Retrotec USACE User Manual
Page 232
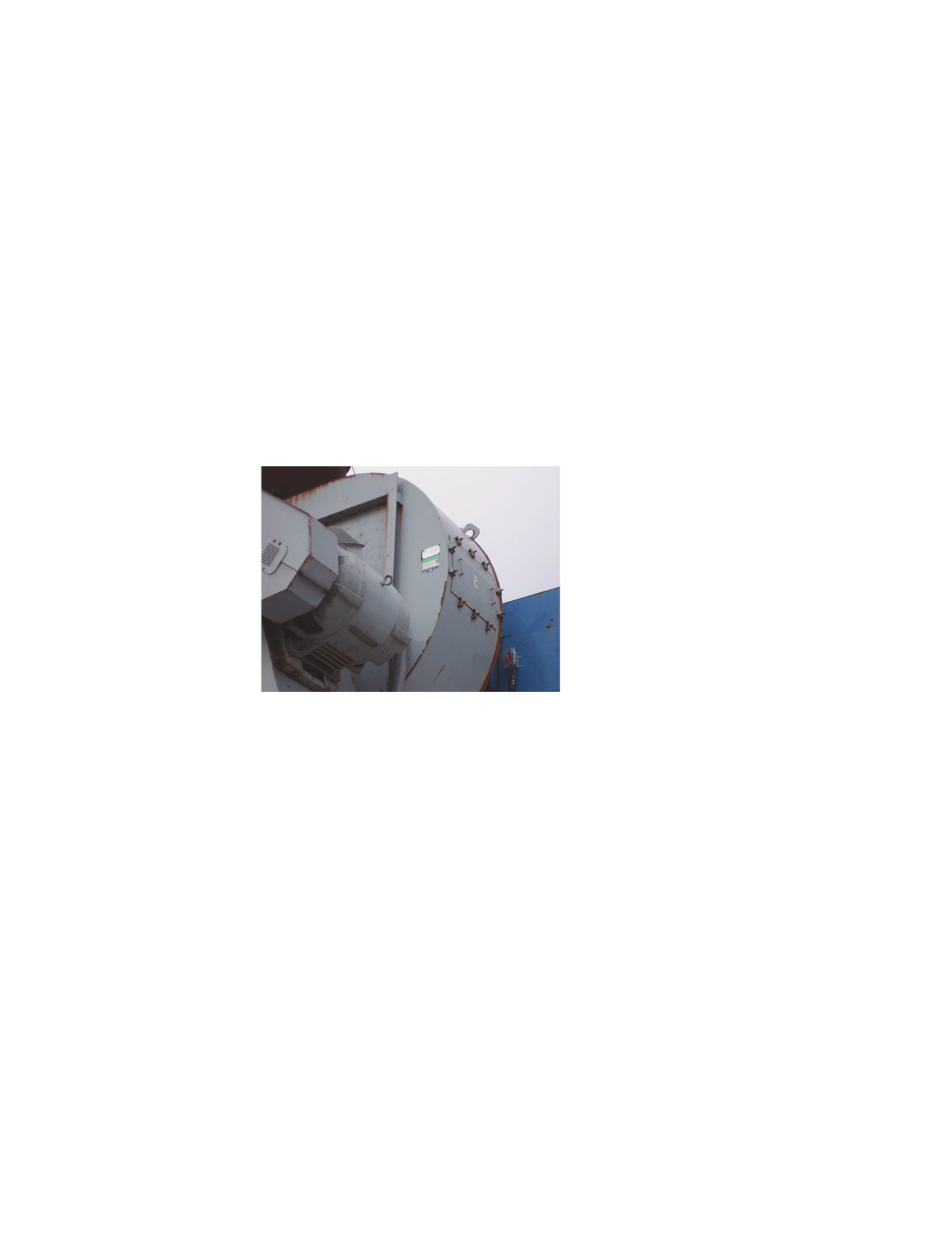
D102 ENERGY & PROCESS ASSESSMENT PROTOCOL
This will save approximately 0.2 kW for each hour of operation the motor runs
fully loaded. The motor effi ciency is provided on the nametag of each motor
and can be used to identify motors that are candidates for replacement.
D.6.1.3 Rewinding Motors More Than Twice (Ineffi ciency)
The life of an electric motor can be lengthened by replacing the wire wind-
ings in the motor as the wire deteriorates. As the motor uses electric cur-
rent, the wire windings in the motor deteriorate slowly due to the resistance
of the wire to electric current. Slowly, the motor looses effi ciency and the
ability to do work. The life of the motor can be extended by replacing the
windings. However, the replacement of windings should only be accom-
plished once in the lifetime of the motor due to the inherent ineffi ciencies
of replacement.
D.6.1.4 Use of Motor Two Sizes Greater Than Required
(Ineffi ciency)
Figure D160. Properly sized motor for exhaust
fan.
Electric motors have power losses through the torque range they operate.
As motors perform their work, they can be heavily loaded at startup and
then less loaded as they continue to run—as with, for example, a ventilation
fan. A fan starting with cold air requires more torque than when operating
with the warmer air it will have when the system gets up to temperature. A
process may have a sequence such that the loads vary through a machining
cycle, and thus the loading on its motor will also vary. Unfortunately, the
effi ciency of a motor is less for motors that are not fully loaded, and having
a motor that is lightly loaded all the time wastes electrical energy. It is
normally wise to design a system with a motor slightly larger (the next size
larger) than required to provide extra power that may be needed to over-
come unplanned system requirements (Figure D160). But if the motor size
is two sizes larger or more, the energy waste is usually enough to warrant
replacement with a smaller motor.