Using the internal dynamic brake, Basic circuit operation, Using the internal dynamic brake -22 – Rockwell Automation 2092-DAx Ultra1500 User Manual User Manual
Page 102: Basic circuit operation -22
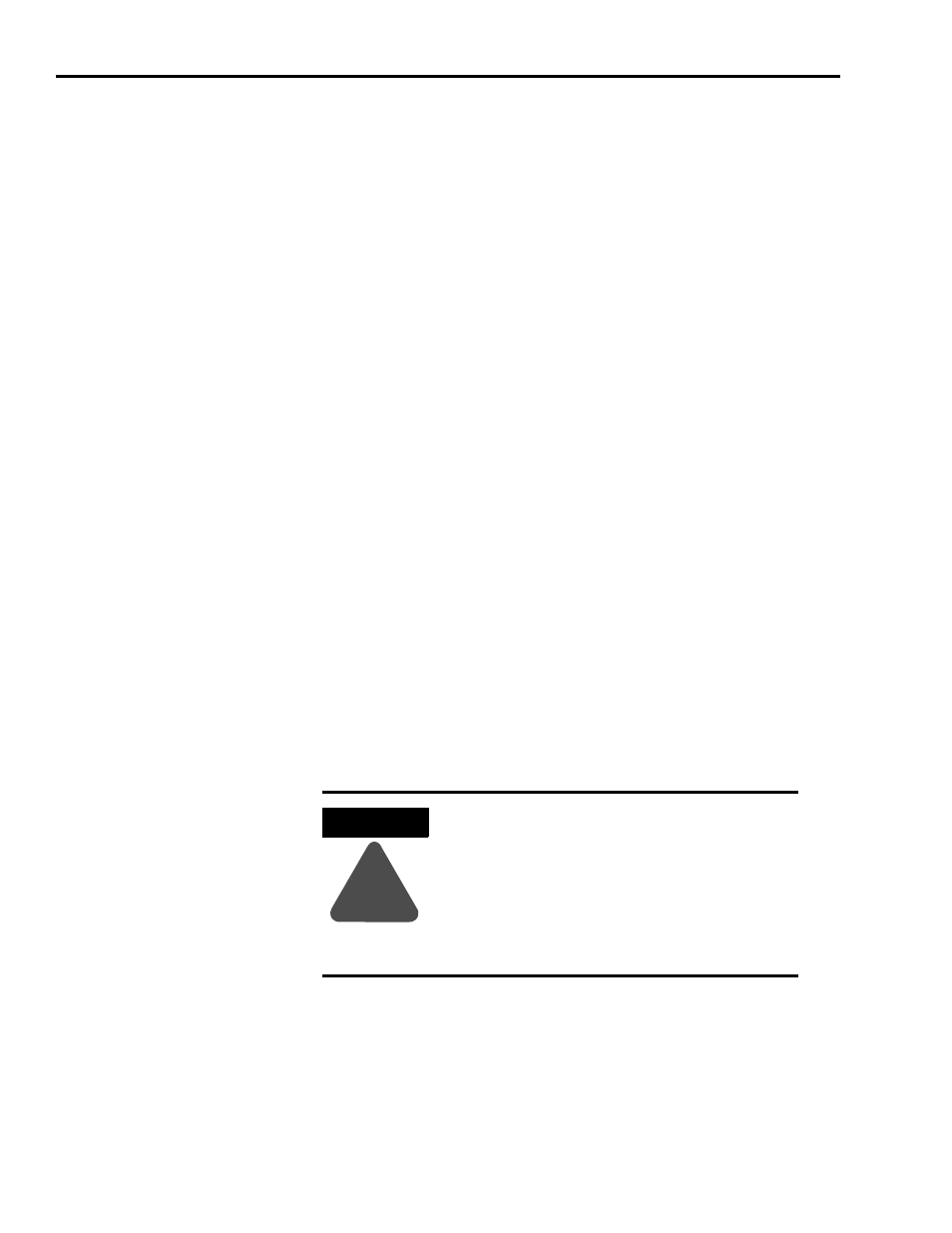
Publication 2092-UM001D-EN-P — July 2005
5-22
Ultra1500 Application Examples
4. Delay 10 ms from the active-going edge of the position strobe, then zero
the position counter of the controller.
5. Delay an additional 175 ms. During this time the drive will increment the
counter in the position controller to correspond to the number of
revolutions of the motor shaft from the zero position.
6. Read the value of the position counter in the controller. Multiply this value
by the number of motor encoder counts per revolution. (In a
ControlLogix application, this is specified as the “Conversion Constant”
for the axis.) The counter value should be interpreted as a 16 bit signed
number. (In a ControlLogix environment, assign the result of the
multiplication to a temporary variable declared as type INT.) The result is
a signed value corresponding to the number of revolutions.
7. Clear the controller position counter in preparation for receiving the
fractional portion of a revolution.
8. Delay another 240 ms. During this time the drive will increment the
position counter to correspond to the fractional portion of a revolution of
the motor shaft from the zero position.
9. Read the value of the position counter and add this to the revolution count
saved in step 6. Set the position counter to this value.
10. The position counter should now be tracking the absolute position of the
drive.
Using the Internal Dynamic
Brake
The Ultra1500 incorporates a dynamic brake relay that can short together the
motor windings under certain conditions. The circumstances in which the
dynamic brake relay is employed are selectable by the user.
Basic Circuit Operation
Figure 5.7 shows the internal arrangement of the dynamic brake relay,
indicated by the NC label. When the dynamic brake relay is engaged, (in the
NC, or normally closed, position), the three motor phases are shorted together
ATTENTION
!
The internal dynamic brake relay does not qualify for
any safety certification. Implementation of safety
circuits and risk assessment is the responsibility of
the machine builder. Reference international
standards EN1050 and EN954 estimation and safety
performance categories. For more information refer
to Understanding the Machinery Directive (publication
SHB-900).