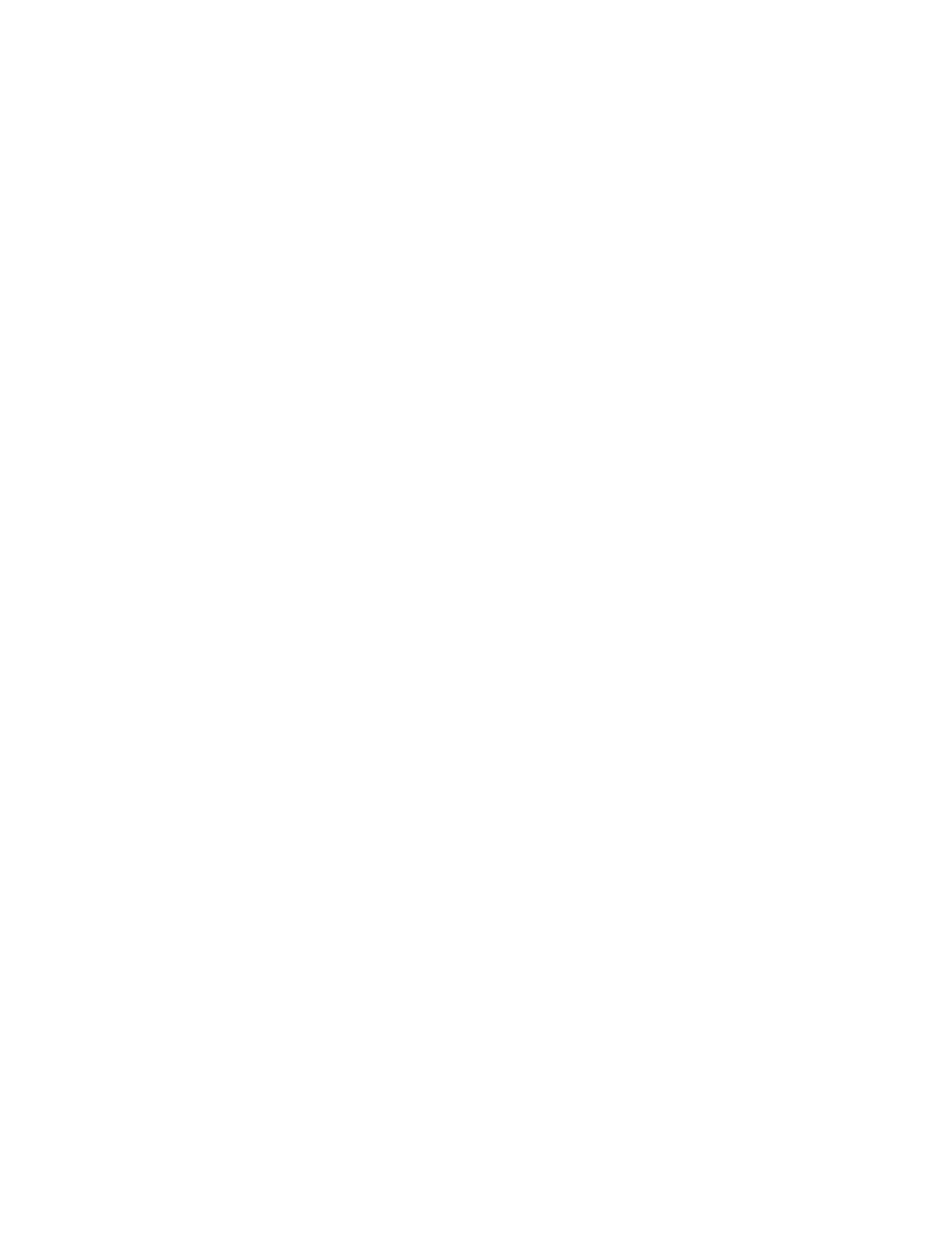
Figures xi
Figure D97. Check old burners for continuous lit pilots versus electronic ignition of pilot.
Figure D98. Boiler similar to this found cycling in dining facility heating hot water in
summer.
Figure D99. Deaerator tank (left) and condensate receiver(right)—both could have vent
gases above 200 °F.
Figure D100. Pump in foreground is electrically driven. The pump behind it is a turbine-
driven pump.
Figure D101. Cooling tower to condense steam from waste heat boiler.
Figure D102. Steam pressure-reducing valve drops pressure from main distribution pressure
(above) to lower value suitable for building equipment (left).
Figure D103. Low-effi ciency old boiler still in use that has been converted from coal to
burning natural gas.
Figure D104. Old burner with low effi ciency.
Figure D105. Oil-fi red boiler with compressed air atomization.
Figure D106. Modern high-effi ciency burner.
Figure D107. Elevated fuel oil tank.
Figure D108. Aboveground horizontal fuel oil tank adjacent to heating plant.
Figure D109. Stack damper in breeching branch before main breeching run to stack.
Figure D110. Small boiler serving individual building.
Figure D111. Valve to isolate offl ine chiller.
Figure D112. Dirty tubes of a heat exchanger.
Figure D113. Control panel of chiller—uses sensors in chiller and in connecting piping that
often need calibration.
Figure D114. Balancing valves of chilled water system.
Figure D115. Thermometers in chilled water lines—check if possible to vary temperature.
Figure D116. Cooling towers for chilled water plant showing fans and pumps.
Figure D117. Window air conditioners and air-cooled chillers providing cooling to a
building.
Figure D118. Large chiller that has a diffi cult time servicing building loads during mild
weather conditions.
Figure D119. Large chillers sized for peak cooling loads.
Figure D120. Smaller two-compressor chiller provides high effi ciency at part loads.
Figure D121. Central cooling plant primary chilled water pump.
Figure D122. Chiller plant controls.
Figure D123. Example of the performance of dirty cooling tower distribution nozzles.
Figure D124. Cooling tower showing return water pipe exiting basin.
Figure D125. Multiple cooling towers having cold well or basin in ground that serve a chilled
water system. The fi rst two towers on the left share a common basin. Note the
vertical turbine pumps adjacent to each tower.
Figure D126. Cooling tower fans with no discharge duct.
Figure D127. Typical compressed air system showing dryer location.
Figure D128. Typical compressed air system showing location of components and possible
leak locations.
Figure D129. Compressed air hose connection with fi lter and regulator where leaks are
common.
Figure D130. Typical compressed air system showing after-cooler location.
Figure D131. Filter and regulator in compressed air system.
Figure D132. Air-cooled compressors with cooling coil on mezzanine and duct outlet for
winter time heating.