IAI America SCON-CA User Manual
Page 251
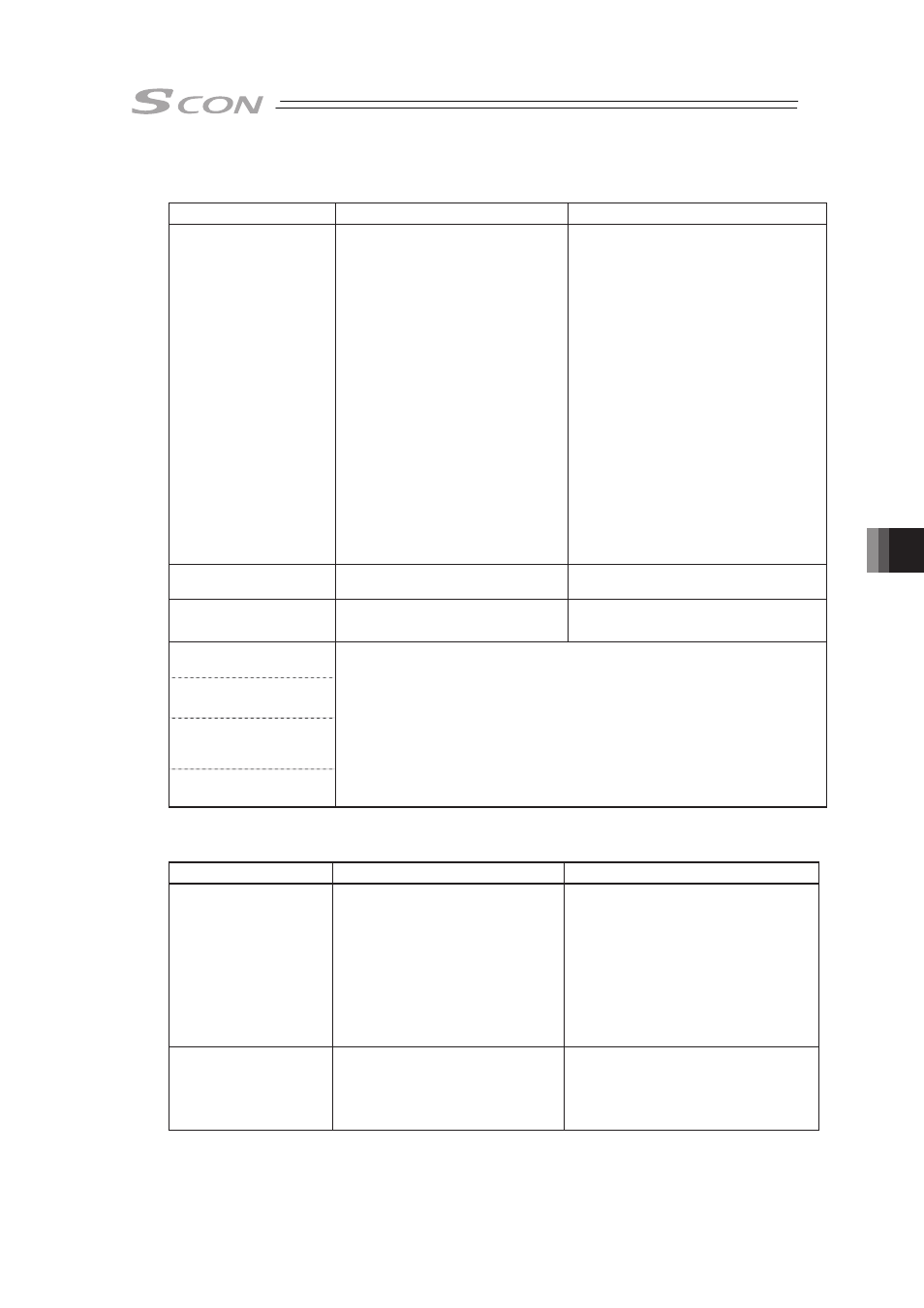
Chapter 9
Troubleshooting
241
9.2.2 Positioning and speed of poor precision (incorrect operation)
Situation
Possible cause
Check/Treatment
Completion of operation
on the way to home
return
In the home return of our standard
specification, the actuator is first
pressed to the mechanical end,
moved oppositely, and subject to
positioning stop at the home
position. Therefore, the product may
judge as the mechanical end even
though it is still on the way when the
load is large and interfere with
surrounding object.
1) A load exceeding its rating
weight is installed on the
actuator.
2) It is touched to interference in
the way of the run.
3) Torsion stress is applied to guide
due to improper fixing method of
the actuator or uneven fastening
of bolts.
4) The sliding resistance of the
actuator itself is large.
1) Reduce the load.
2) Remove the interference.
3) Loosen the fixing bolts once and
check whether the slider can move
smoothly.
If the slider can move smoothly,
check if there is a deformation on the
attached surface, and install the
actuator again following the
instructions stated in Instruction
Manual.
4) Please contact IAI.
Shocks at start and/or
stop.
Acceleration/deceleration is set too
high.
Decrease the settings of
acceleration/deceleration.
Overshoot during
deceleration to stop.
The load inertia is large.
Decrease the setting of deceleration.
[Refer to 9.3.]
Positioning of poor
precision
Uneven speed during
movement
Acceleration/deceleration
not smooth (bad speed
response)
Trace of poop precision
[Refer to 8.3 Servo Adjustment.]
(Note) When the pulse-train operation mode is selected, first adjust
pulse-train commands.
[In the case of Positioner Mode]
Situation
Possible cause
Check/Treatment
Positioning at a position
different from that of
commanded position No.
PIO signal processing is incorrect.
1) Start signal CSTR is input too
early after position No.
command. Or position No.
command and start signal are
input concurrently.
2) The correct position No. is not
specified due to PIO signal
disconnection or poor connector
contact.
1) The stop position may be set for
another purpose. Input the start
signal after the controller fully reads
the position number.
[Refer to 3.2.4 Operation with the
Position No. Input = Operations of
PIO Patterns 0 to 3. Creating
Sequence Program.]
2) Check the input signal on I/O
monitor on the teaching tool.
Complete signal PEND
is not output even
though positioning
process is completed.
PIO signal processing is incorrect.
1) Start signal CSTR is not turned
OFF.
1) Make the start signal CSTR turned
OFF before completing the
positioning process by the turn-off of
positioning complete signal PEND
after starting operation, and so on.