Commissioning and start-up procedure, 1 code numbers for commissioning, 2 preparation of the machine – HEIDENHAIN TNC 306 Technical Manual User Manual
Page 238: 15 commissioning and start-up procedure
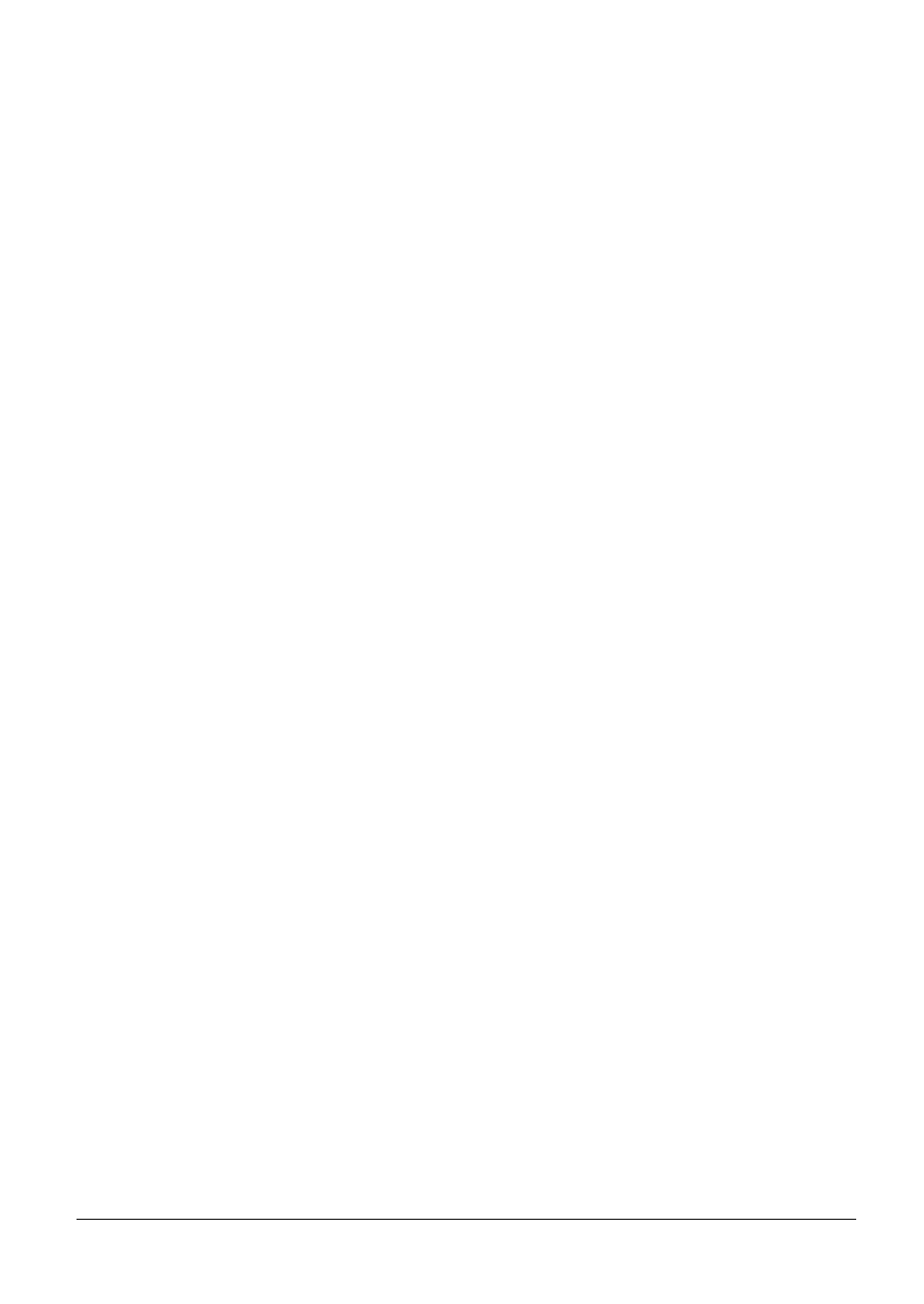
4-138
TNC 406/TNC 306
15 Commissioning and start-up procedure
2/97
15 Commissioning and start-up procedure
This section describes the commissioning procedure for the controls step-by-step. Detailed
descriptions of the functions may be found by referring to the appropriate sections.
15.1 Code numbers for commissioning
Certain operating conditions and functions for the commissioning procedure must be selected by
code numbers (see section "Display and operation").
Code number
Function
95 148
List of machine parameters (see "Machine parameters")
807 667
PLC-operation (see "PLC-programming")
531 210
Erasing the entire physical RAM memory (not NC-programs, erosion tables
and datum shift table)
75 368
Automatic offset adjustment (see section "Servo positioning")
105 296
Non-linear axis error compensation (see "Machine integration")
15.2 Preparation of the machine
The machine is prepared without a control being connected.
For the commissioning of the drive amplifiers please follow the sequence below:
–
Disconnect and short together the nominal value inputs of the drive amplifiers.
0 V must be applied to the input!
–
Connect the servo-enable input to 24 V (normally) and thus activate the servo.
–
Connect the power supply to the drive amplifiers.
–
Rough offset adjustment
. If the axis moves even though the nominal value input is clamped to
0 V, the offset potentiometer must be so adjusted that the axis comes to a stop. After the offset
adjustment remove the short-circuit link on the nominal value!
–
Rough velocity adjustment
. Connect battery supply to the nominal value input. Adjust the battery
supply to 9 V and adjust the drive motor with the tacho-potentiometer to the desired speed
(which equals the maximum rapid traverse rate). The rated speed can be read from the drive
motor with a tachometer.
–
Tuning of the drive amplifier
. As far as the control is concerned, the actual servo-loop consists of
the drive amplifier, motor and axis slide (see section "Servo positioning"). Before the position
control loop in the control can be optimized, the servo-loop must be tuned.
To achieve this, a battery supply is used to apply a (9 V) step function to the nominal value input
of the drive amplifier. The step response of the tachometer signal can be recorded by an
oscilloscope. The axis should be loaded with the permissible workpiece weight while the step
response is being recorded. The subordinate control loop (current control, spindle speed control)
must be so optimized that the step response shows an overshoot.