Template 19: two-axis cross feed cycle, Chapter 31 – Rockwell Automation 8520-MUM 9/Series CNC Mill Operation and Programming Manual Documentation Set User Manual
Page 853
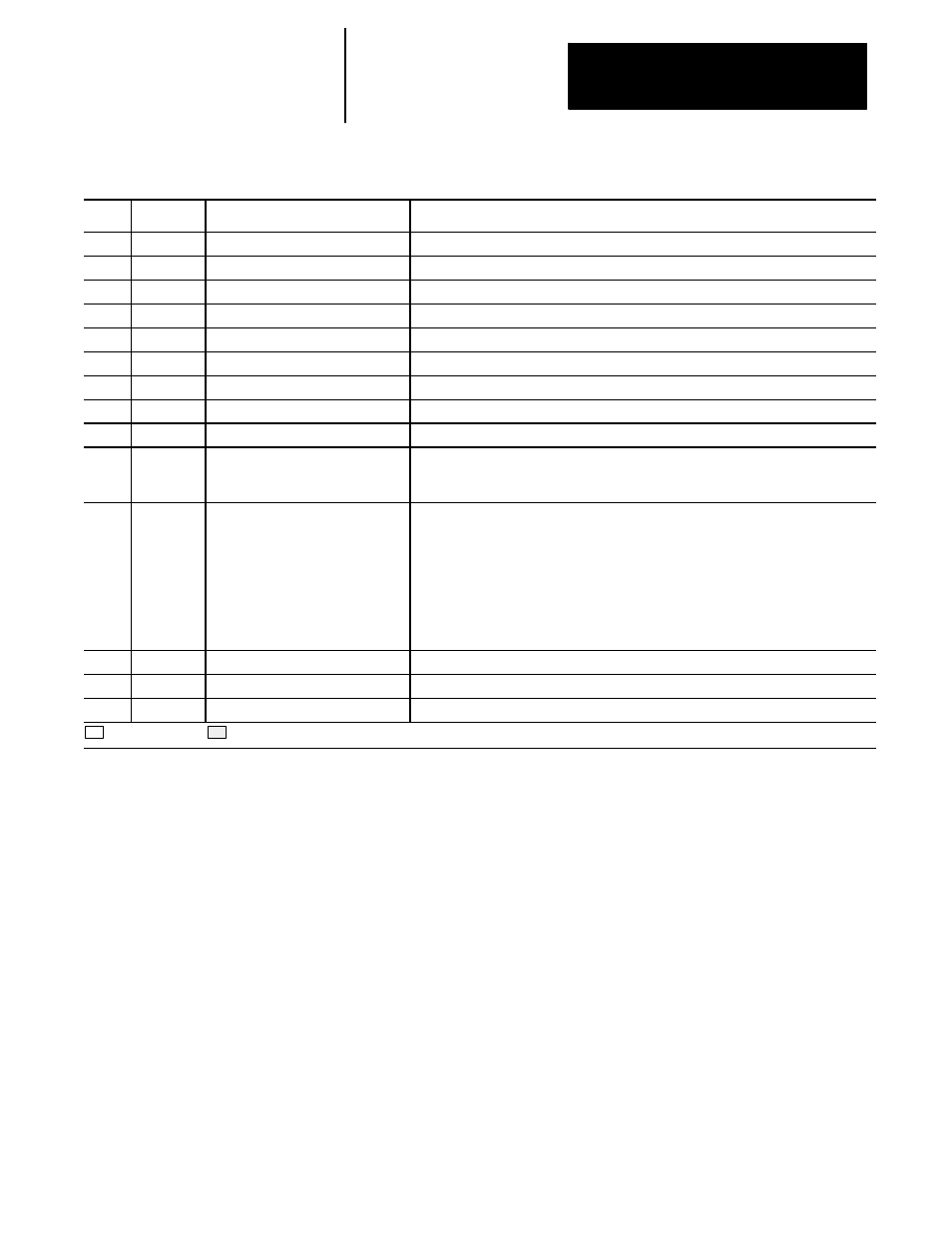
Using Transfer Line Cycles
Chapter 31
31-51
Template 19: Two-Axis Cross Feed Cycle
Letter
Paramacro
Label
Description
F
1
500
MAIN RAPID FEEDRATE
The velocity of the tool as it approaches the part.
X
1
501
MAIN FEED START
The position of the tool as it drills into the part.
F
2
502
MAIN FEEDRATE
The velocity of the tool as it drills into the part.
X
2
503
MAIN FINAL POSITION
The depth of the tool at its final position in the part.
F
3
504
CROSS FEEDRATE (MAX)
The velocity of the tool as it traverses the part.
Y
1
505
CROSS FINAL POSITION
The final position of the tool after it traverses the part.
X
3
506
MAIN RETURN POSITION
The position of the tool when it started the cycle.
Y
2
507
CROSS RETURN POSITION
The position of the slide when it started the cycle.
F
4
508
CROSS RETURN RAPID
The velocity of the slide as it returns to its starting position.
E
509
ADAPTIVE FEED MINIMUM
This is the minimum feedrate at which the control performs an adaptive feed operation.
The control will try to maintain this minimum feedrate, even if it means increasing the
adaptive feed torque percent. For more information on adaptive feed, refer to page 18-9.
Q
510
ADAPTIVE FEED TORQUE %
This is the amount of the selected servo’s continuous rated torque as entered in AMP by
your system installer. Valid ranges are from 1 to 150% of the servo’s rated torque.
Refer to your system installer’s documentation for details on the rated torque of the
servos in your system.
Important: The torque amount applied by the servo is not the cutting force. It is the
torque applied by the servo to the axis. You must calculate the equivalent cutting force
based on your machine dynamics (motor rated torque, lead screw pitch, gearing, tool
dimensions, etc...).
Y
511
CROSS TOOL CHANGE POSITION
The position the slide moves to so that a tool change may be performed.
X
512
MAIN TOOL CHANGE POSITION
The position the tool moves to so that a tool change may be performed.
I
513
HARD STOP SENSE ZONE
The position that indicates to the control that a hard stop is on the axis.
Required entry
Optional entry