Controlled parting using spindle monitoring g991 – HEIDENHAIN CNC Pilot 4290 V7.1 User Manual
Page 292
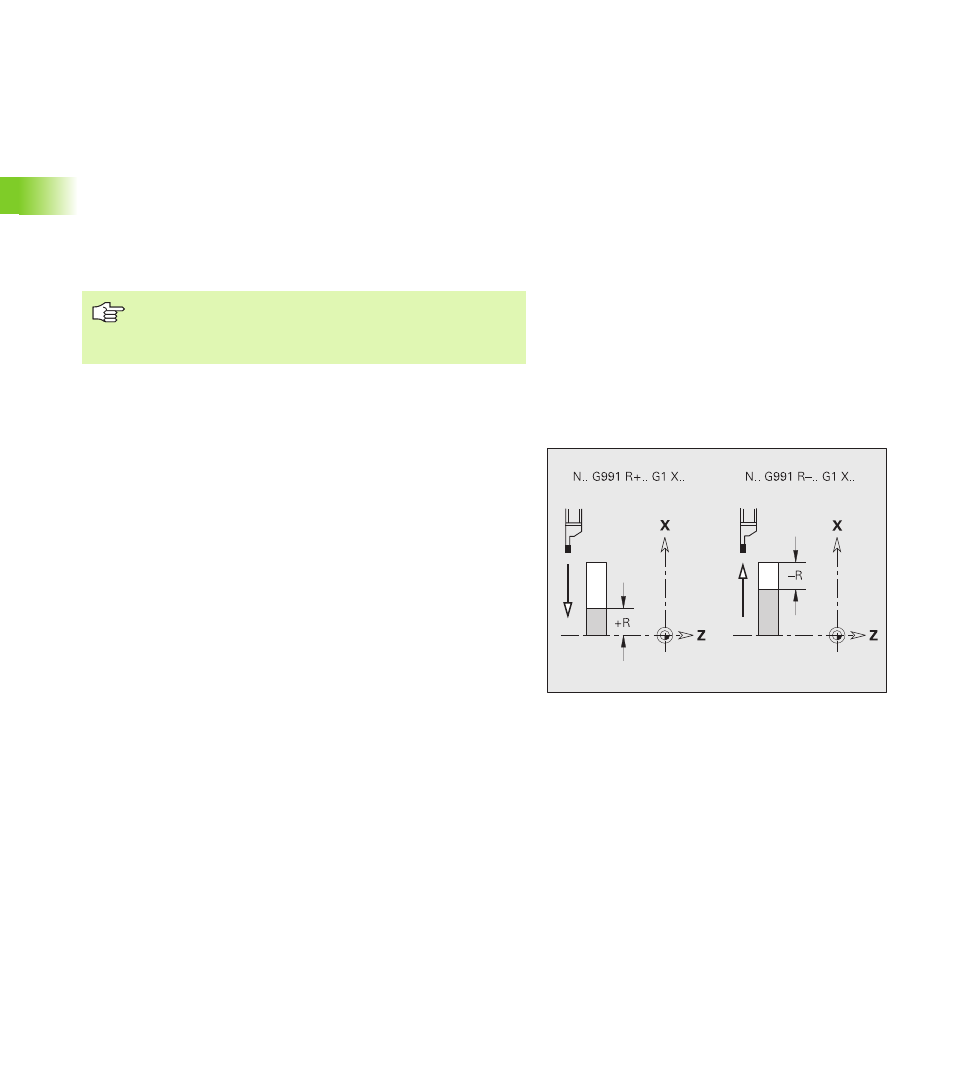
292
4.28 Assignment, S
y
nc
hr
onization, W
o
rk
piece T
ransf
er
Programming:
Program G917 and G1 in one block
Program G1 .. as follows:
For controlled parting: Path > 0.5 mm (to make results)
For checking for smooth parting: Path < width of the parting tool
Result in variable V300
0: Workpiece was not correctly/smoothly cut off (servo lag
detected)
1: Workpiece was correctly/smoothly cut off (no servo lag
detected)
G917 generates an interpreter stop
Controlled parting using spindle monitoring
G991
G991 controls the parting process by monitoring the speed difference
between the two spindles. The spindles are connected in terms of
actuation via the workpiece. After the workpiece has been cut off, the
spindles rotate independently of each other. Speed differences and
monitoring time are stored in machine parameters 808, 858, ... They
can be changed with G992.
In R you specify the path to be monitored and define whether the path
before the workpiece is cut off or the return path is to be monitored
(see illustration).
The CNC PILOT writes the monitoring result into variable V300. G991
generates an interpreter stop.
As of software version 625 952-04:
Lag error monitoring is not activated until the acceleration
phase has been completed.
Parameters
R
Return path (radius value)
No input: The difference in speed between the
synchronously running spindles is checked (once).
R>0: Monitoring of the remaining parting path
R<0: Monitoring of the return path The monitoring
begins with the start of the return path and ends at
return path – R.