Rockwell Automation 2092-DAx Ultra1500 User Manual User Manual
Page 101
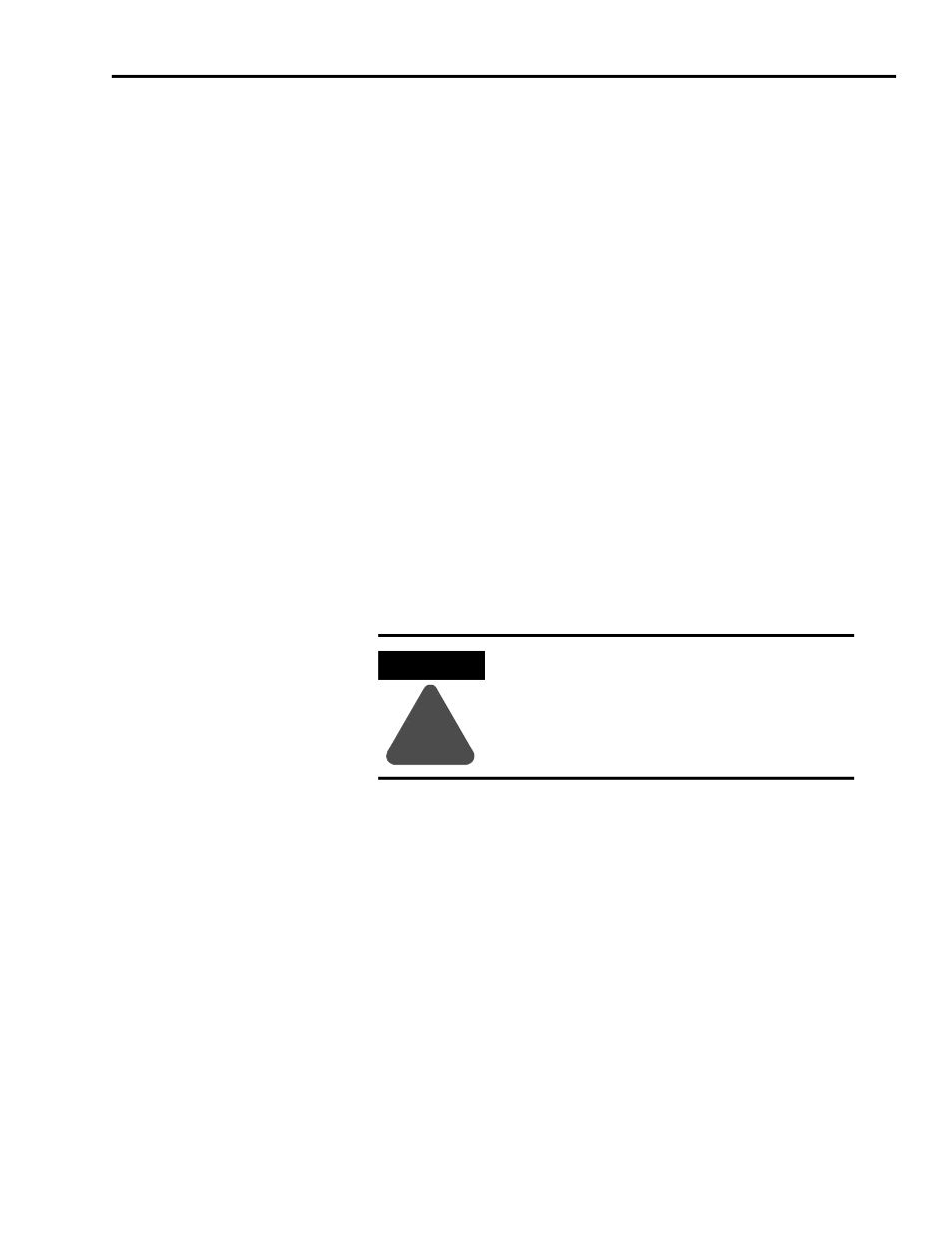
Publication 2092-UM001D-EN-P — July 2005
Ultra1500 Application Examples
5-21
In Figure 5.6 it can be seen that the drive hardware and firmware executes the
following sequence when the active-going transition of the Position Strobe
input is detected:
1. Hold the encoder outputs for 100 ms. The delay provides time for the
controller to prepare its counter to receive multi-turn data.
2. Output the multi-turn revolution data at a fixed output frequency of
1,000,000 counts/second. The length of time for this process step will be
determined by the multi-turn revolution data. (If the multi-turn revolution
data is -1 revolutions, a value of 65535 will be transmitted, resulting in the
maximum time of 66 ms.)
3. Hold the encoder outputs for 100 ms again. This delay provides time for
the controller to read the multi-turn data, and to prepare to receive
single-turn data.
4. Output the fractional revolution data at a fixed output frequency of
1,000,000 counts/second. The length of time for this process step will be
determined by the fractional revolution data. (If the fractional revolution
data is 131071 counts, this step will take the maximum time of 132 ms.)
5. Hold the encoder outputs for 50 ms.
6. The encoder outputs are allowed to track the motor encoder inputs.
Therefore, the following algorithm can be used by a controller to extract the
absolute position from the drive:
1. Ensure that the Ultra1500 drive is disabled, and the motor is stationary.
Any movement of the motor during the absolute transfer process will not
be accounted for by the controller, since the motor encoder inputs are
ignored by the drive during the transfer.
2. Set the digital output of the controller inactive, which means that the
Position Strobe function is off. The A and B encoder outputs of the drive
may still change state.
3. Change the state of the digital output of the controller to active, (meaning
that the input voltage to the drive is 0 Volts and the opto-isolator is turned
ON). This active-going edge will start a time-based sequence in which the
absolute position data is transferred via the A and B encoder outputs of
the drive.
ATTENTION
!
The Ultra1500 does not track any movement of the
motor during the absolute position transfer, which
can take up to 450ms. During this transfer, the motor
should not be moved and the Ultra1500 should be
disabled.