Update information no. 11 – HEIDENHAIN TNC 306 Technical Manual User Manual
Page 500
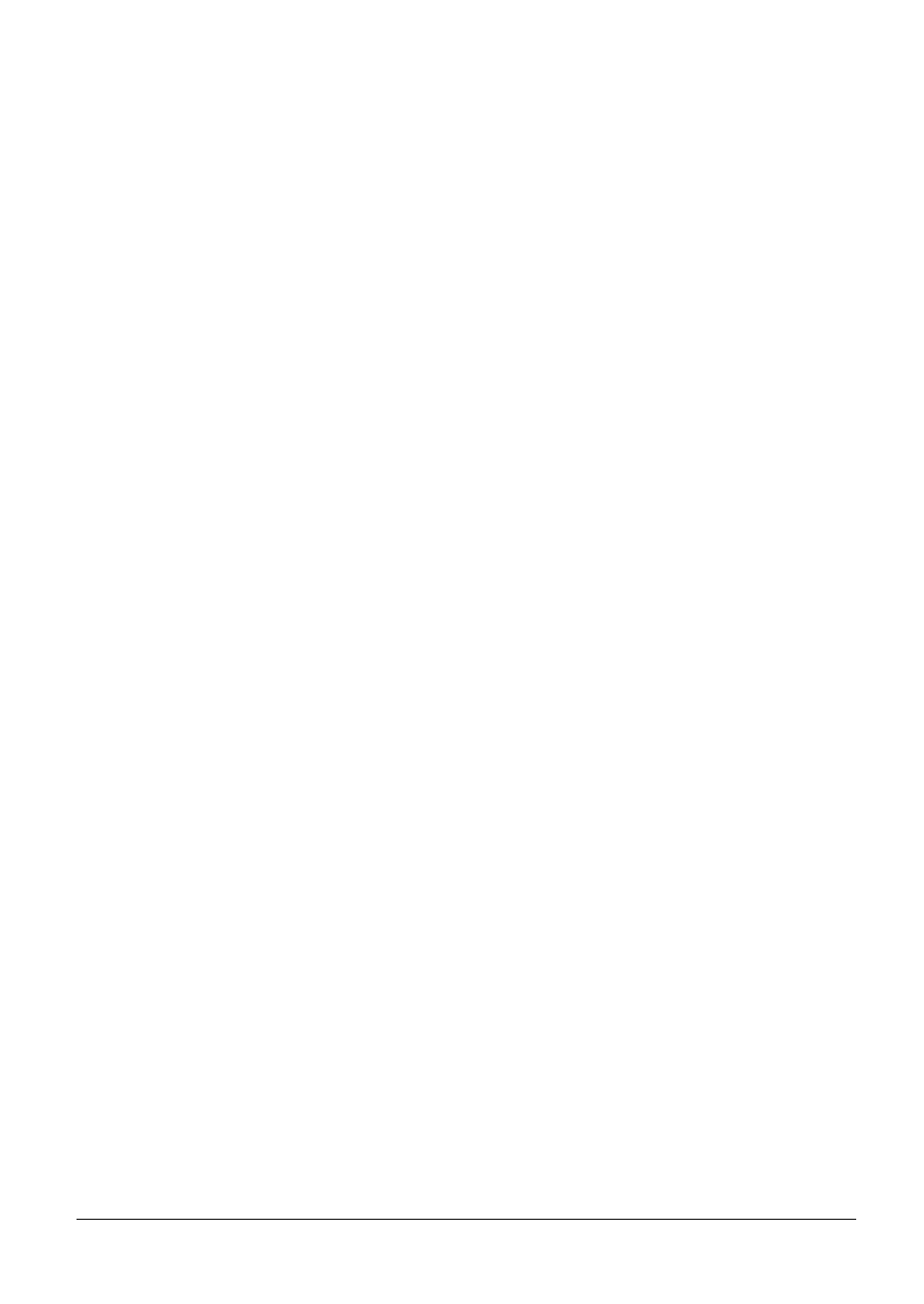
3/97
TNC406/TNC 306
Update Information No. 11
1-1
Update Information No. 11
Software version 15 for the TNC 306 was released at the end of November 1996.
Software version 16 for the TNC 306 was released at the end of January 1997.
Software version 5 for the TNC 406 was released at the beginning of February 1997.
The new software version 15 of TNC 306 introduces the following new features:
• If M36 is active while the "Touch Probe" cycle is running, M37 is automatically output (erosion
switched off).
The new software version 16 of TNC 306 introduces the following new features:
• Functions for HR 410 handwheel are available.
• Output of a step function for machine adjustment
Under the code number 105296 it is possible to start the output of a step function (analog
voltage). The step is adjustable in amplitude (voltage or feed rate) and duration through the arrow
keys. The axis is selected through the axis key. With the step function you can optimize the
servo amplifier adjustment and find the values for acceleration and Kv.
• Sampling rate of the analog signal for gap control
The digital scanning rate of the analog input is now 1 ms. This means that for each cycle, four
analog values are read and their mean value is accounted for in the following control-loop cycle (4
ms). This makes it possible to read input frequencies up to 250 Hz.
• New gap control via gap signal
New MP2081
Input value
= 0 analog input = velocity signal (previous type of gap control)
= 1
analog input = gap signal (new type of gap control)
The previous definition of the analog input for gap control requires that the actual sparking gap is
compared with the nominal spark gap (difference formation for velocity signal) in the generator
(MP2081=0, analog input = velocity signal).
Now you can switch MP2081=1 (analog input = gap signal) so that the values are compared in
the control software. The nominal value is read from the PLC word W524; the actual value is
found in W392. A value of 0 to 500 in W392 corresponds to 0 to 5 volts at the analog input. In
the generator a signal must be formed corresponding to the instantaneous status of the sparking
gap (too small / good / too large).
The following commands are needed in the PLC program for control by gap signal:
- The factor for backward feed rate must be loaded in W522.
- The gap nominal value for "good" must be read in the PLC from the corresponding parameter
(GV, B671) of the active generator setting, converted to a value from 0 to 500 and loaded in
W524.
- The threshold must be loaded in W520.