Contour train (g125) -37, Yx z – HEIDENHAIN TNC 407 (280 580) ISO Programming User Manual
Page 257
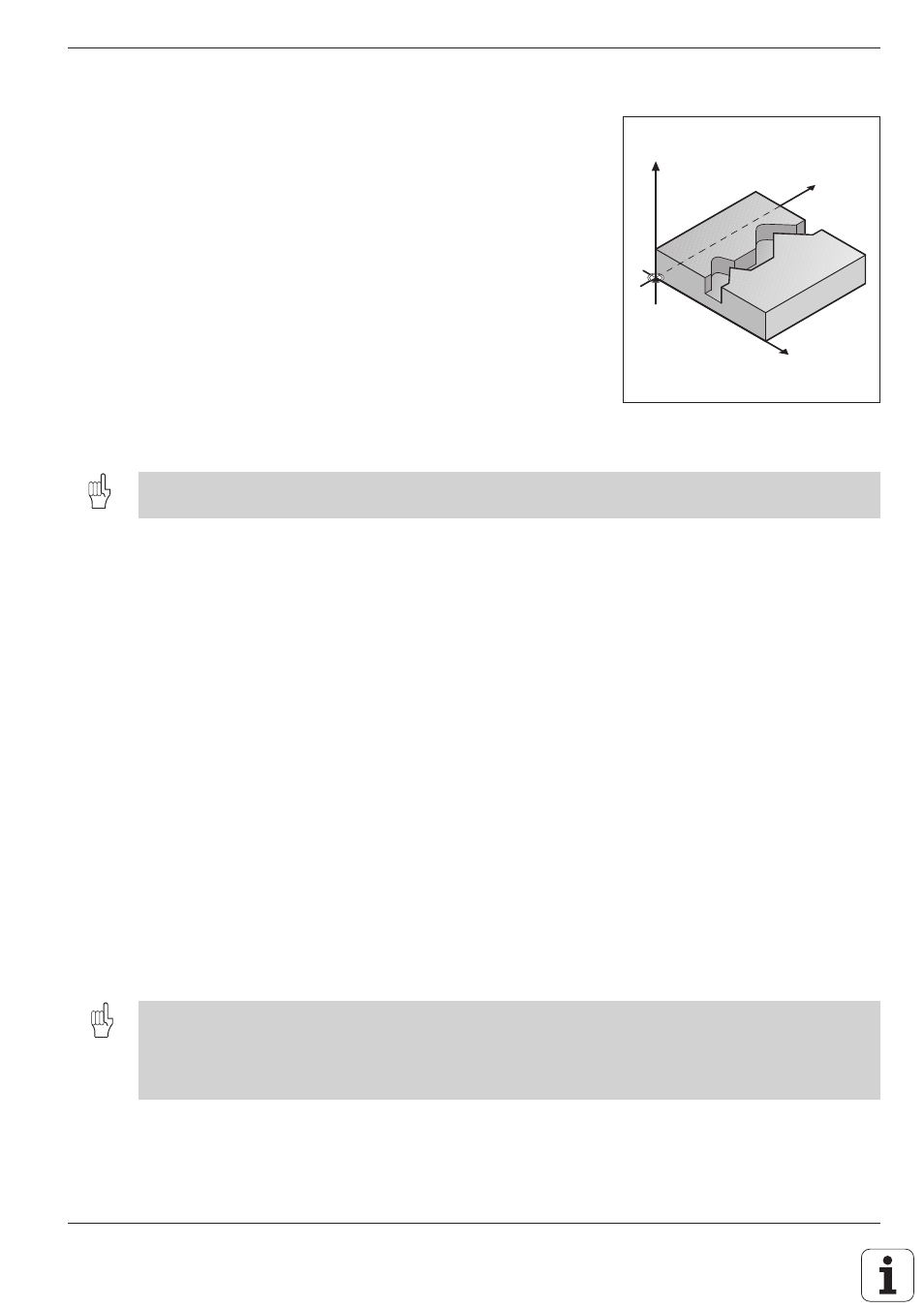
8-37
8
Cycles
TNC 426/TNC 425/TNC 415 B/TNC 407
Fig. 8.41:
Example of an open contour
Y
X
Z
CONTOUR TRAIN (G125)
Sequence
This cycle facilitates the machining of open contours (the starting point of
the contour is not the same as its end point).
G125 CONTOUR TRAIN offers considerable advantages over machining
an open contour using positioning blocks:
• The control monitors the operation to prevent undercuts and surface
blemishes. It is recommended that you run a graphic simulation of the
contour before execution.
• If the radius of the selected tool is too large, the corners of the
contour may have to be reworked.
• The contour can be machined throughout by up-cut or by climb milling.
• The tool can be traversed back and forth for milling in several infeeds.
This results in faster machining.
• Allowance values can be entered in order to perform repeated rough-
milling and finish milling operations.
G125 CONTOUR TRAIN should not be used for closed contours. With closed contours, the starting point and end
point of the contour must not be located in a contour corner.
Input data
• MILLING DEPTH Q1
Distance between workpiece surface and contour floor. The sign
determines the working direction (a negative sign means negative
working direction).
• ALLOWANCE FOR SIDE Q3
Finishing allowance in the machining plane
• WORKPIECE SURFACE COORDINATE Q5
Absolute coordinate of the workpiece surface referenced to the work-
piece datum
• CLEARANCE HEIGHT Q7
Absolute height at which the tool cannot collide with the workpiece.
Position for tool retraction at the end of the cycle.
• PECKING DEPTH Q10
Dimension by which the tool is plunged for each infeed
• FEED RATE FOR PECKING Q11
Traversing speed of the tool in the tool axis
• FEED RATE FOR MILLING Q12
Traversing speed of the tool in the machining plane
• CLIMB OR UP-CUT Q15
Climb milling:
input value =
+1
Up-cut milling: input value = – 1
To enable climb milling and conventional up-cut milling alternately in
several infeeds: input value = 0
• If Cycle G125 CONTOUR TRAIN is used, only the first label from Cycle G37 CONTOUR GEOMETRY will be
processed.
• Each subprogram can contain up to 128 contour elements.
• Cycle G120 CONTOUR DATA is not required.