Chapter 8 i/o parameter, I/o parameter list (continued) – IAI America SCON-CA User Manual
Page 208
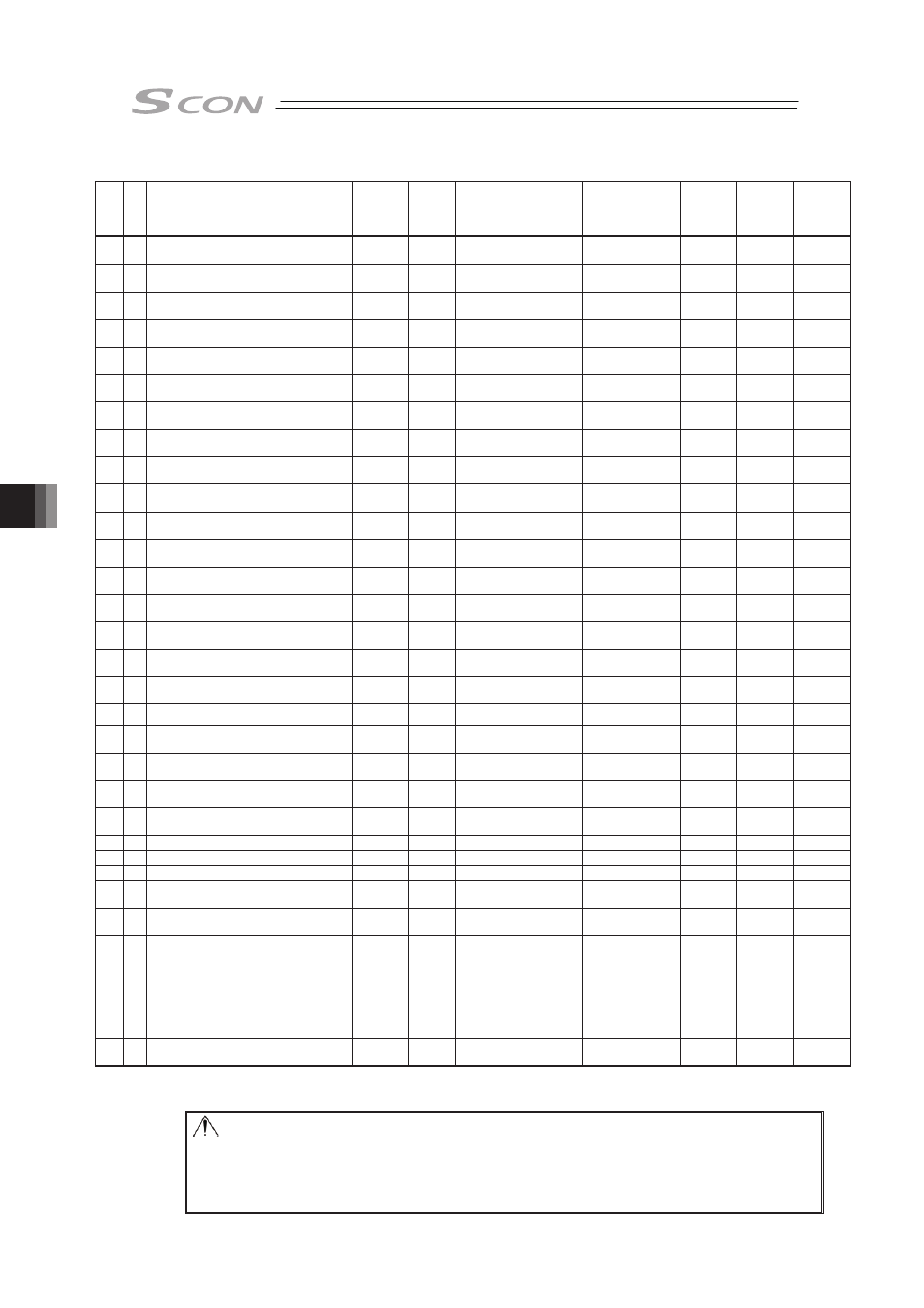
Chapter 8 I/O Parameter
198
I/O Parameter List (Continued)
No.
C
at
eg
or
y
Name
Symbol
Unit
Input Range
Default factory
setting
for
Positione
r Mode
for Pulse
Train
Mode
Relevant
sections
121 C Feed forward gain 1
PLF1
–
0 to 100
In accordance
with actuator
(Note2)
�
8.2 [57]
122 C Velocity Loop Proportional Gain 1
VLG1
–
1 to 27661
In accordance
with actuator
(Note2)
�
8.2 [23]
8.3
123 C Velocity Loop Integral Gain 1
VLT1
–
1 to 217270
In accordance
with actuator
(Note2)
�
8.2 [24]
8.3
124 C Torque Filter Time Constant 1
TRF1
–
0 to 2500
In accordance
with actuator
(Note2)
�
8.2 [25]
8.3
125 C Current control width number 1
CLP1
–
0 to 4
In accordance
with actuator
(Note2)
�
8.2 [40]
8.3
126 C Servo gain number 2
PLG2
–
0 to 31
In accordance
with actuator
(Note2)
�
8.2 [5]
8.3
127 C Feed forward gain 2
PLF2
–
0 to 100
In accordance
with actuator
(Note2)
�
8.2 [57]
128 C Velocity Loop Proportional Gain 2
VLG2
–
1 to 27661
In accordance
with actuator
(Note2)
�
8.2 [23]
8.3
129 C Velocity Loop Integral Gain 2
VLT2
–
1 to 217270
In accordance
with actuator
(Note2)
�
8.2 [24]
8.3
130 C Torque Filter Time Constant 2
TRF2
–
0 to 2500
In accordance
with actuator
(Note2)
�
8.2 [25]
8.3
131 C Current control width number 2
CLP2
–
0 to 4
In accordance
with actuator
(Note2)
�
8.2 [40]
8.3
132 C Servo gain number 3
PLG3
–
0 to 31
In accordance
with actuator
(Note2)
�
8.2 [5]
8.3
133 C Feed forward gain 3
PLF3
–
0 to 100
In accordance
with actuator
(Note2)
�
8.2 [57]
134 C Velocity Loop Proportional Gain 3
VLG3
–
1 to 27661
In accordance
with actuator
(Note2)
�
8.2 [23]
8.3
135 C Velocity Loop Integral Gain 3
VLT3
–
1 to 217270
In accordance
with actuator
(Note2)
�
8.2 [24]
8.3
136 C Torque Filter Time Constant 3
TRF3
–
0 to 2500
In accordance
with actuator
(Note2)
�
8.2 [25]
8.3
137 C Current control width number 3
CLP3
–
0 to 4
In accordance
with actuator
(Note2)
�
8.2 [40]
8.3
138 C Servo gain switchover time constant
GCFT
ms
10 to 2000
10
�
8.2 [108]
139 A Home preset value
PRST
mm
-9999.99 to 9999.99
In accordance
with actuator
(Note2)
�
�
8.2 [109]
140 B IP Address
IPAD
–
0.0.0.0 to
255.255.255.255
192.168.0.1
–
Separate
volume
141 B Subnet Mask
SNMK
–
0.0.0.0 to
255.255.255.255
255.255.255.0
–
Separate
volume
142 B Default Gateway
DFGW
–
0.0.0.0 to
255.255.255.255
0.0.0.0
–
Separate
volume
143 B Overload Level Ratio
OLWL
%
50 to 100
100
�
�
8.2 [113]
147 B Total Movement Count Threshold
TMCT
Times
0 to 999999999
0 (Disabled)
�
–
8.2 [114]
148 B Total Operated Distance Threshold
ODOT
m
0 to 999999999
0 (Disabled)
�
�
8.2 [115]
149 B Zone Output Changeover
FPIO
–
0: Not to change
1: To change
0
�
–
8.2 [116]
150 A Linear Absolute Home Preset Value
LAPS
mm
-9999.99 to 9999.99
In accordance
with actuator
�
�
8.2 [117]
151 B Light Error Alarm Output Select
FSTP
–
0:
0: Battery Voltage
Drop Warning
Output
1: Output of
battery voltage
drop warning or
message-level
alarm
�
�
8.2 [118]
159 B FB Half Direct Mode
FBVS
–
0: 1mm/s unit
1: 0.1mm/s unit
0
�
Separate
volume
Note 2: The setting values vary in accordance with the specification of the actuator. At shipment, the
parameters are set in accordance with the specification.
Caution: When the controller is operated via serial communication, always set the
controller in the “positioner mode” (piano switch 1: OFF).
If it happens to be in the “pulse train mode” by mistake, the controller may
operate erratically because it is operated according to the “pulse train mode”
parameters.