Logic configuration – Rockwell Automation IASIMP Computer Numerical Control (CNC) Machining Accelerator Toolkit Quick Start User Manual
Page 68
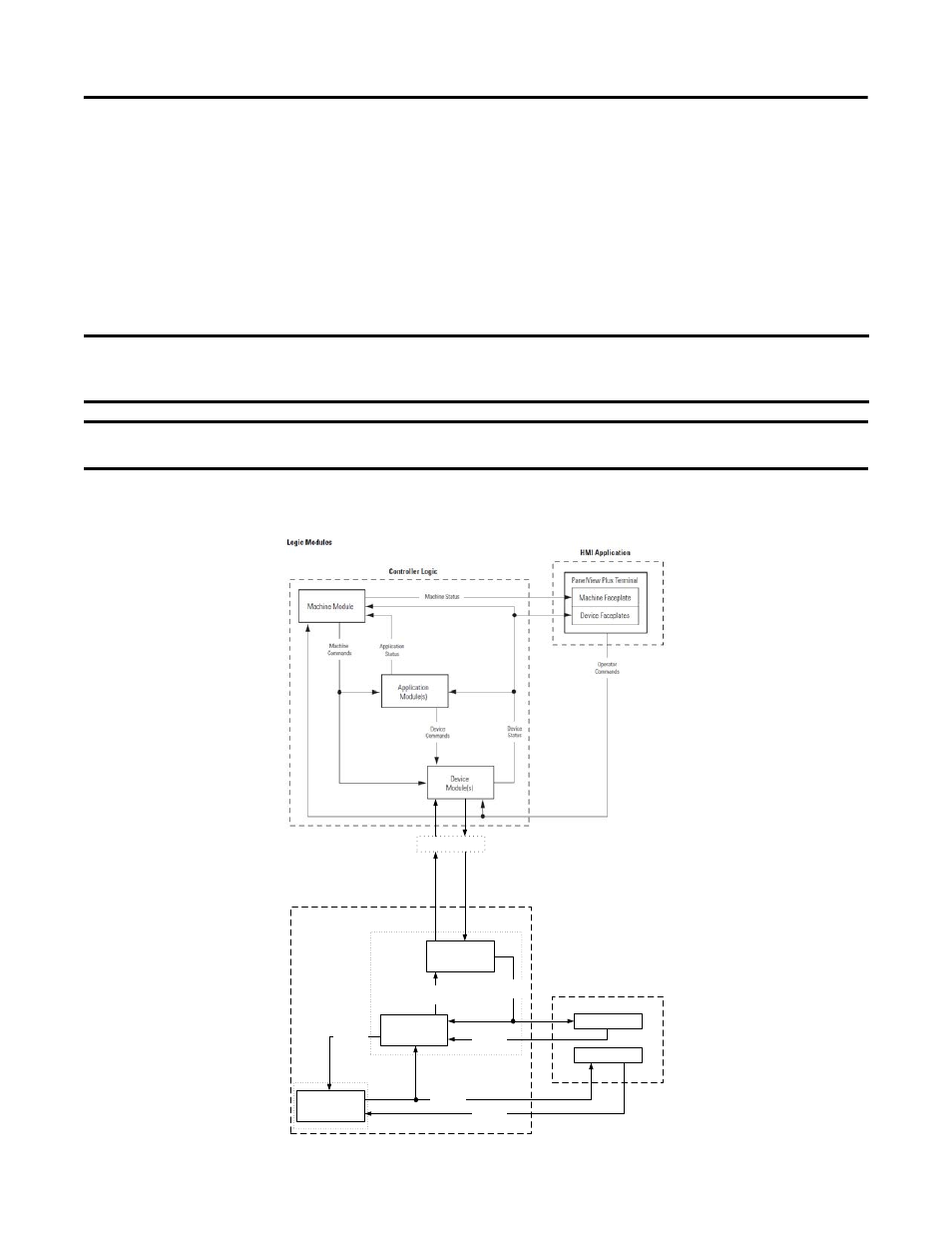
68
Rockwell Automation Publication IASIMP-QS034A-EN-P - October 2012
Chapter 3
FANUC CNC Configuration
Logic Configuration
In this chapter you use the preconfigured PMC logic files and edit them specifically for your application. The
toolkit provides a preconfigured PMC file with application and device modules that significantly speed-up your
application logic development. An initial I/O configuration is provided as well, as an example only.
To assist you in understanding how to best use the preconfigured logic files, the CNC Work Cell application is
used as an example in all of the logic configuration steps.
In this example, the PLC is controlling the machining centers, sending commands over the EtherNet/IP network
to the FANUC CNC devices.
IMPORTANT The overall machine CNC functionality and configuration is not being detailed or explained here. The CNC Machining
Accelerator Toolkit, and this quick start, provide the framework to communicate with the Rockwell Automation
GuardLogix supervisory controller.
IMPORTANT In this example, there is a supervisory PLC that manages an entire work cell consisting of a gantry, and two machining
centers. This PMC program is for one of the machining centers, but could be used interchangeably as a starting point.
Device
Module(s)
Application
Module(s)
Machine Module
CNC
PMC
MDI Panels
Device
Status
Device
Commands
LCD Display
Machine
Status
Operator
Commands
Operator
Commands
CNC/PMC Logic
CNC Operator Panels
Application
Commands
PLC AOP