Retrotec USACE User Manual
Page 246
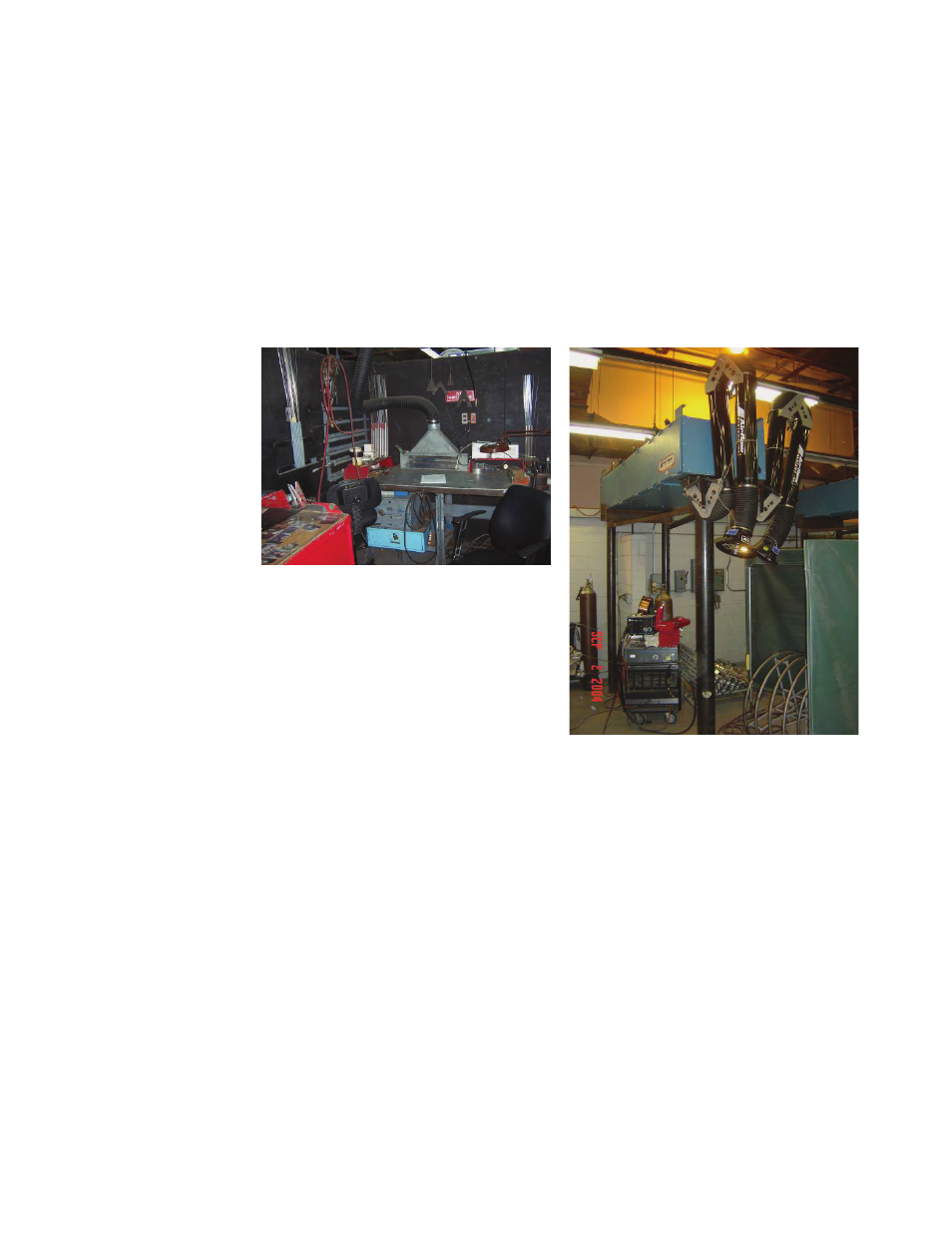
D116 ENERGY & PROCESS ASSESSMENT PROTOCOL
after the welding is completed. These are all in addition to actually welding.
Some weld stations are set up for a specifi c type of weld and thus are not in con-
tinuous use. If the welding stations are serviced by an exhaust system that runs
all the time, the energy consumed to power the exhaust fan and the makeup
air fan is not used effi ciently. In addition, excessive energy is used to heat and
cool makeup air. See also “Demand-Based Ventilation System.” Figure D181
shows a welding shop that has a constant volume centralized welding exhaust
system that operates continuously, and one with a recirculating local exhaust
system (right).
D.7.4.2 Using Stationary Welding Hoods (Ineffi ciency)
Figure D183. Weld exhaust system with
moveable hood that can be placed at
multiple locations to capture welding fumes.
Figure D182. Stationary hood in a welding
booth that works well for small parts—but
for larger parts it would be ineffective.
For effective capture of welding fumes, the use of stationary or fi xed hoods
(Figure D182) at welding stations should be replaced with movable hoods
(Figure D183). These hoods can be positioned to best remove welding fumes
generated from the part being welded. The use of stationary hoods often re-
sults in not capturing all the welding fumes. With a movable hood, the hood
can be positioned closer to the welding location, and good capture of the fumes
can be obtained with a minimum exhaust air fl ow. The use of stationary hood
requires more air, and more fan motor energy is used—plus, additional heating
is required to temper the air in winter.
D.7.4.3 Excessive Welding Fume Generation (Ineffi ciency)
Clean air for welding operations is provided by ventilation systems, which typi-
cally consist of process and local exhaust systems and general ventilation supply
and exhaust systems. The most effi cient method of contaminant control in the