Retrotec USACE User Manual
Page 464
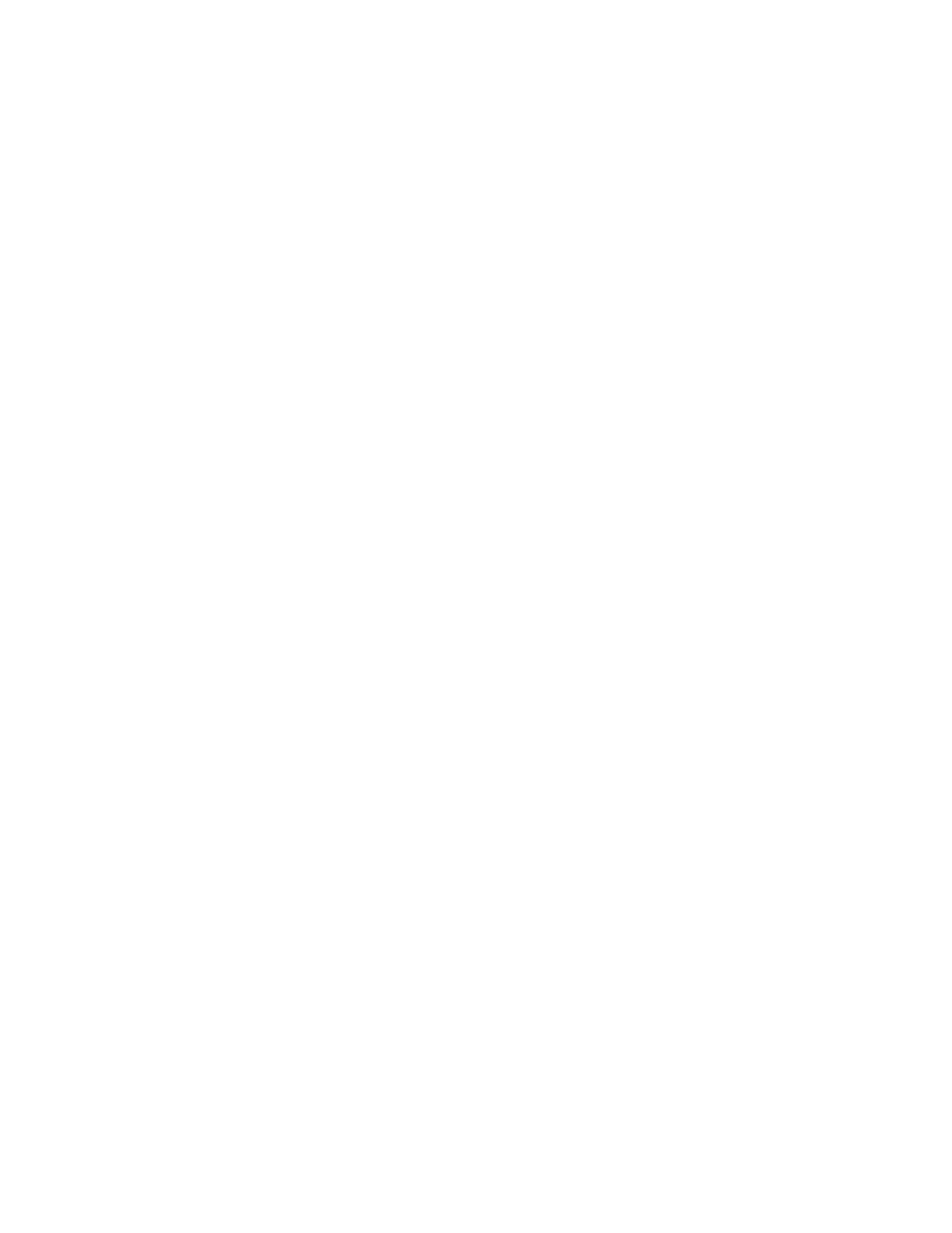
IND4 ENERGY & PROCESS ASSESSMENT PROTOCOL
virtual training facilities, L19
water systems, L6–L8
welding,
L17–L18
European terminology, 17–18
Federal Energy Management Program (FEMP),
55–56
Floors
penetrations of, D10
poor slab-on-grade insulation, D10
poor slab over unheated basement insulation, D9
Foundry operations
outside furnace temperature, D119–D120
oversized equipment, D120
running exhaust systems when not required, D119
Furnace operations
automatic stack damper, lack of, D127
burners,
ineffi cient, D128
controls,
D121–D122
cooling water, waste of heated, D129
cycling on and off during low loads, D126
damaged or missing refractory, D123
dampers, improper operating, D121
dirty burners, D120–D121
fast melting rates during low metal demand periods,
D125
fl ue exhaust, combustible gases in, D122
fl ue gases, excess oxygen in, D126
fuel oil too cold for good atomization, D128–D129
heaters, use of underfi red, D129
hot clean exhaust air exhausted outside, D125–D126
leaks around doors, D124
openings used for charging too large, D123–D124
pilot, continuously lit, D127
temperature not reduced in standby mode,
D124–D125
wet and cold materials to be heated, D125
Heating and cooling systems
air
fl ow, excessive, D33
chilled water pipes, poorly insulated, D36–D37
coils, poor selection of cooling/dehumidifi cation,
D29–D30
condensate water, use of, D33
dampers, excessive use of, D34
dampers, inoperable, D31
dehumidifi cation systems, ineffi cient, D28–D29
dependence on only unit heaters, D26
dirty
fi lters or coils, D34
duct air leaks, D32
duct and piping insulation, lack of, D31
fan belts, loose, D32
fan coil units in unconditioned space, D30
fan, use of ineffi cient, D33
forced air heating in large high bay areas, D25–D26
hot air exhausted to outside, D27
Energy assessment procedure
agreement on, 31
assessments,
13
benchmarking energy data, 11–12
building design documents and, 33–34
cost and tariff analysis, 37–40
data and material needed from site, 32–34
installation of smart meters and submeters, 12
management,
5
metering and data collection, 10–11
on-site assessment work, 40
organization of, 7–8
preassessment site visit, 31–32
preparation activities, 32
protocols
for.
See Protocols, energy assessment
setting up energy monitoring and targeting, 8–9
site work arrangements, 34–35
team kick-off meetings, 35–37
time span and, 5–6
using a building management system (BMS), 44–45
working procedure, on-site, 40–42
Energy assessment reports
aim of, 48
meeting with client/site staff, 52
monitoring, summary data for, 51–52
quality check, 51
recommended structure, C1–C4
typical report contents, 48–52
Energy assessment technologies for energy
management, 59–60
Energy audit. See Energy assessment
Energy Conservation in Buildings and Community
Systems (ECBCS), xxii
Energy conservation measures (ECMs)
building envelope, L1–L3
catering facilities, L18–L19
chiller system, L10–L11
compressed air system, L11–L12
electric systems, motors, pumps, fans, L14
energy generation and distribution, L8–L10
high-cost measures, 51
HVAC distribution systems, L5–L6
HVAC systems, L3–L5
lighting,
L13
machining,
L16
maintenance plan, regular, L20–L21
medium-cost measures, 51
no-cost/low-cost measures, 50–51
painting,
L15–L16
photo and X-ray processing, L20
plating and metal fi nishing, L16
process control, L20
process systems, general, L14–L15
rules of thumb for utility system, I1–I7
swimming pool, L19
thermal storage and heat pumps, L12–L13