Heat and cool outputs – Watlow CLS200 User Manual
Page 172
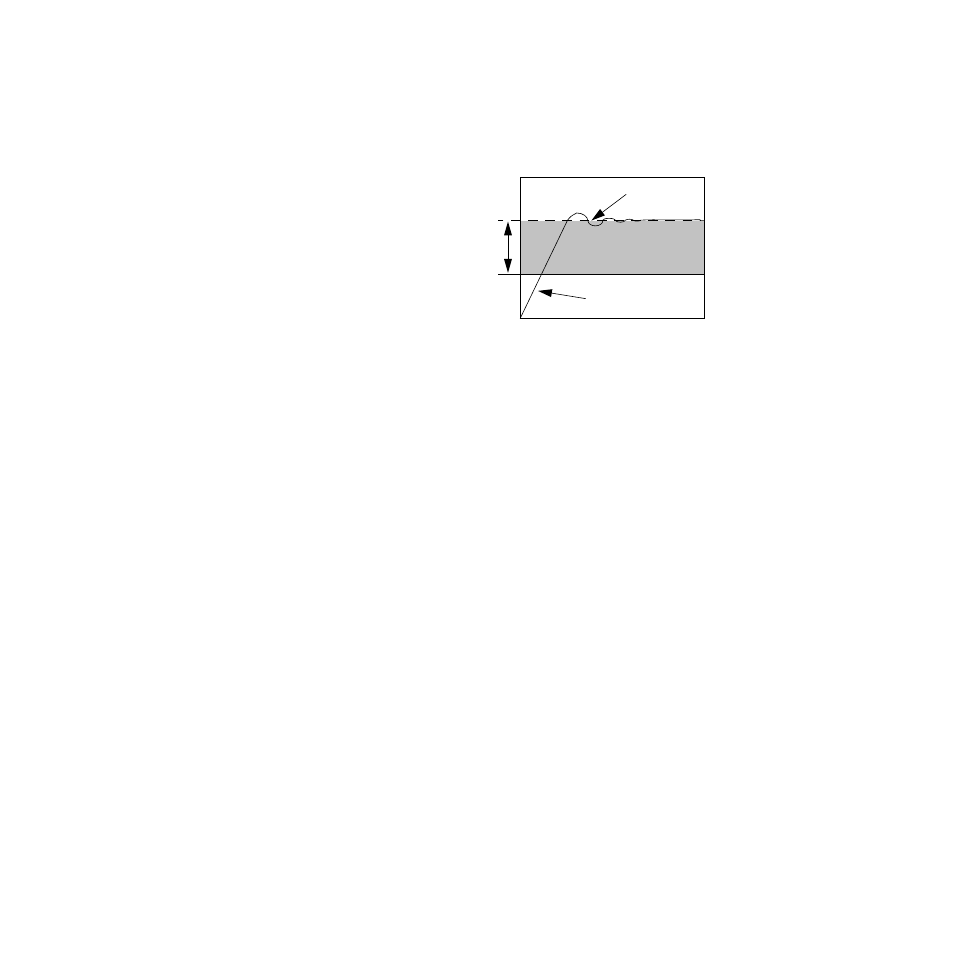
Chapter 8: Tuning and Control
CLS200 Series User’s Guide
156
Watlow Anafaze
Doc.# 0600-3050-2000
rapidly approaching the setpoint from below, derivative
control reduces the output, anticipating that the process
variable will reach setpoint. Use it to reduce overshoot and
oscillation of the process variable common to PI control.
Figure 8.4 shows a process under full PID control.
Figure 8.4 Proportional, Integral and Deriva-
tive Control
Heat and Cool Outputs
Each loop may have one or two outputs. Often a heater is
controlled according to the feedback from a thermocouple,
in which case only one output is needed.
In other applications, two outputs may be used for control
according to one input. For example, a system with a heater
and a proportional valve that controls cooling water flow
can be controlled according to feedback from one thermo-
couple.
In such systems, the control algorithm avoids switching too
frequently between heat and cool outputs. The on/off algo-
rithm uses the SPREAD parameter to prevent such oscilla-
tions (see Spread on page 92). When PID control is used for
one or both loop outputs, both the SPREAD parameter and
PID parameters determine when control switches between
heating and cooling.
Proportional
Setpoint
Process Variable
Band