IAI America SCON-CA User Manual
Page 246
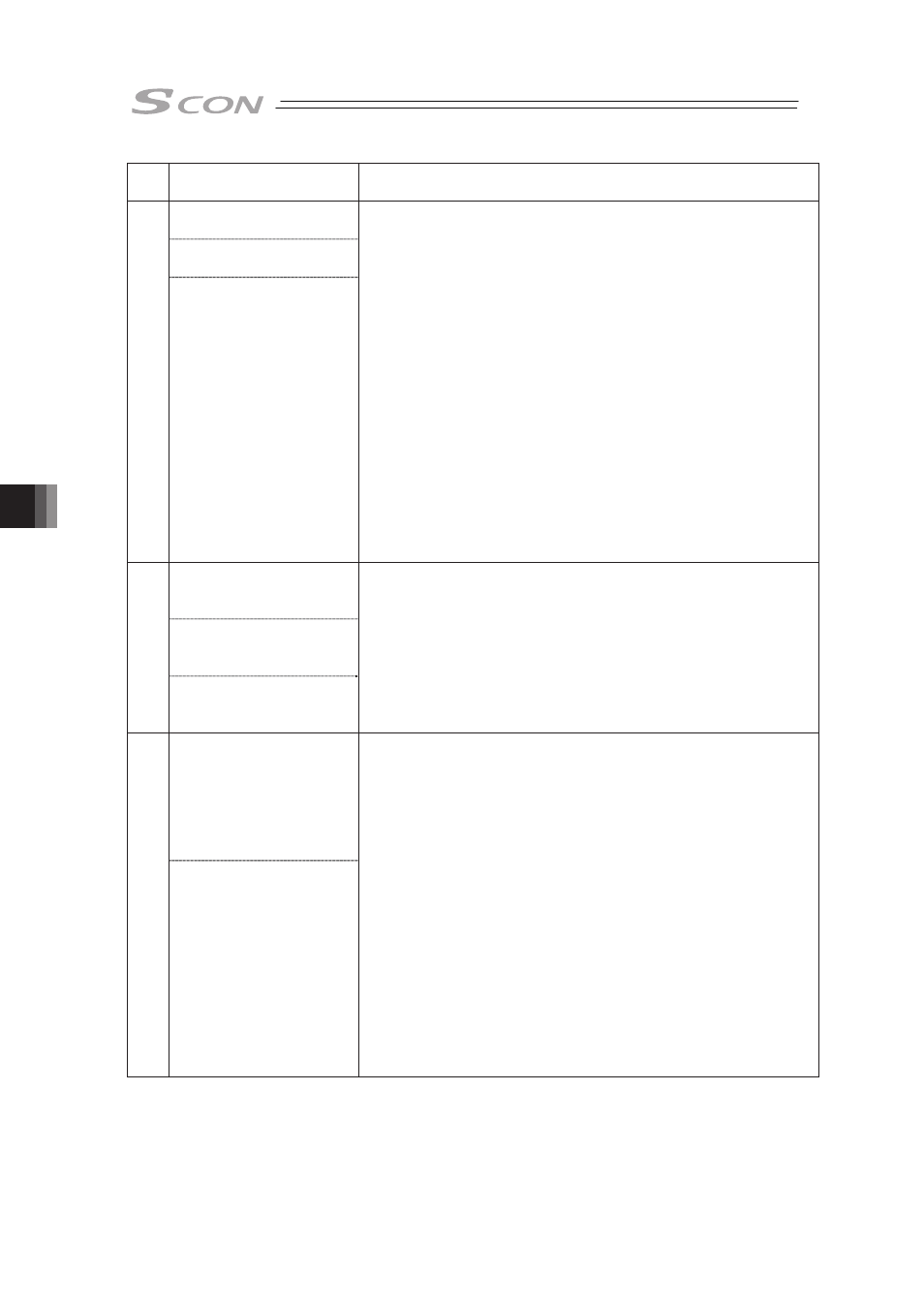
Chapter 8 I/O Parameter
236
No.
Situation that requires
adjustment
How to Adjust
Trace precision is desired
to be improved.
Equi-speed performance
is desired to be improved.
5
Response is desired to be
improved.
�
Make the condition optimized with Parameter No.7 “Servo gain
number” and Parameter No.31 “Velocity loop proportional gain”
adjusted by referring to the way to adjust stated in No. 1 to 3 in
the previous page.
[Reference]
The most important factor is to select the actuator (motor).
The servo is extremely sensitive to the inertia of the load. If the
inertia moment of the load is too large in comparison with the
inertia moment of the servo motor itself, the motor is highly
affected by the load. This may cause the actuator to be
controlled unstably.
Therefore, to improve the precisions of the trace, position, speed
and response of the actuator, the load inertia ratio must be made
small.
For high trace precision, equi-speed performance, and response
of the actuator in such a use as application, it is better to use ball
screws with small leads in the actuator as much as possible and
an actuator of motor capacity higher by at least one level.
The best method is to calculate the load inertia to select the
proper actuator.
Large static friction of load
makes actuator start
slowly.
Large load inertia makes
response of actuator low
at start and stop.
6
Takt time is desired to be
shortened.
�
Set parameter No.71 “Feed forward gain”.
Select a value in the range from 10 to 50 roughly. The larger the
setting value is, the smaller the deviation is. Then the response
is improved.
Setting a large value may cause vibrations and/or noises to
occur.
Set the feed forward gain in order to improve the response of
the actuator further after adjusting Parameter No.7 “Servo gain
number” and Parameter No.31 “Speed loop proportional gain”.
(Pulse train control)
An abnormal noise is
generated in
acceleration/deceleration
and Alarm Code 0D8
“Deviation Overflow” is
issued and stopped.
7
There is an impact at the
start or stop.
�
Change the setting in Parameter No.55 “Position command
primary filter time constant” to approximately 50ms.
If there is no improvement in situation, try to increase the setting
gradually. If there is an improvement, try to decrease the setting
gradually to the boundary. Making a change to this setting will
make the settling time longer thus the takt time also becomes
longer. The accuracy for the positioning also becomes worse. It
is recommended, to solve the problem from the root cause, to
replace the host positioning unit with one that is equipped with
acceleration/deceleration function.
[Important]
�
There is a case that the acceleration/deceleration setting of the
host controller (PLC) to output the pulse train is not appropriate,
or the host controller is not equipped with this type of function.
Tune the setting to the appropriate one (in the range it does not
exceed the actuator acceleration/deceleration capability) if there
is the acceleration/deceleration function.
If there is not, tune the setting by using Parameter No.55.