Plc positioning, 7 plc positioning – HEIDENHAIN TNC 306 Technical Manual User Manual
Page 124
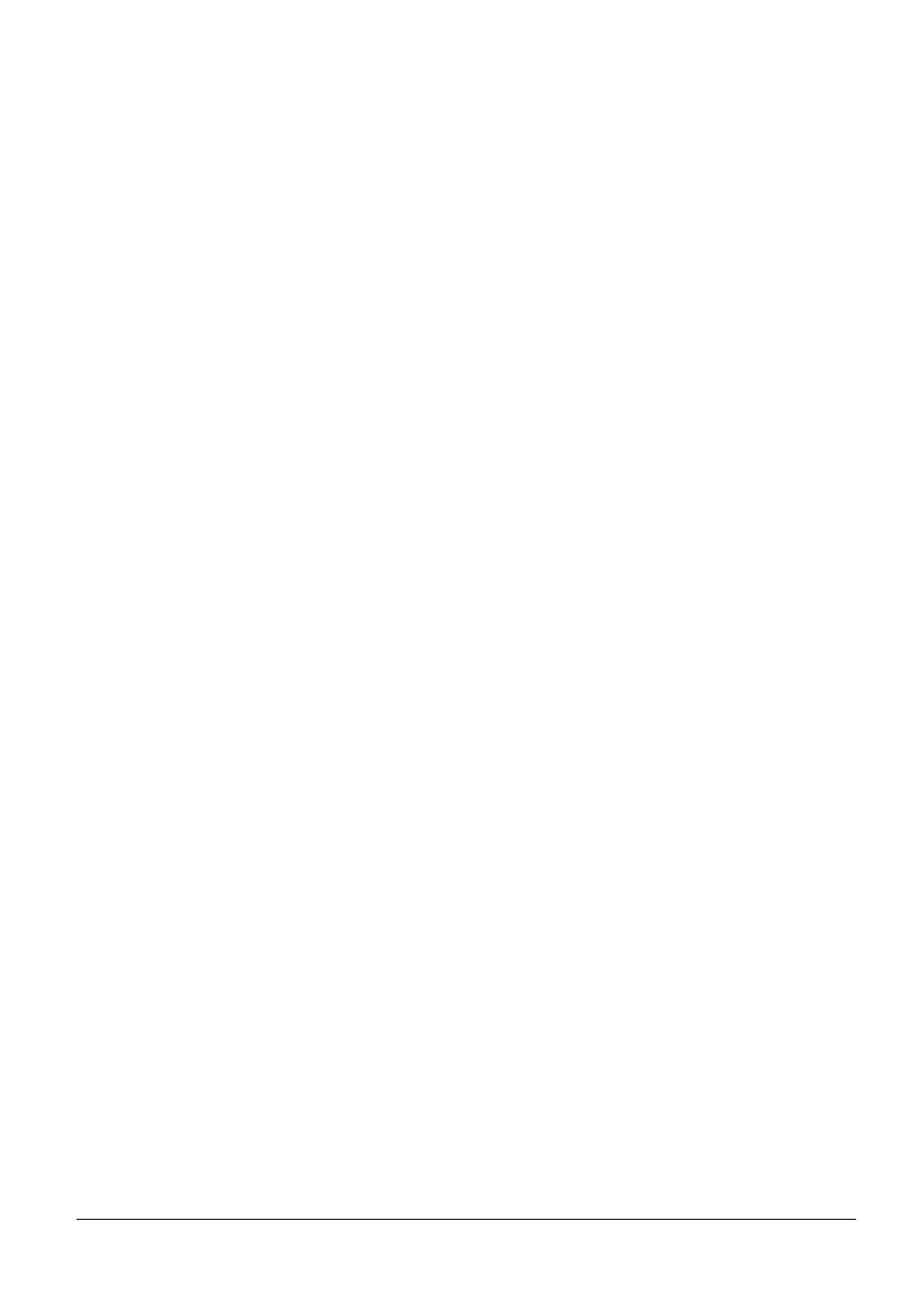
4-24
TNC 406/TNC 306
1 Machine axes
3/97
1.7 PLC positioning
The four axes of the control can also be positioned by the PLC. The positions of the individual axes
must be stored as doublewords (D528 to D540) before activating the positioning.
The feed for positioning the individual axes is stored in W560 to W566.
The transfer of the positions and the feed to the PLC is carried out, for example, by Q-parameters
or machine parameters (MP4210.X, MP4220.X).
All four axes can be traversed simultaneously [simultaneous activation of all the strobe-markers
(M2704 to M2707)].
PLC positioning can be interrupted by resetting the strobe-marker (M2704 to M2707).
The doublewords D528 to D540 have a multiple usage. They have the following meaning for the
PLC positioning:
Address
Function
D528
Position X axis [1/ 1000 mm]
D532
Position Y axis
D536
Position Z axis
D540
Position axis 4
D544 *
Position axis 5
Feed for PLC positioning
W560
Feed X axis [mm/min]
W562
Feed Y axis
W564
Feed Z axis
W566
Feed axis 4
W568 *
Feed axis 5
Set
Reset
M2704
Activate PLC-positioning X axis
PLC
NC
M2705
Activate PLC-positioning Y axis
M2706
Activate PLC-positioning Z axis
M2707
Activate PLC-positioning axis 4
M2708 *
Activate PLC-positioning axis 5
Note:
– The positions refer to the reference marks.
– Software limit switches are not taken into account.
– Tool compensations not calculated.
– The path compensation must be terminated before a PLC positioning.
– PLC positioning is not displayed in the test graphics.
* only TNC 406