Retrotec USACE User Manual
Page 375
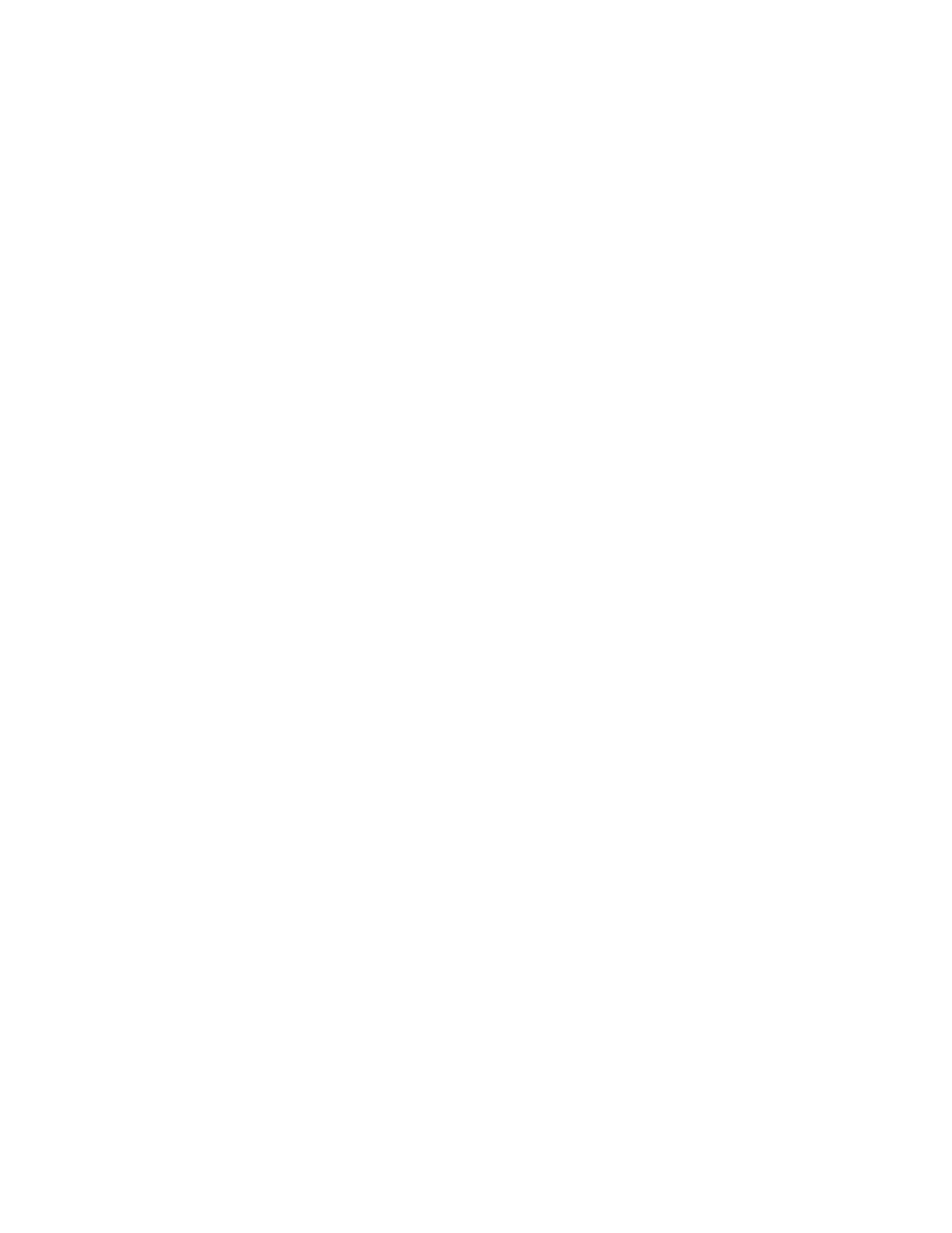
Appendix I I7
4.33 Reduce system
∆
P: Identify and relieve piping system
∆
P bottle-
necks.
4.34 Air traps: Establish a formal trap program. A failed trap can lose
10–100 SCFM (17–170 m
3
/hr), costing $950 to $9500/yr @$0.18/KCF
($.00636/m
3
). Approximately $100/CFM-yr ($3534/m
3
-yr).
4.35 Fix leaks: Industrial facilities leaks range from 10–40% of air produc-
tion. A facility with 1,000 SCFM (1700 m
3
/hr) of production at 25%
leaks is losing approximately $24,000/yr. Typical leaks range from
small 3 CFM (5.1 m
3
/hr) @ $300/yr and medium 20 CFM (34 m
3
/
hr) @ $1,000/yr to large 30 CFM (51 m
3
/hr) @ $3,000/yr. Purchase an
ultrasonic leak detector ($1,000 to $3,500) to support the program.
4.36 ID peakers: Identify and reduce CA loads that strongly contribute to
peak demand. These users actually cost up to twice the average cost
per CFM ($0.36 ($.0127/m
3
) versus $0.18/KCF ($.00636/m
3
)).
4.37 Optimize processes to use less or zero CA: Re-engineer CA out of the
processes by technology or procedural changes. Savings of 15–40%
have been achieved.
4.38 Storage tanks: Install surge/storage tank at high volume, short period,
pulsing users.
4.39 PRV for emergency supply: Install a normally closed high-to-low pres-
sure system PRV for backup of low-pressure header.
4.40 Decommission idle distribution legs and machines: Install airtight
blank fl anges to isolate and depressurize idle legs. Valve off idle
machines. If leaks are 25% and 20% of the systems are idle, then sys-
tem-wide energy costs are reduced by 5%.
4.41 Management and CAT feedback: Formally provide facility manage-
ment with the fi nancial contribution of the CA program on a quarterly
basis. Provide CAT members and “customers” economics on specifi c
projects/programs as achieved.