Retrotec USACE User Manual
Page 244
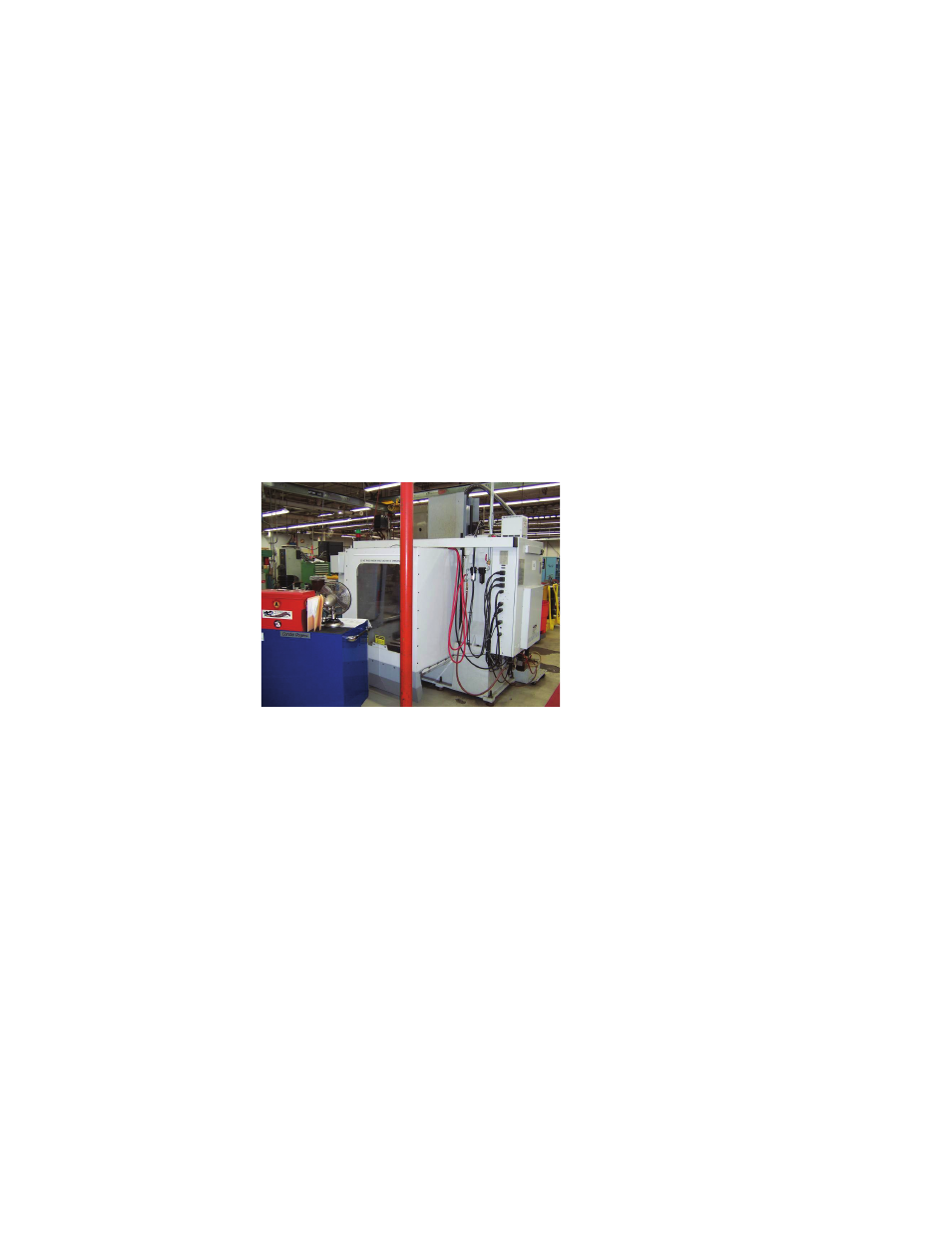
D114 ENERGY & PROCESS ASSESSMENT PROTOCOL
Turning (lathe), drilling, milling, and grinding dry and wet operations emitting
abrasive particles or cooling fl uid mist (Figure D178) need to be equipped with
a local exhaust system to meet OSHA requirements for air quality in the occu-
pied zone. General dilution ventilation is typically not effective or economical.
Most modern machines used for these processes are computer-controlled and
have process enclosures connected to central exhaust systems or have built-in
fans and fi lters to prevent surrounding space contamination. Older machines
need either partial enclosures or local capture hoods, attached to the duct
system with a fi lter and a fan. Well-engineered local exhaust systems not only
provide a healthy and safe working environment but also reduce energy con-
sumption required to operate the system to meet OSHA regulations. For more
information on process enclosures with machining operations, open hoods,
and fi ltration systems, see ACGIH, Industrial Ventilation: A Manual of Recom-
mended Practice, 25th ed., 2004, and HPAF, Ventilation Guide for Automotive
Industry, 2000.
D.7.3.2 Compressed Air Leaks (Waste)
Figure D179. Compressed-air hose connection
with fi lter and regulator where leaks are
common.
Compressed-air systems that are poorly maintained have leaks in the range
of 20–30% of the compressed air output (Figure D179). If a good leak
detection and repair program is implemented, this value can be reduced
to lower than 10%. Such a high rate of leaks requires unnecessary equip-
ment to operate and can cause system pressure drops that affect the per-
formance of adjacent process equipment. A leak through an opening having
an effective diameter of 1/8 in can result in a operating cost loss of more
than $1,000, assuming constant operation and electricity at $0.10 per kWh.
Common leak locations are at couplings, fi ttings, hoses, pipe joints, dis-
connect fi ttings, valves, and pressure regulators. It is best to look for leaks
when the production equipment is not operating—on a weekend, or in the
middle of the night. The use of an ultrasonic detector will aid greatly in
fi nding these leaks.