Chapter 8 i/o parameter, I/o parameter list (continued) – IAI America SCON-CA User Manual
Page 206
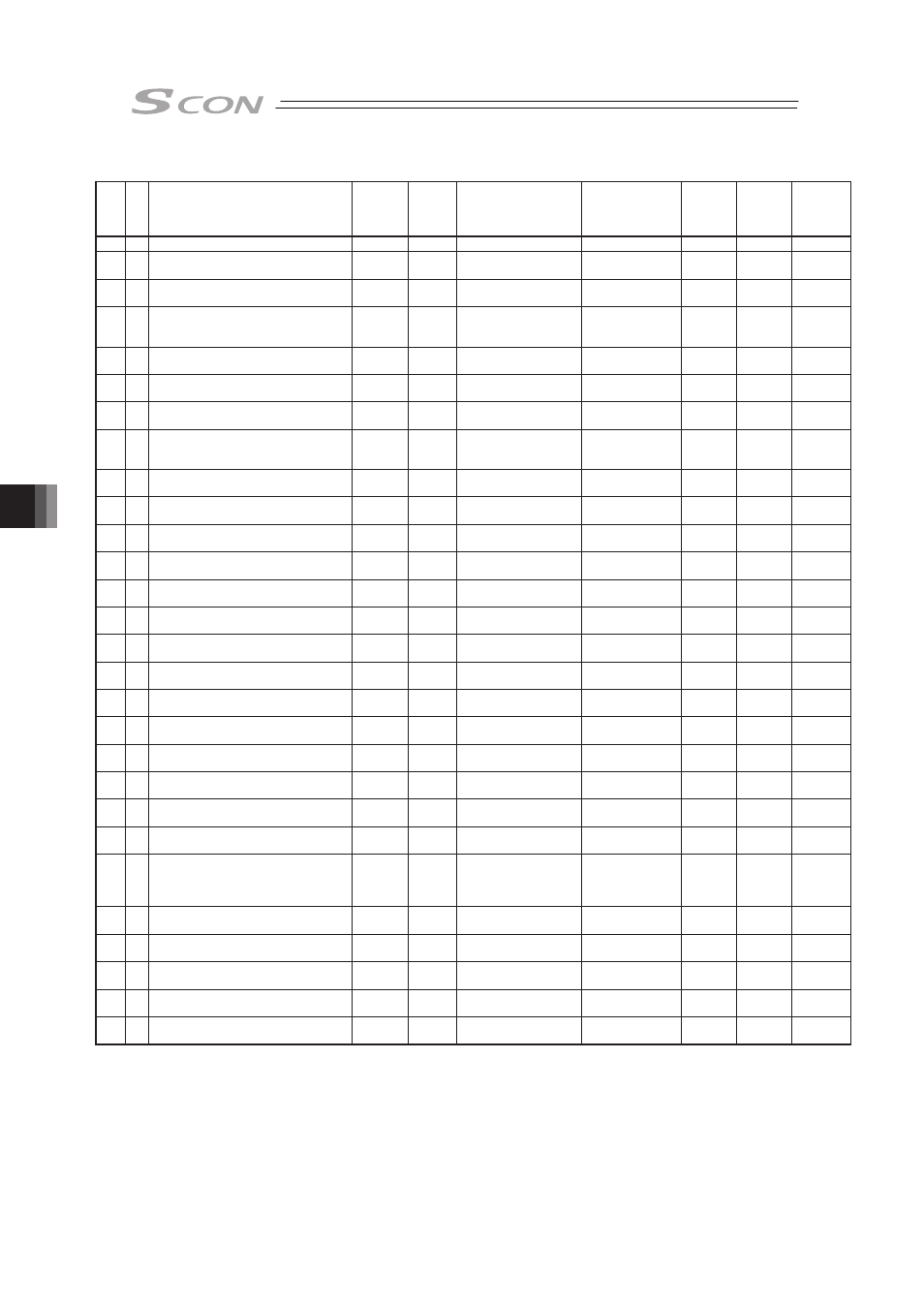
Chapter 8 I/O Parameter
196
I/O Parameter List (Continued)
No.
C
at
eg
or
y
Name
Symbol Unit
(Note1)
Input Range
Default factory
setting
for
Positioner
Mode
for Pulse
Train
Mode
Relevant
sections
66 B Electronic Gear Denominator
CDEN
–
1 to 4096
125
�
�
3.3.4
67 B Compulsory Stop Input
FPIO
–
0: Enabled,
1: Disabled
0
�
3.3.6
68 B Feedback Pulse Output
FPIO
–
0: Enabled,
1: Disabled
1
�
�
3.3.5
69 B Feedback Pulse Train
FBPT
–
0 to 2
0
(A/B Phase Pulse
String)
�
�
3.3.5
70 B Feedback Pulse Form Polarity
FBPT
–
0: Positive Logic
1: Negative Logic
0
�
�
3.3.5
71 B Feed forward gain
PLFG
–
0 to 100
0
�
�
8.2 [57]
8.3
72 E Timer period for emergency stop relay
fusing monitor
EMWT
msec
0 to 60000
3000
�
�
8.2 [58]
73 D Encoder voltage level
EVLV
–
0 to 3
Depending on
encoder cable
length
(Note2)
�
�
8.2 [59]
74 C PIO Power Supply Supervision
FPIO
–
0: Enabled,
1: Disabled
0
�
�
8.2 [60]
75 D Electromagnetic brake power monitor
FSTP
–
0: Disabled,
1: Enabled
In accordance with
actuator
(Note2)
�
�
8.2 [61]
76 D Belt breaking sensor input polarity
AIOF
–
0 to 2
In accordance with
actuator
(Note2)
�
�
8.2 [62]
77 D Ball Screw Lead Length
LEAD
mm
0.01 to 999.99
In accordance with
actuator
(Note2)
�
�
8.2 [63]
78 D Axis operation type
ATYP
–
0: Line Axis
1: Rotary Axis
In accordance with
actuator
(Note2)
�
8.2 [64]
79 B Rotary axis mode selection
ATYP
–
0: Normal Mode
1: Index Mode
In accordance with
actuator
(Note2)
�
8.2 [65]
80 B Rotational axis shortcut selection
ATYP
–
0: Disabled,
1: Enabled
In accordance with
actuator
(Note2)
�
8.2 [66]
84 A Field bus operation mode
(Note4)
FMOD
–
0 to 8
Separate volume
�
Separate
volume
85 A Field Bus Node Address
(Note4)
NADR
–
0 to 127
Separate volume
�
Separate
volume
86 A Field bus baud rate
(Note4)
FBRS
–
0 to 4
Separate volume
�
Separate
volume
87 E Network Type
(Note4)
NTYP
–
0 to 7
Separate volume
�
Separate
volume
88 D Software limit margin
SLMA
mm
(deg)
0 to 9999.99
In accordance with
actuator
(Note2)
�
�
8.2 [71]
89 D Allowable time of exceeding torque
allowing continuous pressing
PSCT
sec
0 to 300
In accordance with
actuator
(Note2)
�
8.2 [72]
90 C Field I/O format
(Note4)
FPIO
–
0 to 3
Separate volume
�
Separate
volume
91 C Current limit value at stopping due to
miss-pressing
FSTP
–
0: Current limit value
during movement
1: Current limit value
during pressing
0
�
8.2 [74]
92 C Use of loadcell
FFRC
–
0: Not Applicable
1: Use
In accordance with
actuator
(Note2)
�
8.2 [75]
93 C Selection of pressing control
FFRC
–
0: Current limit
1: Force sensor
In accordance with
actuator
(Note2)
�
8.2 [76]
94 C Pressing operation using force sensor
gain
FRCG
–
100 to 30000
1500
�
8.2 [77]
95 C Force judgment margin +
FJMM
%
1 to Maximum Pressing
Force
In accordance with
actuator
(Note2)
�
8.2 [78]
96 C Force judgment margin -
FJML
%
1 to Maximum Pressing
Force
In accordance with
actuator
(Note2)
�
8.2 [78]
Note 1 The unit (deg) is for rotary actuator. It is displayed in mm in the teaching tools.
Note 2 The setting values vary in accordance with the specification of the actuator. At shipment, the
parameters are set in accordance with the specification.
Note 4 These parameters are exclusively used for the field network. Set the parameters according to the
Instruction Manual of each field network, a separate volume.