Retrotec USACE User Manual
Page 417
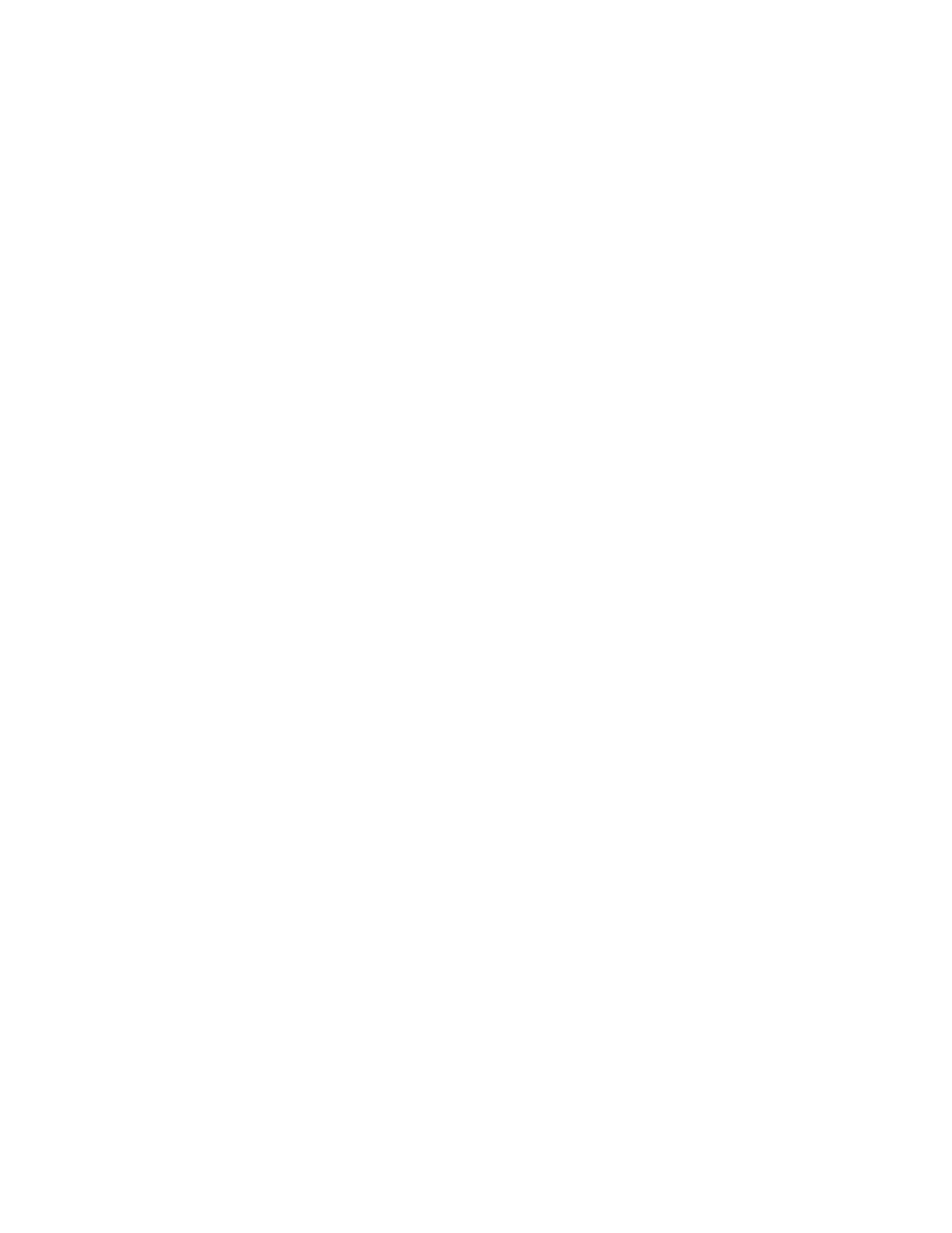
Appendix L L17
7.4 Welding
7.4.1 Select welding process that produces the least volume of fumes consistent with other
application considerations. GTAW, plasma arc welding (PAW), and SAW processes gen-
erally produce the lowest fume levels. GMAW is normally the process with the next-
lowest fume generation rate.
7.4.2 Use high-effi ciency welding power sources, which have better electrical effi ciency and
an improved power factor. In high-effi ciency welding, power to the transformer is shut
off during system idling, and cooling fans only run when needed. These power sources
provide 10–40% energy savings over older units.
7.4.3 Use modern inverter welding power sources, which can reduce the fume generation
for pulsed gas metal arc welding (GMAW-P) compared to conventional GMAW proce-
dures.
7.4.4 Selecting optimum welding voltage to reduce fume generation.
7.4.5 Select welding electrodes with reduced fume generation. Electrodes and electrode
coatings containing higher percentages of more volatile ingredients produce higher lev-
els of fume.
7.4.6 Select shielding gas with reduced fume generation for the GMAW and fl ux cored arc
welding (FCAW) processes. Argon-based shielding gases with the lowest percentages
of oxygen or carbon dioxide will minimize fume for both GMAW and FCAW. The fume
generation rate can be cut almost in half by changing from 100% CO
2
shielding gas to
a mixture of argon with 25% CO
2
shielding gas. A further reduction in fume generation
rate can be achieved by use of a shielding gas containing argon with only 5% CO
2
along
with the appropriate electrode.
7.4.7 Avoid, remove, or reduce oil fi lm, paint, primer, rust, galvanizing, or other coatings on
the welded surfaces since these coatings increase fume.
7.4.8 Reduce expulsion during spot welding.
7.4.9 Avoid short-time conditions with spot welding, changing over to medium-time condi-
tions.
7.4.10 Place containers with welded small parts in the totally enclosed cabinets connected to
exhaust system to avoid residual welding smoke release into the building.
7.4.11 Exhaust from the total welding process enclosure when automatic welding machines
are used.
7.4.12 Exhaust from the welding area enclosure separating welding process from operator’s
environment, when robotic welding and material handling are used.
7.4.13 Install local exhaust, which captures the contaminants at or near their source, with
manual and semiautomatic welding operations.