Retrotec USACE User Manual
Page 13
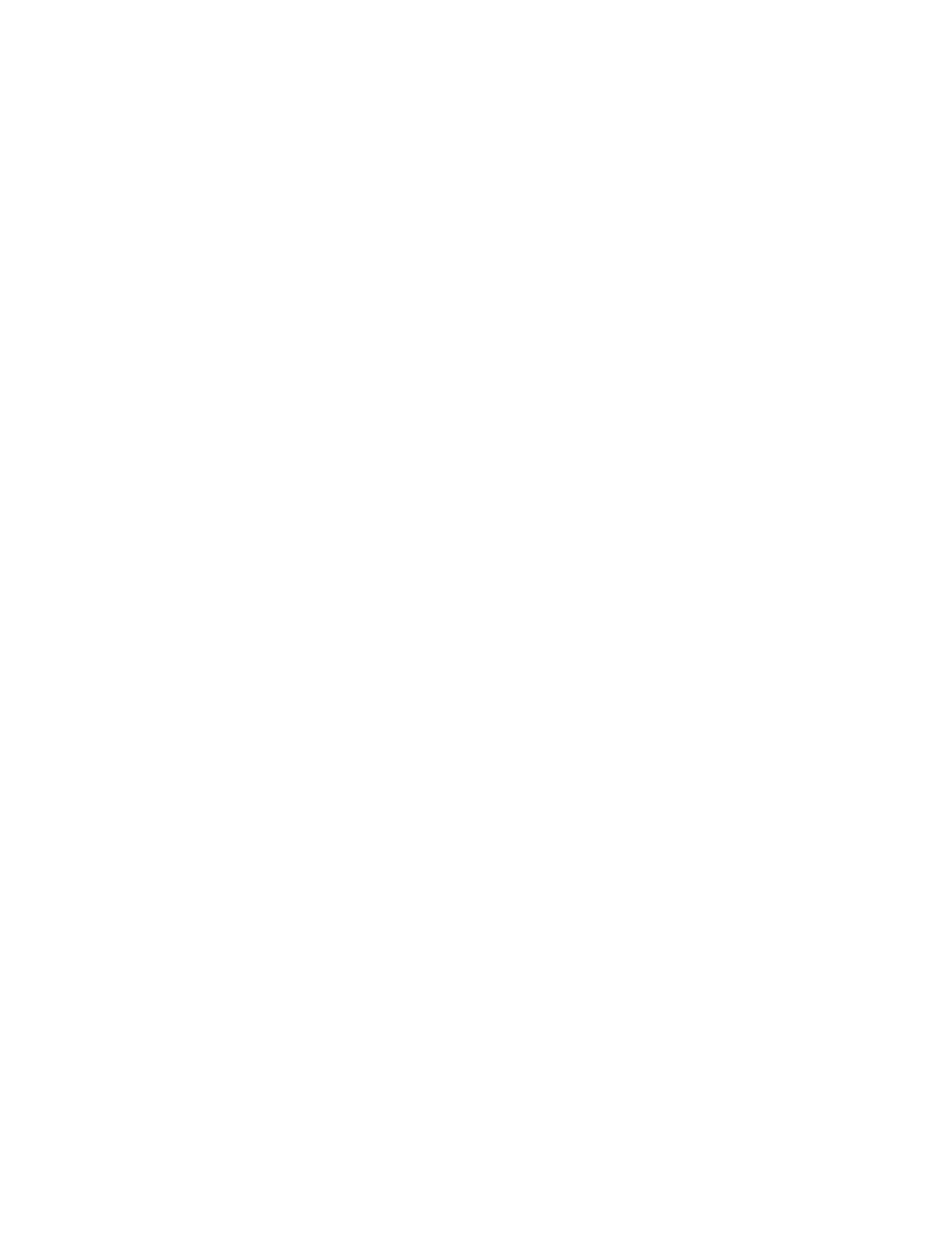
Figures xiii
Figure D171. Paint operations occurring in a partially enclosed paint booth requiring exces-
sive exhaust to contain paint fumes.
Figure D172. Plating shop with open door causing excessive air movement near plating tank
exhaust hoods.
Figure D173. Plating shop with numerous exhaust systems, some that operate continuously.
Figure D174. Heated rinse tank that should be insulated.
Figure D175. Plating tank exhausts: 1.2-meter (4-foot)-wide tank with push–pull exhaust
system (left), hood on both sides of the tank (center), large hood behind the
plating tank (right).
Figure D176. Exhaust systems from a plating shop exhaust some heated air.
Figure D177. Heated chrome acid tank with balls fl oating on surface to reduce loss of water
vapor.
Figure D178. Examples of Unenclosed Machining Processes.
Figure D179. Compressed-air hose connection with fi lter and regulator where leaks are
common.
Figure D180. Machine shop having fl uorescent lamps over total work area. There may be a
potential for the use of task lights.
Figure D181. Welding shop that has constant volume centralized welding exhaust system
that operates continuously (left); recirculating local exhaust system (right).
Figure D182. Stationary hood in a welding booth that works well for small parts—but for
larger parts it would be ineffective.
Figure D183. Weld exhaust system with moveable hood that can be placed at multiple loca-
tions to capture welding fumes.
Figure D184. Enclosure over a container with welded small parts at Fiat plant in Turin, Italy.
Exhaust from the enclosure controls residual weld fumes.
Figure D185. Work station in assembly area having fl uorescent lamp task light over work
area and smaller lamps on extension cord.
Figure D186. Air-cleaning equipment and exhaust fans required by a foundry.
Figure D187. Foundry exhaust air system in mold department.
Figure D188. Melt furnace in foundry that could have hot surfaces.
Figure D189. Hand-pouring of a few molds to obtain a small number of parts.
Figure D190. Looking at burner from inside a heating chamber.
Figure D191. Direct-drive induced draft fan to provide air for burner.
Figure D192. Damper in breeching to stop air fl ow when not operating.
Figure D193. Controls on oven in paint shop.
Figure D194. Heat treat ovens with controls (to right of open doors).
Figure D195. Combustion gas monitors located in breeching to analyze products of combus-
tion.
Figure D196. Oven in paint shop with no combustion controls.
Figure D197. Heat treat oven showing inner refractory bricks.
Figure D198. Loading part into a vertical heat treat furnace.
Figure D199. Small heat treat oven sized for small loads.
Figure D200. Note opening between furnace and door, where red hot inner surface of fur-
nace can be seen.
Figure D201. Heat treat furnaces in standby mode.
Figure D202. Economizer installed in stack to preheat boiler water. Note thermometer
before economizer in stack for temperature measurement.
Figure D203. Combustion gas monitors for sensing the oxygen and carbon dioxide content
of fl ue gases.