IAI America SCON-CA User Manual
Page 143
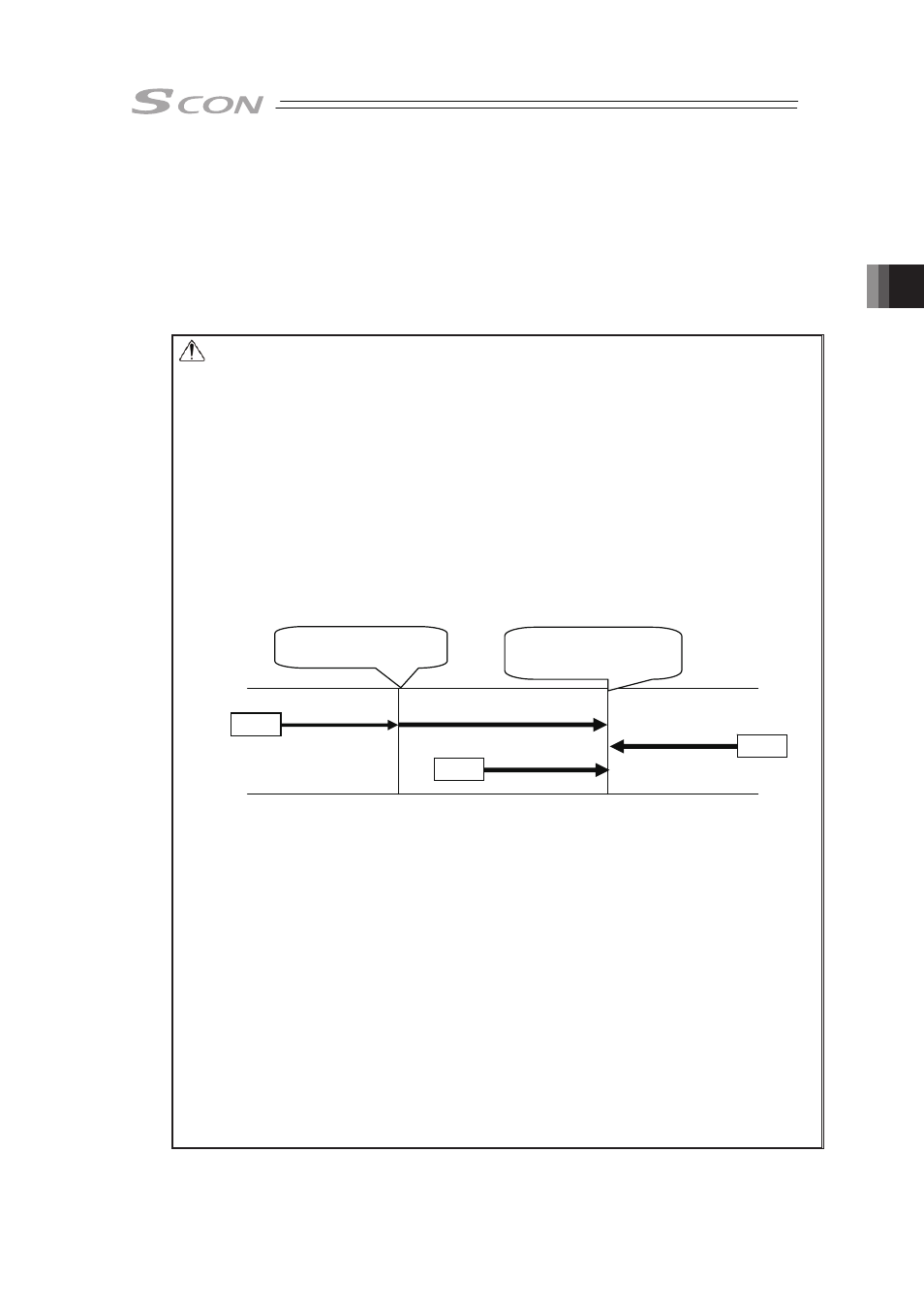
Chapter 3 Operation
133
3) First define the positioning in position No.1. Next, the operation in position No.2 moves the
actuator to the position of 80mm at the setting speed and rating torque and change to the
tension operation. The actuator moves by 50mm in the negative direction in the tension
operation. The upper limit of the tensile force is the torque set in percent.
4) In the similar way as pressing, the positioning complete signal is output when the shaft is
stopped by tension (pressing complete). If the actuator cannot be stopped during
movement within the setting positioning width (miss-pressing), it moves by the setting
distance to stop but PEND is not turned ON. The current position No. PE* is turned on at
the completion of pressing and even in miss-pressing.
� �
Caution: (1) The speed during tension operation is set in Parameter No.34. Check the
10.4 List of Specifications of Connectable Actuators for the pressing
opration speed. The speed for tension operation is same as that for
pressing operation.
Do not set any value larger than the value in the list. If the speed set in the
position table is equal to or less than the tension speed, the tension
operation is performed at the setup speed.
(2) The tension ready position should be the tension start position or forward. If
not, the moving direction varies depending on the start position to be
dangerous.
The tension operation from a coordinate (less than 30mm = 80 – 50 in the
above example) located before the end position (30mm) changes to the
pressing operation from the current position to the tension end position.
Please note that it cannot be the tension operation to the point of 30mm
after the positioning at the point of 80mm.
(3) The work is pulled also after completion of the tension. The work is drawn
back or pulled further if the work is moved. When the work is drawn back
before the approach position, alarm code 0DC “Pressing Motion Range
Over Error” occurs to stop the work. When the work is moved in the tension
direction and the load current becomes less than the current limit value
(pressing in percent), PEND is turned OFF. Miss-pressing occurs when the
actuator moves by the pressing moving distance set in “Positioning width”.
Current Position No. PE* keeps turned on until the next movement
command is made even if the work piece gets moved and pulled backward
or further forward once it is turned on at the tension operation complete.
(4) Tension operation cannot be performed with the rotary actuator.
(5) If the actuator is RCS2-RA13R (Ultra-High Thrust Type), there is a limit in
the continuous tension time (= continuous pressing time) and the duty of
continuous pressing. Use of the product above this limit may cause a
failure occurred due to the motor heat generation.
[Refer to 10.4.2 Specifications and Limitations in Pressing Operation of
RCS2-RA13R]
Pressing Operation
ST*: Start position
ST*
ST*
ST*
Tension Operation
Approach Operation
Tension Operation
Tension start position
80mm
Tension end position
80 – 50 = 30mm