IAI America SCON-CA User Manual
Page 263
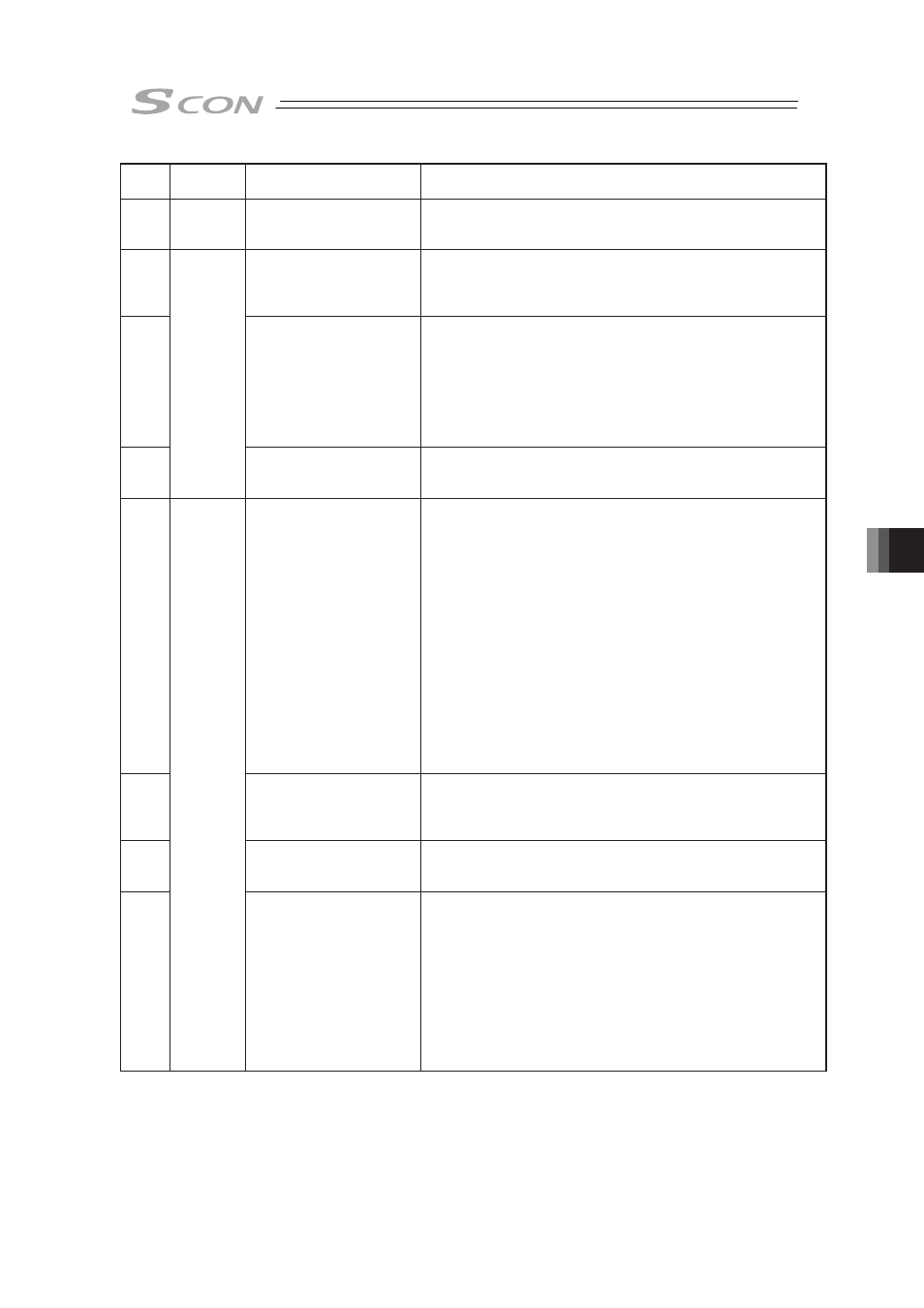
Chapter 9
Troubleshooting
253
Alarm
Code
Alarm
Level
Alarm Name
Cause/Treatment
0CF Operation
release
I/O 24V power supply error Cause
: 24V power supply for PIO is not connected. The
voltage is extremely low.
Treatment : Check the connection and voltage.
0D2
Motor power source
voltage excessive
Cause
: A breakdown of the part inside the controller is
considered.
Treatment : If this error occurs frequently, the controller may be
faulty at high probability. Please contact IAI.
0D3
Motor power supply
voltage low
Cause
: 1) If the power source is shut off out of the
controller, servo-on command was made during
the power is shut.
2) There is a concern of a malfunction of the
controller internal components.
Treatment : 1) Check the controller external circuit.
2) If this error occurs often, there is a concern of a
controller malfunction. Please contact us.
0D7
Cold start
Belt breaking sensor
detected
Cause
: The belt of the ultra-high thrust RCS2-RA13R is
broken.
Treatment : Belt must be replaced. Please contact IAI.
0D8
Deviation overflow
Cause
: This alarm indicates that the position deviation
counter has overflowed.
1) The speed dropped or the actuator stopped due
to the effect of external force or overload.
2) The excited-phase detection operation following
the power-on is unstable.
3) The power supply voltage dropped.
4) Servo gain number is too small
Treatment : 1) This error occurs when the actuator cannot be
operated as it is commanded. Check the load
conditions such as if the work is touching to the
surrounding object, or brake is properly
released, and remove the cause.
2) Overload can be concerned. Revise the
transportable weight and redo the home-return
operation.
3) Check for the source voltage.
0D9
Software stroke limit
exceeded
Cause
: The current position of the actuator exceeds the
software stroke limit.
Treatment : Return the actuator to be within the range of the
software stroke limit.
0DA
Feed back pulse error
Cause
: Feedback pulse data cannot be output within the
cycle.
Treatment : Take proper measures against noise.
0DC
Operation
release
Pressing motion range
over error
Cause
: 1) After the pressing operation has complete, the
force to push back is too large and the pushed
back to the pressing start position (“Position” in
the position table).
2) The actuator touched the work during the
approach movement before the pressing
movement.
Treatment : 1) Revise the setting and adjust it so the force to
push back gets smaller.
2) Set the “Position” setting in front in the position
table to shorten the approach distance.