Preventative maintenance schedule, Tachometer usage, When is a tachometer required – Rockwell Automation 7000 PowerFlex Medium Voltage AC Drive (B Frame) - ForGe Control (PanelView 550) User Manual
Page 256: Preventative maintenance schedule tachometer usage
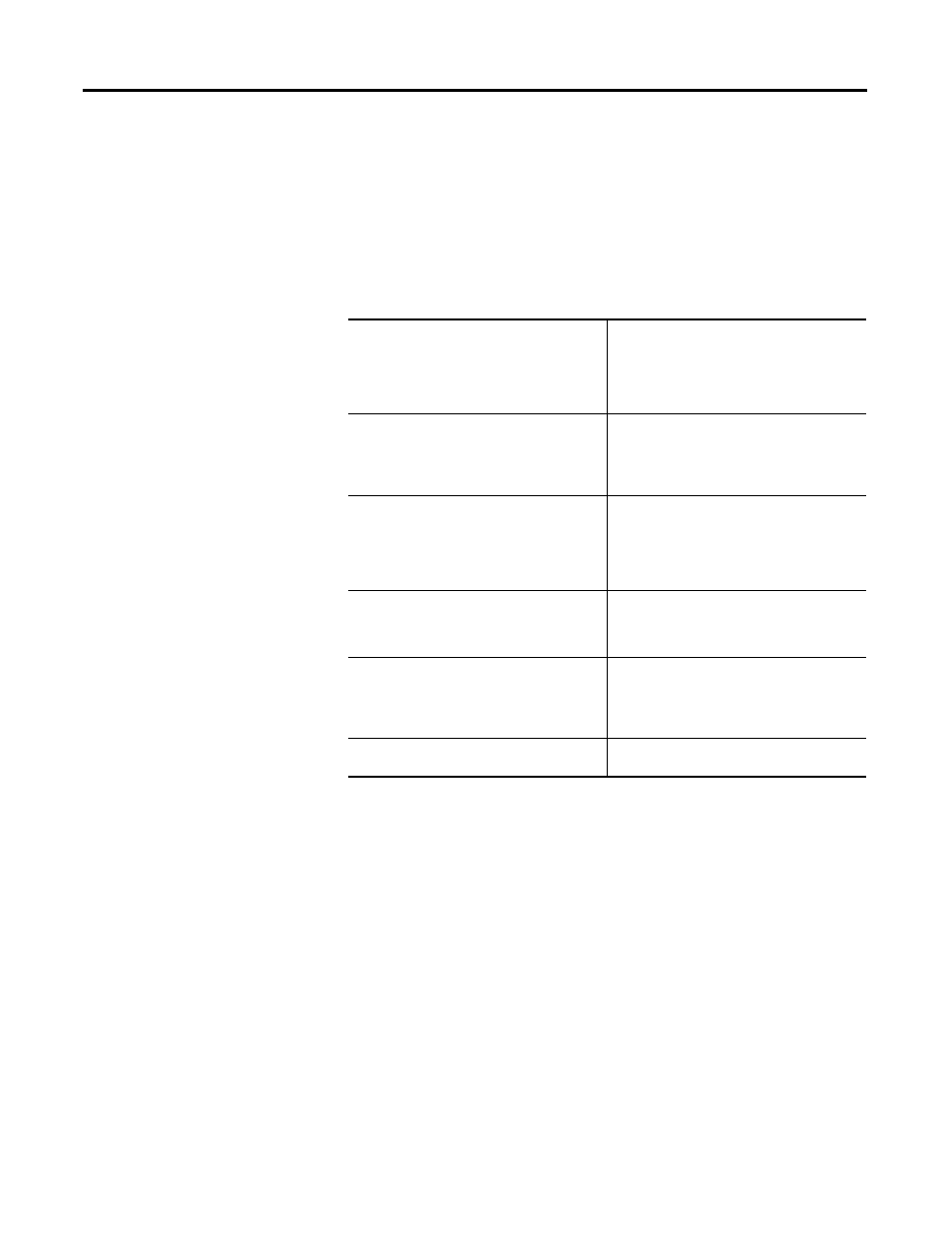
256
Rockwell Automation Publication 7000-UM151E-EN-P - January 2013
Appendix A General Reference
Preventative Maintenance
Schedule
Rockwell Automation recognizes that following a defined maintenance schedule
improves your drive’s performance and operational lifespan. By rigorously
following this maintenance schedule, you can expect the highest possible uptime.
Annual maintenance includes a visual inspection of all drive components visible
from the front of the unit, resistance checks on the power components, power
supply voltage level checks, general cleaning and maintenance, checking of all
accessible power connections for tightness, and other tasks. These tasks are
described in great detail in the PowerFlex 7000 “B” Frame User Manual.
Tachometer Usage
When is a Tachometer Required?
A tachometer is required under the following conditions:
1. When speed regulation accuracy must be between 0.01 – 0.02% of
nominal speed.
2. When the zero speed breakaway torque needed is greater than 90% of
continuous running torque.
3. When continuous running speed is greater than or equal to 0.1 Hz, but less
than 6 Hz.
4. For minimizing restart times using the flying start capability in forward or
reverse direction.
I – Inspection
This indicates that the component should be
inspected for signs of excessive accumulation of
dust/dirt/etc. or external damage (e.g. looking at
Filter Capacitors for bulges in the case,
inspecting the heatsinks for debris clogging the
air flow path, etc.).
M – Maintenance
This indicates a maintenance task that is outside
the normal preventative maintenance tasks, and
can include the inductance testing of Line
Reactors/DC Links, or the full testing of an
isolation transformer.
R – Replacement
This indicates that the component has reached
its mean operational life, and should be replaced
to decrease the chance of component failure. It
is very likely that components will exceed the
design life in the drive, and that is dependent on
many factors such as usage, heating, etc.
C – Cleaning
This indicates the cleaning of a part that can be
reused, and refers specifically to the door-
mounted air filters in the liquid-cooled drives and
some air-cooled drives.
Rv – Review
This refers to a discussion with Rockwell
Automation to determine whether any of the
enhancements/changes made to the Drive
Hardware and Control would be valuable to the
application.
RFB/R – Refurbishment/Replacement
The parts can be refurbished at lower cost OR
the parts can be replaced with new ones.