Retrotec USACE User Manual
Page 252
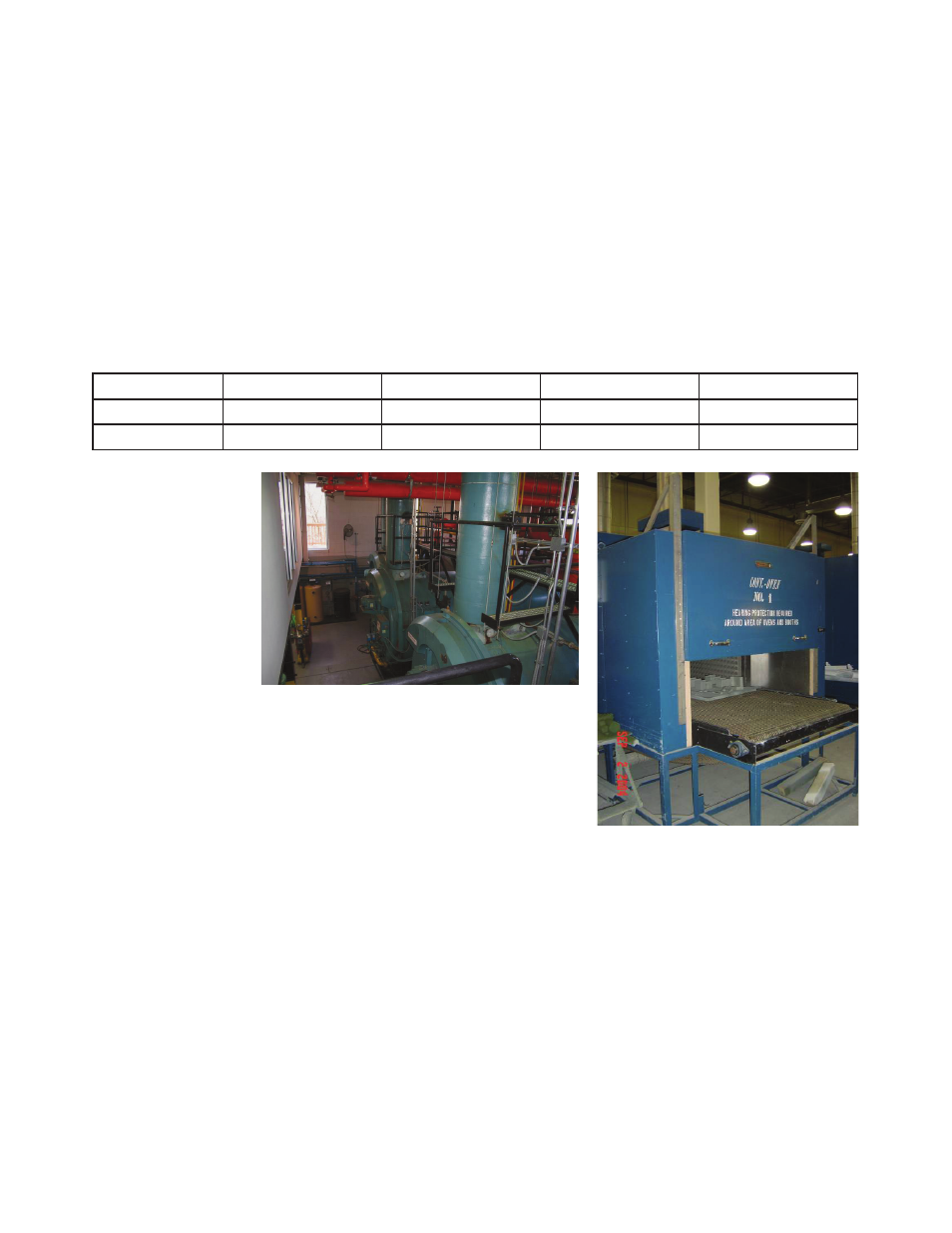
D122 ENERGY & PROCESS ASSESSMENT PROTOCOL
Furnace and oven burner controls monitor the chamber temperature and
stack draft to establish fi ring rates and proper fuel air mixture (Figures D193–
D195). Controls should be installed on furnaces and ovens that lack them
(Figure D196). Providing complete combustion with minimal excess air is the
goal for peak energy effi ciency. The furnace and oven controls should measure
the amount of carbon monoxide, oxygen, or carbon dioxide and then make ad-
justments in the fi ring rate and the amount of air passing through the burner.
For effi cient operation, carbon monoxide is the best monitor, but it is also the
most expensive. Carbon dioxide works well if only one fuel type is in use. The
sensing of oxygen may give false readings due to air leaks into the fl ue. Based
on a fl ue gas temperature of 177 °C (350 °F), the following are good operating
conditions for effi cient operation:
Fuel
Excess Air
Oxygen
Carbon Monoxide
Carbon Dioxide
Natural gas
7%
1.5%
<100 ppm
11%
#2 fuel oil
10%
2%
<100 ppm
14.1%
Figure D196. Oven in paint shop with no
combustion controls.
Figure D195. Combustion gas monitors located
in breeching to analyze products of combustion.
D.7.8.4 Combustible Gases in the Flue Exhaust (Waste)
If there is a presence of high levels of carbon monoxide, unburnt natural gas,
or high levels of soot in the combustion gases, inadequate oxygen is present in
the burner for proper combustion. Poor furnace and oven effi ciency will be
the result. If the concentration of combustible gases is too high, an explosive
mixture could be present, presenting a signifi cant danger to the furnace and
oven. This condition can be caused by faulty boiler controls, inoperable damp-
ers, and dirty burners.