Process at rest monitoring 242, Self tuning 242 - 246, Preparation 242 - 246 – West Control Solutions KS98-1 User Manual
Page 242: Process at rest 242
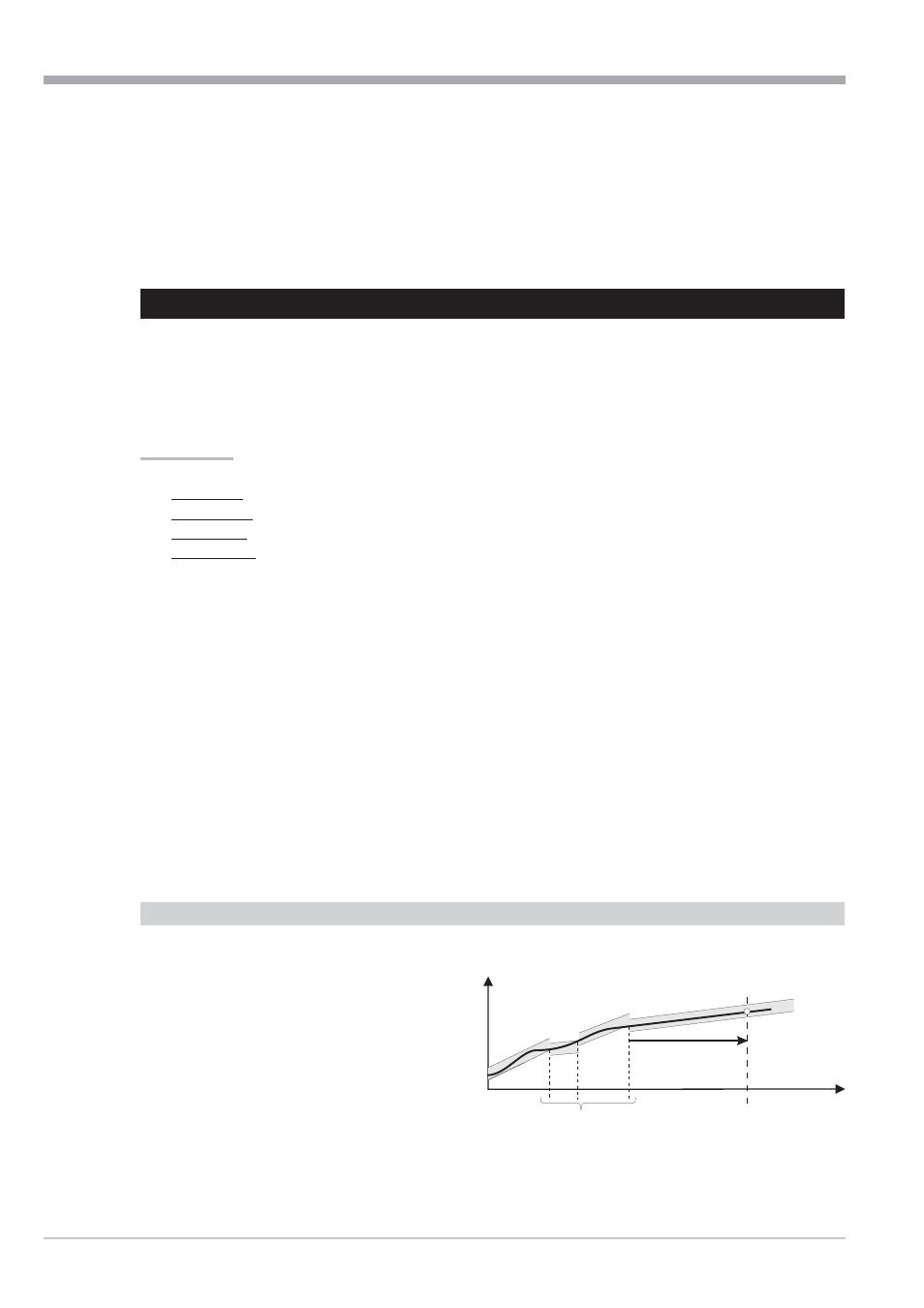
g
For the controlled variable (process value X) the empirical optimization is substantially improved with a writer (or trend
function of the engineering tool) in time requirement and quality, and evaluation of the test results is clearly simplified.
g
The procedure mentioned can only with restrictions be generalized and does not lead to a clear improvement of the
behavior with all controlled systems.
g
Changes of the operating point (Y0), the switching point distance (Xsh) and the lasting switching period (Tp1 and Tp2)
lead to results, which can be better or worse. With 3 - Point - step controllers TM must be adjusted to the real running
time of the conncted actuator.
III-16.7
Self-tuning
r controller adaptation to the process
For determination of optimal parameters a self-optimization can be accomplished.
This is applicable for controlled systems with reconciliation and none dominating dead time and K £ 30%. After start
by the operator the controller initiates an adaptation cycle in order to determine the line characteristic values Tu and
Vmax. It calculates by it the control parameters for fast, overshoot-free correction to the (Xp1, Xp2, Tn, Tv, Tp1, Tp2,
depending upon kind of controller).
Preparation
w
Set the desired controller behaviour
P-controller:
Tn = 0.0
Tv = 0.0
PD-controller:
Tn = 0.0
Tv > 0.0
PI-controller:
Tn > 0.0
Tv = 0.0
PID-controller:
Tn > 0.0
Tv > 0.0
The parameters Tn and/or Tv can be switched off, by being adjusted to the value =
0,0.
Thus they do not participate in the self-optimization.
w
With the automatic controller CONTR+ is to be selected, which parameter set is to be optimized (
POpt=1... 6).
w
Configure conditions for process at rest (
OCond)
The condition designates, when "Prozess at rest" is to be recognized (
PIR_H):
grad=0, grad<0/>0 or grad0 (r also see process at rest, page 242).
w
The correcting variable
YOptm is to be specified. This is, in automatic running, the correcting variable, which is
output with the start of self-optimization in order to generate "Prozess at rest".
w
The step of the correcting variable
dYopt is to be specified. dYopt is the amount the correcting variable
jumps, from the initial value
YOptm and/or in manual operation from the original correcting variable.
w
Consider the reserve
(r also see reserve, page 243)
Process-at-rest’ monitoring (
PiR):
‘Process-at-rest’ monitoring is done at any time. The
proces is at rest, when the process value is within a to-
lerance band of _{X = 0.5% during more than 60 se-
conds. When the process value is out of this band, the
monitoring timeout counter is reset to zero. With detec-
tion of PiR e.g. during control operation and output of a
widely deviating stable correcting variable
YOptm at
self-tuning start, waiting until the full PiR time has
elapsed is required.
With extended monitoring, monitoring is for a constant-
ly varying instead of a constant process variable!
Controller
9499-040-82711
III-242
Self-tuning
r controller adaptation to the process
X
t
Resetting monitoring time counter
PiR (Process at rest)
60s
{X = _0,5%
Fig. 61