Thermostat input, Encoder phasing, Thermostat input -16 encoder phasing -16 – Rockwell Automation 2092-DAx Ultra1500 User Manual User Manual
Page 46: Thermostat, Input
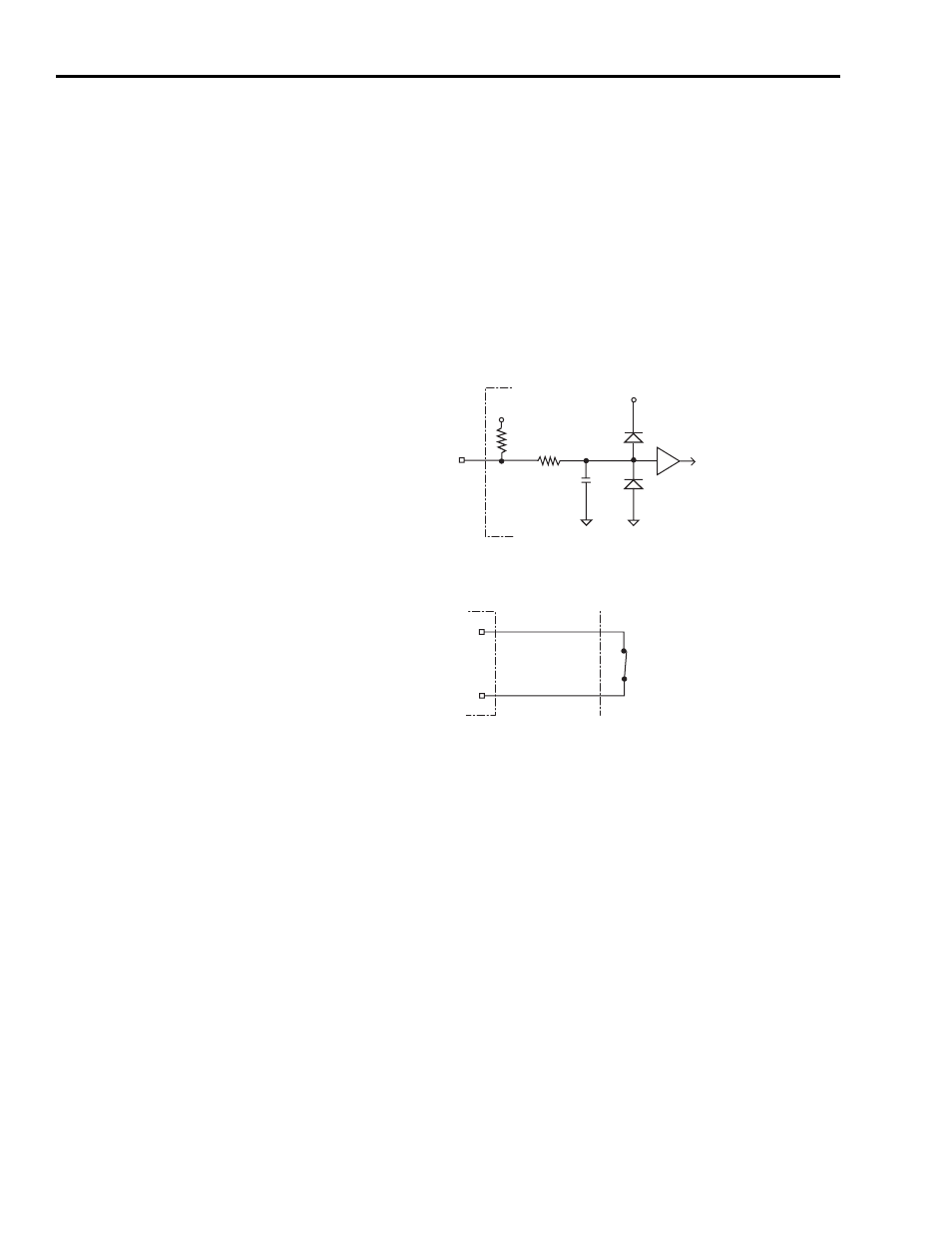
Publication 2092-UM001D-EN-P — July 2005
2-16
Ultra1500 Connector Data
Thermostat
Input
The Ultra1500 can monitor a thermostat or thermistor signal from a motor
and generates a fault if the motor overheats. Figure 2.13 shows the
configuration of this drive input. Figure 2.14 on page 2-16 shows a typical
connection to a motor with a normally closed thermostat. The logic is
designed so that an open or high-impedance condition will generate a fault. If
the motor does not have this signal, the drive can be configured through
Ultraware software to ignore the input.
Figure 2.13
Thermostat Input Configuration
Figure 2.14
Typical Thermostat Connection
Encoder Phasing
For proper motor commutation and control, it is important that the motor
feedback signals are phased properly. The drive has been designed so that a
positive current applied to a motor will produce a positive velocity and
increasing position readings, as interpreted by the drive. Additionally, if Hall
signals are used to initialize the commutation angle, the Hall signals must
sequence properly and the phase relationship to the motor back-EMF signals
must be understood. Figure 2.15 shows the proper sequencing of the Hall
signals when positive current is applied to the motor. If the Hall signals are out
of phase with the back-EMF signals, the drive can be configured through
software to compensate for the phase offset, as long as the sequencing of the
Hall signals is correct. Figure 2.16 shows an example where the Hall signals
have an offset of 60 degrees.
6.8k
Ω
1k
Ω
+ 5 V
+ 5 V
0.01
µF
Logic Ground
Logic Ground
TS
Ultra1500 Drive
TS
ECOM
Ultra1500 Drive
Thermostat
normally
closed
Motor/Encoder