Yx z 10 – HEIDENHAIN TNC 407 (280 580) ISO Programming User Manual
Page 72
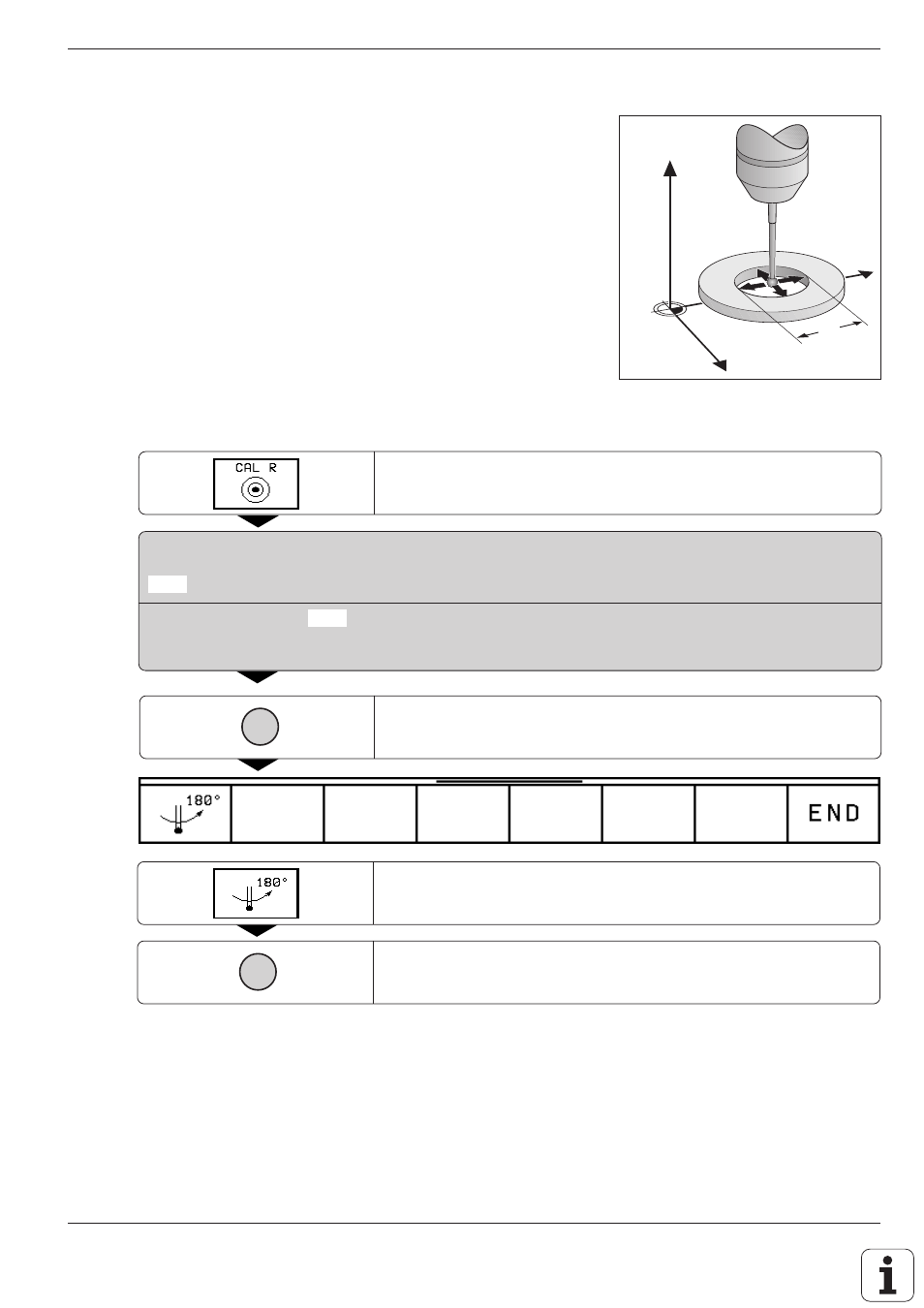
TNC 426/TNC 425/TNC 415 B/TNC 407
2 - 1 1
2
Manual Operation and Setup
Y
X
Z
10
I
I
4x
4x
Fig. 2.10:
Calibrating the touch probe radius
and determining center
misalignment
To calibrate the effective radius
Position the ball tip in the bore hole of the ring gauge.
Compensating center misalignment
After the touch probe is inserted it normally needs to be exactly aligned
with the spindle axis. The misalignment is measured with this calibration
function and automatically compensated electronically.
For this operation the 3D touch probe is rotated by 180°. The rotation is
initiated by a miscellaneous function that is set by the machine tool builder
in the machine parameter MP 6160.
The center misalignment is measured after the effective ball tip radius is
calibrated.
Select the calibrating function for the ball-tip radius and the touch
probe center misalignment.
MANUAL OPERATION
X + X – Y + Y –
TOOL AXIS = Z
RADIUS RING GAUGE = 0
The touch probe contacts a position on the bore in each axis direction;
the effective ball-tip radius is stored.
Determine the ball-tip center misalignment (or terminate the
calibration function with END): rotate the touch probe by 180°.
The touch probe contacts one position on the bore hole for each axis
direction; the touch probe center misalignment is stored.