Retrotec USACE User Manual
Page 383
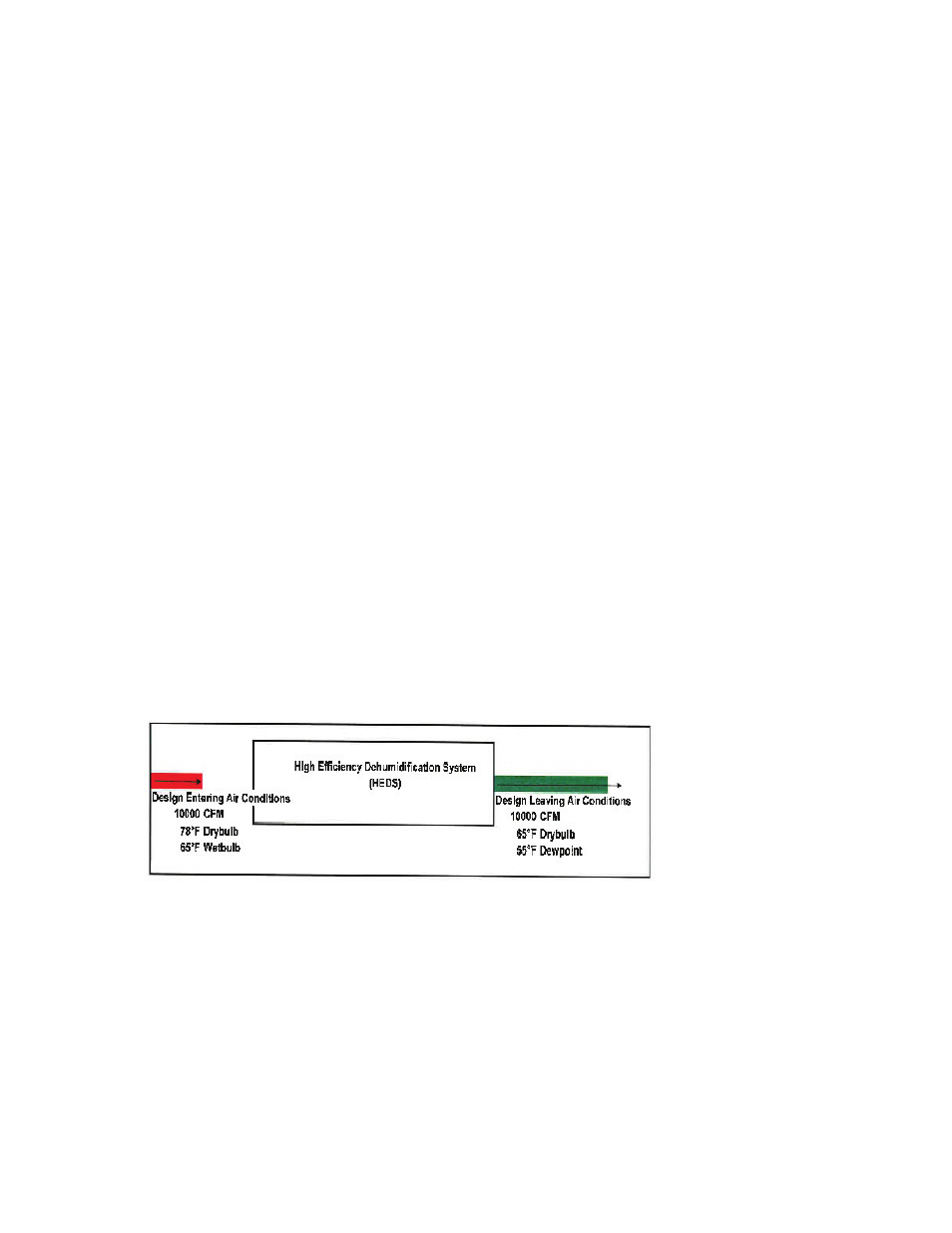
Appendix J J7
their design or small cooling coils, colder water and higher fl ow rates of chilled
water will be required. This can create a very ineffi cient cooling system and
can contribute directly to the “Low Delta T Syndrome.”
Air distribution systems that have “normal” designs and cooling coil sizes
have a detrimental effect on chiller plant performance.
For example, a cooling coil that requires 5.6 °C (42 °F) chilled water
supply temperature and provides a 12.2 °C (54 °F) return water temperature
to meet cooling loads and provide adequate dehumidifi cation will cause the
chiller plant to use 25–40% more energy than a cooling coil selected to provide
the design supply air temperature and the design dehumidifi cation load with
10 °C (50 °F) chilled water supply and 21.1 °C (70 °F) chilled water return
will require. If a HEDS-designed AHU is utilized, the chiller plant savings will
increase by another 25% or more.
When design dehumidifi cation loads exist, there is typically the need for
some form of reheat energy to temper the air entering the spaces. Reheat
energy typically comes from a new source of energy, typically a boiler plant
connected to steam or hot water sourced reheat coils, or electric strip reheat
coils.
Cold, saturated air entering a humid space can cause condensation to form
on surfaces that it comes in contact with, creating wet spots and all of the prob-
lems that go along with water on surfaces in occupied areas, so some form of
re-heat or a method to decrease the relative humidity of the air entering the
space is required.
For a system such as a DOAS design or a VAV system serving a barracks
facility, the design day chiller plant and boiler plant energy savings associated
with a HEDS system can be in excess of 50% when compared to a typical
design.
Figure J6. High Effi ciency Dehumidifi cation System.
Supply air temperature is 10°F above the dew point temperature.
For DOAS-HEDS, the supply air temperature can be 20° F above the
dew point temperature.