HEIDENHAIN TNC 306 Technical Manual User Manual
Page 493
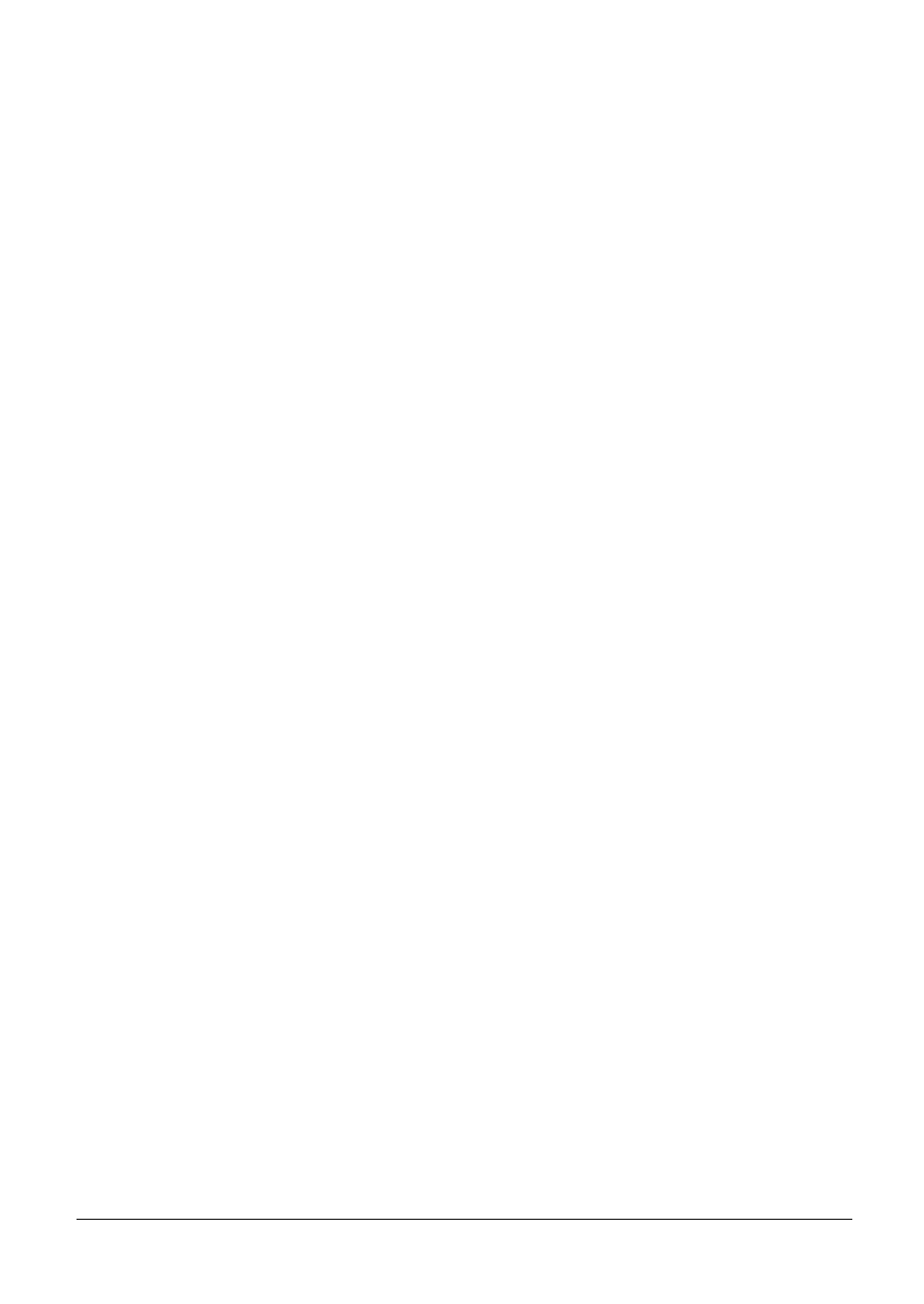
1/98
TNC406/TNC 306
1-5
MP1141 removed: Maximum voltage between two control loop cycles
MP1141 was removed because the acceleration monitoring is now automatic.
MP2190 removed: Constant speed for timing
MP1530 added: Overshoot behavior during acceleration with feedforward
MP1530 has been added. It influences the overshoot behavior during acceleration in the gap control
in feedforward mode.
Input: 0 to 0.999
If MP1530 is programmed to equal 0, the standard value 0.25 is used.
Input value 0.999 = steepest characteristic curve
MP1540 added: Braking behavior during feedforward
MP1540 is also new. It influences braking to a target in feedforward mode.
Input: 0 to 0.999
If MP1530 is programmed to equal 0, the standard value 0.5 is used.
Input value 0.999 = steepest characteristic curve
MP 1550 added: Filter for feedforward
1 = Switch off the filter in the feedforward voltages
MP7655 added: Positioning with the handwheel
1 = Positioning with the handwheel is also effective in the PROGRAMMING AND EDITING mode of
operation.
MP7290.0-5 added: Display step
MP 7290 (axis-specific) sets the display step of the position values. The finest resolution is 1/10 µm.
Value of MP
Resolution of display
µm inch
0
0.1 µm
0.00001
1
0.5 µm
0.00002
2
1 µm
0.0001 (previous resolution)
3
5 µm
0.0002
4
10 µm
0.001
5
50 µm
0.002
6
100 µm
0.01
MP2060 removed: Erosion feed rate for M2620
MP2060 (erosion feed rate if marker 2620 is set) was removed. If the function is needed for special
applications, you can use MP2081=1 to realize a two-position control without characteristic curve.
An other possibility: The threshold for free-run feed rate from MP2141 can be defined with W520
(0..500).
Error handling in the control loop changed
The error messages "gross positioning error ..." and "... measuring system defective" no longer result
in a black screen with blinking error message. Rather they are now shown in the normal error line.
The machine is switched off by an EMERGENCY STOP and the markers M2191 (EMERGENCY
STOP) and M2187 (control loop error) are set. In the event of a "... measuring system defective"
error, after you acknowledge the error message by pressing CE and the EMERGENCY STOP circuit
is reclosed, the control goes into the reference run mode.