Controlled adaptation 245, Self-tuning with heating and cooling processes 245 – West Control Solutions KS98-1 User Manual
Page 245
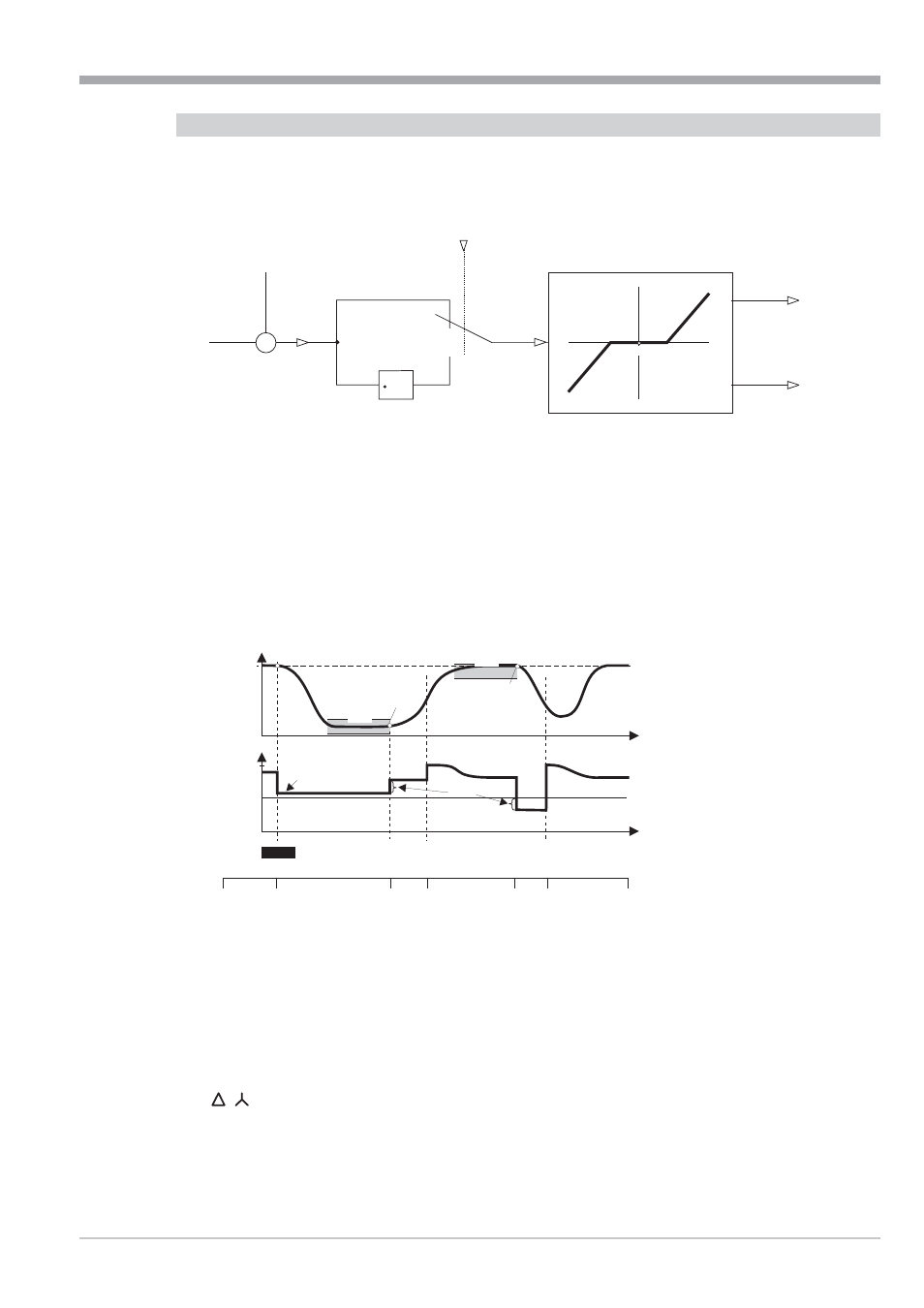
Self-tuning procedure with heating and cooling processes:
(3-point / split-range controller)
Self-tuning starts as with a “heating” process. After self-tuning end, the controller settings based on the calculated
parameters are made. This is followed by line-out at the pre-defined , until PiR is reached again. Subsequently, a step
to cooling is made to determine the “cooling” parameters, in order to determine Tu2 and Vmax2 using the step respon -
se. Based on these characteristics, the controller settings for the cooling process are made.
When cancelling the cooling attempt, the parameters for “heating” are also taken over for cooling. No error message
(
Ada_Err) is indicated.
g
With 3-point stepping controllers, the motor actuator is closed first after starting and opening to
YOptm will occur
only then. This calibration procedure (
Stat: Abgl.) is not shown in the figures.
g
For maintaining a safe process condition, monitoring for an exceeded is done continuously.
a
During self-tuning, the control’ function is switched off! I.e.: Ypid is within the limits of Ymin and Ymax.
a
With
Off controllers, self-tuning is using the function star, i.e.Y2 = 0.
9499-040-82711
Controller
Self-tuning
r controller adaptation to the process
III-245
t
t
Y
100%
0%
-100%
X
W
60s
60s
PiR
PiR
Start
Adaption
Optimization
heating
ready
Optimization
cooling
ready
Start
+
YOptm
dYopt
Off/Ok
PIR_H
Step
Off/Ok
PIR_K
Step
Fig.: 66 Self-tuning with heating and cooling
/ /
Y1
Y2
Xd
Xsh2
Xsh1
Xp2
Xp1
OUT2
OUT1
(-1)
X
W
+
-
Xd = w - x
invers
direct
Xw = x - w
0
Fig.: 67 Principle of direct/invers switchover