Returning your unit, Troubleshooting controllers, Process and deviation alarms – Watlow CLS200 User Manual
Page 180
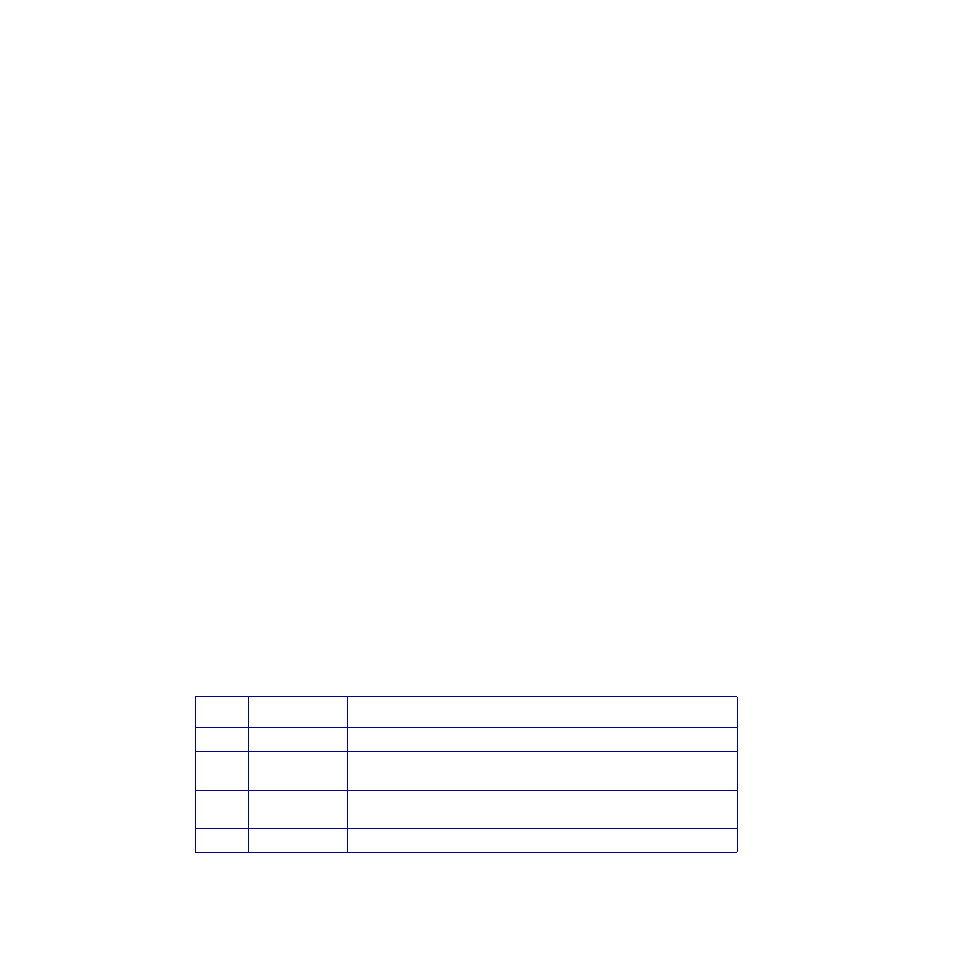
Chapter 9: Troubleshooting and Reconfiguring
CLS200 Series User’s Guide
164
Watlow Anafaze
Doc.# 0600-3050-2000
If you are certain the installation is correct, you can try re-
placing the controller. If the second unit works correctly,
then the problem is specific to the controller you replaced.
Returning Your Unit
Before returning a controller, contact your supplier or call
Watlow for technical support.
Controllers purchased as part of a piece of equipment must
be serviced or returned through the equipment manufac-
turer. Equipment manufacturers and authorized distribu-
tors should call customer service to obtain a return
materials authorization (RMA) number. Shipments with-
out an RMA will not be accepted. Other users should con-
tact their suppliers for instructions on returning products
for repair.
Troubleshooting Controllers
A problem may be indicated by one or more of several types
of symptoms:
•
A process or deviation alarm
•
A failed sensor alarm
•
A system alarm
•
Unexpected or undesired behavior
The following sections list symptoms in each of these cate-
gories and suggest possible causes and corrective actions.
Process and Deviation Alarms
When a process or deviation alarm occurs, the controller
switches to the single loop display for the loop with the
alarm and displays the alarm code on the screen. Software
such as AnaWin or WatView displays a message on the
alarm screen and logs the alarm in the event log.
Table 9.1
Controller Alarm Codes for
Process and Deviation Alarms
Code
Alarm
Description
HP
High Process
Process variable has risen above the high process alarm setpoint.
HD
High Deviation
Process variable has risen above the setpoint by more than the devia-
tion alarm value.
LD
Low Deviation
Process variable has dropped below the setpoint by more than the
deviation alarm value.
LP
Low Process
Process variable has dropped below the low process alarm setpoint.