21 simple t u rn ing cy cles – HEIDENHAIN CNC Pilot 4290 V7.1 User Manual
Page 237
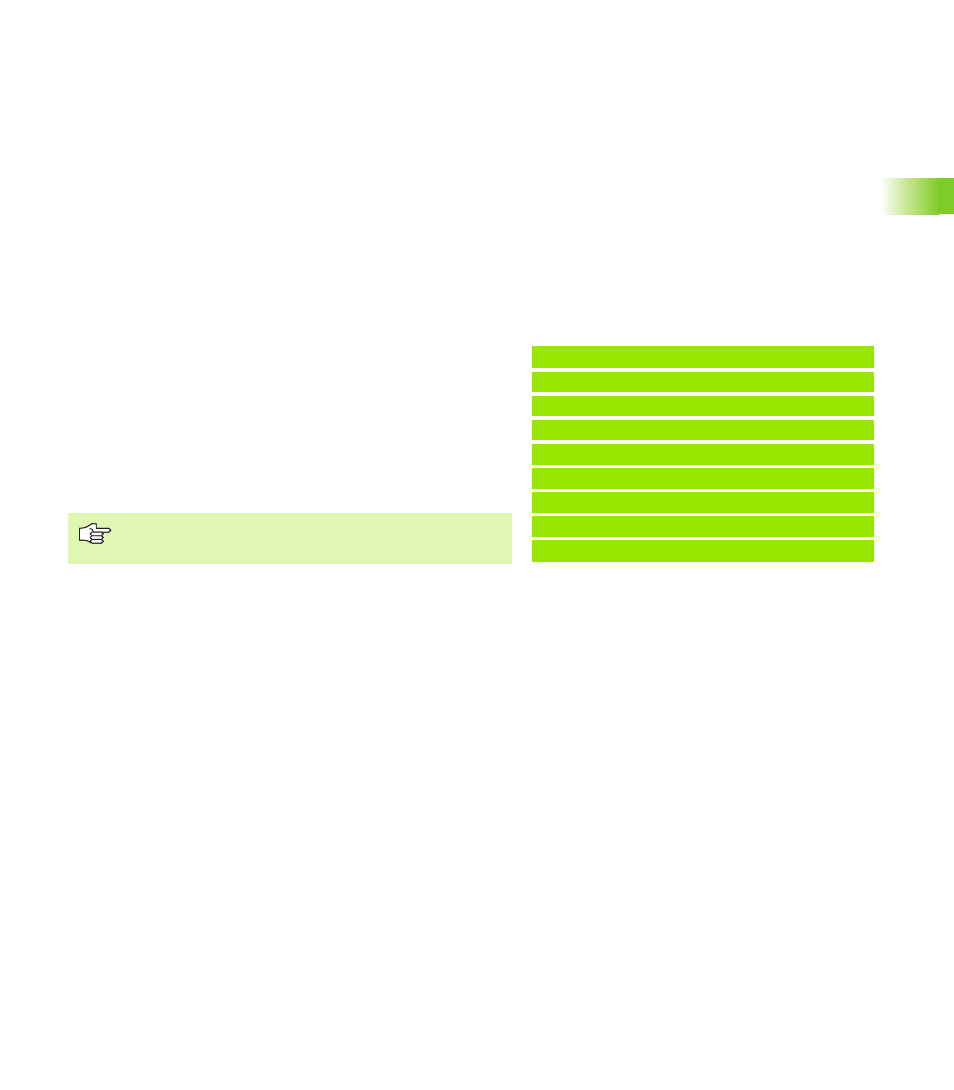
HEIDENHAIN CNC PILOT 4290
237
4.21 Simple T
u
rn
ing Cy
cles
“Oversize” programmed: First roughing, then finishing
G86 machines chamfers at the sides of the recess. If you do not wish
to cut the chamfers, you must position the tool at a sufficient distance
from the workpiece. Calculate the starting position XS (diameter) as
follows:
K
Radial recess: Recess width
K>0: Recess width
No input: Recess width = tool width
Axial recess: Oversize
K>0: Oversize (roughing and finishing)
K=0: No finishing
E
Dwell time (for chip breaking)—(default: length of time for one
revolution)
With finishing oversize: Only for finishing
Without finishing oversize: For every recess
Parameters
Example: G86
. . .
N1 T3 G95 F0.15 G96 S200 M3
N2 G0 X62 Z2
N3 G86 X54 Z-30 I0.2 K7 E2
[radial]
N4 G14 Q0
N5 T8 G95 F0.15 G96 S200 M3
N6 G0 X120 Z1
N7 G86 X102 Z-4 I7 K0.2 E1
[axial]
. . .
XS = XK + 2 * (1.3 – b)
XK:
Contour diameter
b:
Chamfer width
The tool radius compensation: is active.
Oversizes are not taken into account.
Cycle run
1
Calculates the number of cutting passes.
Maximum offset SBF * cutting width
(SBF: See Machining Parameter 6)
2
Approaches to clearance height at rapid traverse on paraxial
path.
3
Executes the first cut, taking finishing oversize into account.
4
Without finishing oversize: Dwells for the time period E
5
Retracts and approaches for next pass.
6
Repeats 2 to 4 until the complete recess has been machined.
7
With finishing oversize: Finish-machines the recess
8
Returns paraxially to starting point at rapid traverse.